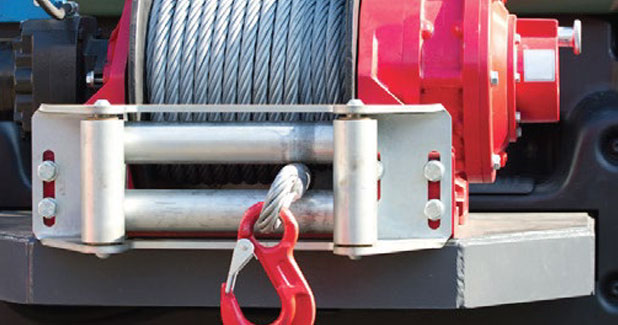
High performance rotary oil seal
<span style="font-weight: bold;">Trelleborg Sealing Solutions unveils HP20 rotary oil seal that optimises performance under pressure.</span><p></p><p> Low-speed/high-torque (LSHT) hydraulic motors are one of the most cost-effective and dependable parts of a hydraulic system. Offering many advantages over a high-speed motor and gearbox speed reducer. LSHT motors give a large amount of power from a comparatively small drive envelope, with low noise and vibration, easy reversal of direction and smooth starting torque. They are commonly found within the forestry, agricultural, construction industries, hydraulic pumps, winch brakes and general purpose hydraulic applications.</p><p>'LSHT motors offer a large amount of power to the user and enable easy reversal of direction with a smooth start,'says <span style="font-weight: bold;">Filippo Zanetti, Product Director for Rotary Oil Seals at Trelleborg Sealing Solutions.</span> 'The metal retainer, for example, doesn't just prevent lip extrusion at the high pressures in the application, but also reaches beyond the seal, making contact with the metal housing to more effectively dissipate heat,'continues Filippo.</p><p>Trelleborg Sealing Solutions Team has developed HP20 seal that provides the optimal solution for sealing the motor output shaft. The geometry of the seal has also been optimised. 'Our product development experts have improved the geometry of the sealing lip by combining with practical testing and theoretical testing methods, such as FEA. We have redesigned the geometry to balance pressure and ensure reliable contact with the sealing lip and the shaft,'says <span style="font-weight: bold;">Maurizio Massetti, Product Engineering Manager.</span> The new features are combined with proprietary materials to deliver even greater performance at high speeds and allow adaptability with differing application conditions and hydraulic fluids, now including bio-degradable oils.</p><p>'Our trust, and our customers' trust, in the solutions we provide is crucial, so we've developed a testing rig specifically for the HP20,'says Maurizio. Equipped with two heads for back-to-back testing of two different solutions, the rig can apply pressures, temperatures and speeds in-line with customer specifications, giving information on product wear and reliability. The rig is capable of being programmed with up to 40 steps, monitoring factors such as the absorbed torque, shaft rotation speed, direction, fluid temperature, flow rate and head pressure, receiving all the data in real-time for analysis. 'By more accurately modelling real-world application conditions, we can give a much better behaviour of product lifetime,'adds Maurizio. For all the hydraulic applications, the HP20 combined with a scraper can deliver increased performance and more cost-effective operation. 'Over two million are already in use by our customers and are seeing the benefits in action,'concludes Zanetti.</p>