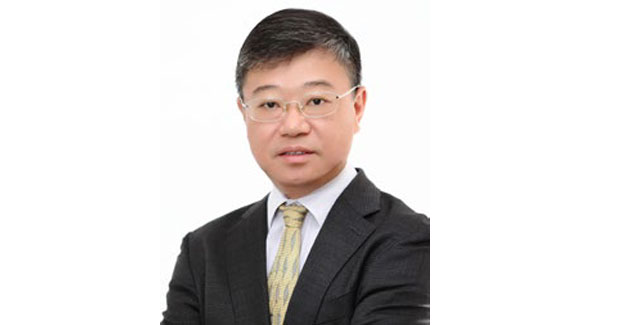
Advancements in Bearings for Construction Machinery
Construction machinery is characterised by its ability to perform in the harshest environments. Machinery such as excavators, dozers, compactors, cranes and dumpers have tremendously increased development capacity. Mobility and movement, the two key factors of the machinery, require bearings and bushings.<p></p><p> <span style="font-weight: bold;">Bushings</span><br />Bushings are mounted in a number of applications including the suspension system, axles, steering joints, linkages, pivots and hydraulic cylinders. They absorb impact, take loads, reduce noise and control the amount of movement in joints.</p><p>Materials most commonly used for these applications consist of steel and bronze. Steel tends to be more cost-effective and have the ability to take higher loads than bronze. However, steel needs regular lubrication. Since construction machines can run 24-hours at a time, they need re-greasing at the end of every shift or every eight hours. If an employee forgets to re-grease the bushing, it can lead to premature failure, and potentially shutdown the entire machine. </p><p>Bronze is softer than steel so its load rating isn't as high as that of a steel bushing. Aluminium bronze bushings are still widely used in construction machines. </p><p>When selecting a bearing, it is important to work with the bearing manufacturer's engineering team as they can spot bearing-related improvements. For example, CCTY Bearing identified a critical design change when reviewing a bushing selection for a bulldozer's shaft. The lengths of the specified bushings were too long relative to the loads on the shafts. This type of load would create excessive stress concentration on the bushing edges. Backed by results from FEA and field tests, the OEM implemented CCTY Bearing's recommendation of a shorter bushing to fully protect the shaft. </p><p> <span style="font-weight: bold;">Spherical plain bearings (SPBs)</span><br />SPBs are key components in hydraulic cylinders as they are designed to take very heavy loads and impact. Hydraulic cylinders give power to the moving accessories on construction equipment, so having a strong and reliable SPB maintains uptime and equipment productivity. </p><p>What makes CCTY Bearing's SPBs unique is the ability to dry-apply molybdenum disulphide to the bearing surface. Some SPB manufacturers apply a wet mixture with oil or grease and smear over the surface area. This type of application is not only dirty, but it also lacks uniformity as grease slides over the part's surfaces. </p><p>The dry film used by CCTY bearing is sprayed on the SPB and then baked. It allows for a clean and easy-to-handle assembly with uniform distribution of the lubricating particles.</p><p>CCTY Bearing also separates the inner and outer ring with a phosphate super-finish (phosphating) on the raceway. When combined with the dry film, the SPB runs smoothly during the break-in stage and thus prolongs the durability life significantly. Phosphating absorbs some of the oil at initial stage of operation and moly-disulphide protects the surface. After the surface is smooth from running, the grease acts as a lubricant. This combination of surface treatment reduces the occurrence of scrape or galling on the SPB. </p><p>Bearings that excel in rugged elements, under heavy loads and aggressive run times are necessary. Choosing a manufacturer that understands construction applications and produces bearings specifically designed for the conditions will enable machinery to work more efficiently and last longer.</p><p> <span style="font-weight: bold;">For forther information contact:</span><br />CCTY Bearing<br />Cell: +91-9823017144 / 9909501963<br />Email: info.in@cctybearing.com<br /></p>