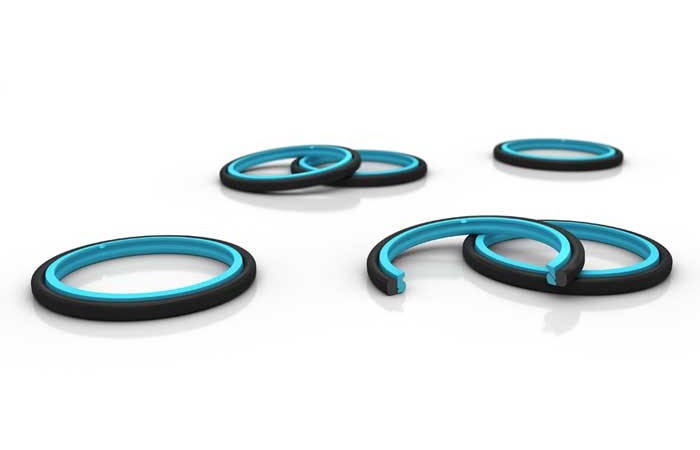
Beating the friction
Keeping systems lubricated
Lubrication is critical to keeping moving parts in machinery operating smoothly and efficiently, achieved by creating a thin film of fluid as separation between the seals and hardware. Without it, damage to seals and hardware is likely, leading to downtime and losses in productivity. Material and design development have for decades largely focused on improving performance and reliability of the primary seal in hydraulic cylinders. And they have been designed to be incredibly dependable and efficient.
Primary seals are the first line of defence against system pressure, while secondary seals act as a residual oil barrier, and scrapers remove fluids and dirt without external forces interfering with their operation. Technology and expertise have resulted in the portfolios of seals for pistons and rods that we see on the market today; both specialised and general products for hydraulic sealing applications.
Modern hydraulic fluids give excellent protection against wear and corrosion; the problem is that as the focus has been on the primary seal sealing lubricant in, sometimes this can prevent lubrication from reaching the contact area of other sealing system elements, stopping the benefits of lubrication on the contact surface. In a wind turbine’s pitch cylinder, for example, short-stroke service and years of 24/7 cycling means that lubrication is often not reaching the elements ‘downstream’ of the primary seal, resulting in wear and damage from dry running.
Fighting dry-running
Trelleborg Sealing Solutions has been hard at work developing proprietary and patented methods for improving performance in applications that have been seeing failures and damage resulting from dry-running. Sealing configurations are based on a new sealing technology termed Lubrication Management.
The primary seal still protects against system pressure, but by carefully modifying seal geometry, small quantities of lubricating media are allowed to enter the contact zones during the outstroke. This significantly reduces friction and further protects the hardware and seals, ensuring adequate fluid can reach all sealing elements and increasing total system lifetime. Usually, to achieve the same lubrication, a drain line would need to be installed behind the primary element, to prevent over-pressure and seal blow out. But engineers at Trelleborg Sealing Solutions decided to rethink classic approaches and combine some of their most effective technologies to develop a wholly new solution.
Turcon® Stepseal® V LM is a new type of primary seal that combines Trelleborg Lubrication Management principles with Stepseal® V design features to offer improved lifetime and performance across the whole sealing system. The Turcon® Stepseal® V range of seals features a unique, patented hydrostatic relief channel. It offers increased pressure balancing during operation, which protects secondary seals regardless of the service conditions, and is part of the secret to its low-friction performance. Combining this feature with Trelleborg’s Lubrication Management principles sets the new Turcon® Stepseal® V LM apart.