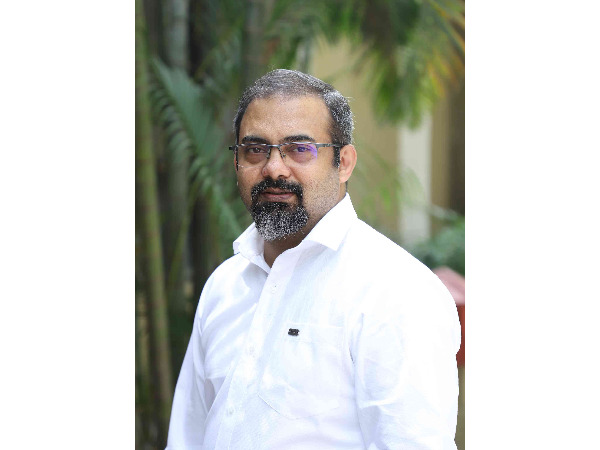
“Digitalisation plays a major role in today’s mining operation.”
What is the current scenario of underground mining in India?
Epiroc Mining India recognises today’s sobering reality about the environment and has accelerated its efforts to raise environmental awareness and drive better action towards zero carbon emission. Major players in the industry are bracing themselves for challenges such as rapid increase in production with mechanisation and cost reduction while under an expansion spree to increase their production capacities to meet domestic and global supply demand. Exploration is being carried out at various locations in the country to identify new mineral reserves.
How digitalisation plays a role in making underground mining sustainable?
Digitalisation plays a major role in today’s underground mining operation and major companies are focussing on AI/ML based analytical modules, IoT smart sensors on remote equipment, condition – based monitoring and Real time reliability health index (RHI) of critical assets, automated process data analysis, 3D mine visualisation mine production planning for asset tracking which benefits in improved safety (people and assets) and availability, reliability and efficiency of equipment process optimisation and higher efficiency. This digitalisation trend is bringing the mining industry closer to intelligent unmanned mining. Epiroc Mining India is geared up with all such offerings to enhance the productivity, safety and peace of mind of our customers.
The future of the underground mining equipment market in India looks bright. What do you think are the major growth drivers in this segment?
As of FY22, the number of reporting mines in India is estimated at 1,245, electric vehicles (EVs) are a globally recognised means to alleviate dependence on petroleum products and reduce CO2 emissions.
Major growth drivers for underground minerals are in high demand. The projected demand of copper due to electric vehicles is expected to increase many folds.
Zinc and lead will be driven by strong growth in India led by 5G roll-out, 100 per cent electrification target, smart cities project, emerging technology for battery application led by automotive sector and inverter battery market and emerging opportunity of storing electricity generated from photovoltaics.
Could you elaborate on your range of equipment for underground mining?
Epiroc has been a leading supplier of mining and rock excavation equipment with focus on maximising production with safe, cost-effective and sustainable solutions. This is reflected in our development and manufacture of quality rock drills, face drilling and production drilling rigs, underground loaders and trucks, electric/battery haul loaders and trucks, ventilation systems and digging arm loaders. Our underground equipment’s production plants are located at Sweden, China and India.
Major equipment used in underground metal mining operations are:
• Development: Single and double boom drill jumbo
• Production: Long hole production drills
• Loaders: Load haul dumpers – diesel/ electric/ battery
• Trucks: Low profile dump trucks – diesel/ electric/ battery
• Bolters: Cable and bolters machines
• Raise boring machines and mobile miners
• Grouting and ventilation system
What are the new developments in equipment and technologies in underground mining? How IoT and digital technologies are evolving in underground mining?
Automation and digitalisation are technology shifts that are happening quickly. To keep pace with new technology in underground mining and enhancing our focus in these vital areas and better meet the needs of customers, Epiroc has introduced digital products and services that can deliver long-term competitive solutions.
Epiroc Mining Intelligence (Mobilaris): From a cost effective deployment and reuse of existing datacom infrastructure, Mobilaris can deliver a Mining Intelligence Solution that:
• Increases the overall production efficiency between 10 to 20 per cent
• Lowers operational costs
• Increases the personal safety in underground mines
• Delivers position data and decision support to other existing mine automation applications
MineRP Platform: An open, standards-based digital integration platform to mines of all types, commodities and locations. With the MineRP Platform, the fragmented technical services domain is instantly integrated, and mine planning from life of mine to detail shift-scheduling becomes fast and collaborative.
Certiq:
• By connecting machines with Certiq the whole global fleet can be monitored
• The data is communicated via mobile network, satellite, Wi-Fi or whatever available
• All data is then processed in our central server and made available to all users
• The customer can access the data on the web portal, via sms, reports or integrated into their ERP system
Automation: Automation-concept contains four levels of automation. From data monitoring and product function control, to calculated optimisation and in the end full autonomy. Combining all steps allows you to reach the full potential of Epiroc’s equipment. When the machines work together they can perform very complicated tasks, deep underground. And they can do so with minimal downtime and maximum safety.