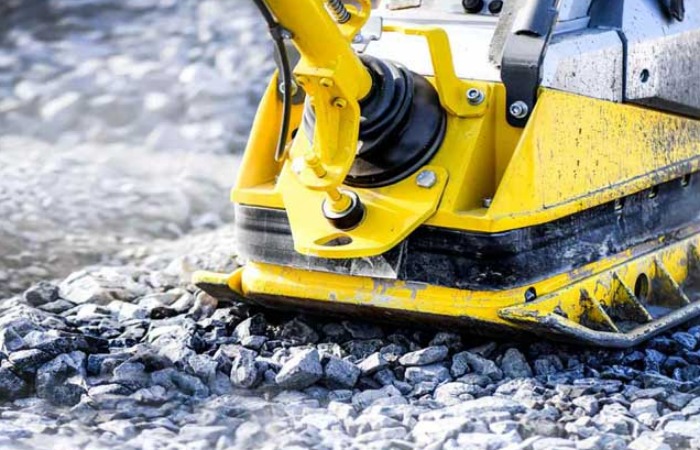
Safety in Selecting Compaction Equipment
The top priority in road building is crew member safety. But conventional compaction equipment is about as inflexible as it gets. Operators sweat down the sloping road shoulders and ditches, risking a rollover but praying for the best as they feel every degree of slope. Although rollover protective structures (ROPS), seatbelts, and personal protective equipment (PPE) like hard helmets have been demonstrated to be effective at saving lives in compactor rollover accidents, they are not very effective for averting a disaster altogether.
Some manufacturers are redesigning the compaction process from the ground up in order to overcome the main challenges posed by conventional compaction rollers, including risk, excessive maintenance, and limited utility. When considering a new compaction roller, here is what to look for.
Safety-Focused Design
Manufacturers' perception that the compaction drum is a source of motion, compaction, and stability all in one has been the main barrier to compaction safety. On the other hand, the safety concern is quickly resolved by moving the drum to an offset arm attachment. The compaction roller can now be linked to graders, compact track loaders, wheel loaders, or skid steers as an accessory. These hosts offer a separate source of power for the compaction drum as well as stability and operator safety due to the offset arm.
With this configuration, an operator is now able to compact level areas as well as run the host machine on flat ground while the arm extends to the farthest, steepest edge of sloping road shoulders and ditches. Improving safety to this extent puts a major dent in workers comp claims, lowers insurance premiums, and increases safety ratings ” a necessity to contractors bidding on competitive jobs.
Shifting the drum to an offset arm attachment drastically improves safety, but it can also unlock a host of other benefits.
Minimal Maintenance Downtime
The onboard engine, transmission, and other connected equipment are no longer present because the compaction roller is now an independent device. Look for an attachment that offers a universal mounting pad and straightforward hydraulic connections for a smooth setup and disconnect to the host machine to further save downtime.
Think about remote-controlled possibilities as well. The operator can make all adjustments from the palm of their hand and without leaving the host machine's cockpit using certain compaction roller attachments that can be quickly attached to the remote.
Typically, aside from a handful of grease fittings to maintain and clean off debris, compaction roller attachments have no maintenance to speak of ” no more oil changes, filters, transmission fluid or any hard parts to wear and break. This can make for 90 per cent less maintenance over self-propelled machines. Cutting out the unnecessary bulk seen with traditional compaction machines also allows manufacturers to design a more compact, versatile machine.
Easy Adjustability & Transportability
Since the compaction drum no longer needs to support and move the machine, manufacturers may now offer variable drum diameters to accommodate different applications from clients. Contractors would need to buy several self-propelled machines, each with an engine and transmission that will ultimately fail and require upkeep and pricey repairs, in order to achieve the same benefit as conventional compaction machines. Transport is also made simpler by the compact size of compaction roller attachments. A typical pickup truck can pull many of these, and they can all fit on a shared trailer with the host equipment.
Look for a device that not only enables remote-controlled modifications of the attachment arm but also of the drum itself for more adaptability. Some drums have a 30-degree pivot and can extend up to 30 inches below the mounting point of the arm. Because of this, slopes at different angles can be compacted by the roller without difficulty.
Compaction roller attachments can easily surpass their conventional equivalents in every way during a busy roadwork season. These attachments prevent an engine from lying idle and progressively deteriorating into a surprise repair charge when the next season comes along. But more crucially, offset-designed compaction roller attachments boost crew safety and offer a multipurpose piece of machinery that will outlast any conventional compaction machine in a road crews fleet. Customers may buy with confidence knowing that they will receive the best possible return on their investment.