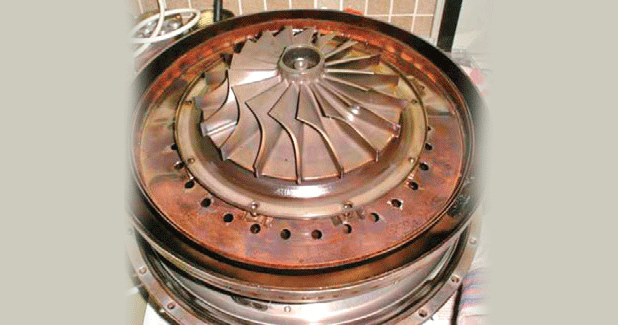
Bearings: Brother in Arms With Manufacturing
Manufacturing and bearings are ?brothers in arms?. Some type of bearing is always required for every conceivable engineered movement, irrespective of the purpose or design. In synch with growth in manufacturing, demand for bearings will grow in leaps and bounds, in terms of variety, applications, technology and volumes. Very few are in a position to accurately estimate the industry size of bearings in the next decade, from the existing Rs 1000 crore. While new bearing majors and others will enter the market, the existing bearing majors and medium size bearing manufacturers will need to substantially ramp up production facilities to increase their product and capacities to meet the market?s demands from OEMs and replacement segments. SKF present in India from a long time has already invested in R&D, resulting in numerous innovations, new standards, products and solutions in bearings. Our CASH Special, tracks the latest developments in bearings, with an emphasis on off-road equipment applications.
Construction equipment operates in highly dusty or wet or other very challenging work environment on one hand while the owners demand the maximum possible availability and utilisation at minimum cost. This is apparently, an impossible situation for the maintenance crew to handle. Reliability Centered Maintenance (RCM), a best practice, can be an answer to meet such a difficult challenge. An intelligently implemented RCM program can deliver these objectives for all critical and high value equipment. The RCM system comprises of: assessment of the specific requirements, maintenance measurements and implementation methodology, leading to ?repair before failure? thereby maximising availability and minimising costs. Further, it provides opportunities to extend the economic life cycle of equipment.