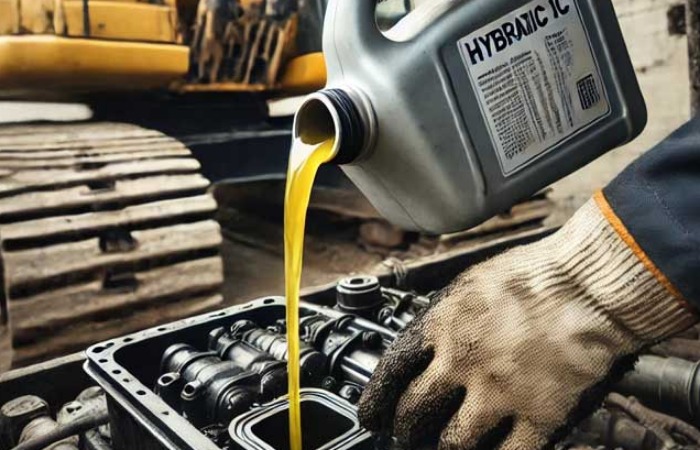
Boosting Performance
Lubricants represent between 1 and 3 per cent of the maintenance budget. However, the impact of improper lubrication on the bottom line can be massive. There are a number of disadvantages of inefficient machine lubricants: short drain intervals or frequent oil changes, unplanned stoppages and downtime, premature part wear, equipment breakdown, and loss of productivity, to name a few. Moreover, all of these points are directly correlated with increased maintenance labour costs. In worse-case scenarios, there are also deadline and contract breaches that can have severe financial and reputational consequences.
Therefore, lubrication is both an essential element of the total cost of ownership and a major part of construction operations.
Using the right lubricant and lubrication system in construction operations is of critical importance. Their formulations are engineered to have high load-carrying capabilities and elevated wear control. Supreme lubricants achieve full fluid film formation and retention. They reduce operating temperatures effectively as a result of their extended thermal and oxidative stability. To be able to withstand extreme construction conditions, they also have to possess high durability and micro pitting resistance.
All of these features and more are parts of complex lubrication systems which contribute to the performance and protection of machines and machine components even after their extensive use and extended service life. A well-lubricated machine is protected from breakdown and with maximal performance and uptime achieved; there is also improved fuel efficiency. Furthermore, other operational benefits include extended repair and drain intervals. While the economic implications of adequate lubrication are reduction in operating and labour costs.
Therefore, proper lubrication does not only mean getting the most out of your machine. Or the longest life for your equipment by protecting critical components from wears and tears. It also means an increase in productivity and operational efficiency and savings.
Wide product range
In the competitive world of construction machinery, maintaining equipment performance and longevity is paramount. One often-overlooked factor in achieving this is the use of OEM-approved lubricants. Several leading OEMs in the construction industry, such as Caterpillar, Komatsu, Volvo CE, and Hitachi, have recognised the benefits of producing their own lubricants. These custom-engineered products offer distinct advantages for both machinery and operators.
OEM-approved lubricants are specifically designed to meet the unique requirements of the machinery they service. For instance, Caterpillar’s lubricants are formulated to match the exact specifications of their engines and components, ensuring that each part operates under ideal conditions. Similarly, Komatsu and Volvo CE develop their own lubricants to cater to the operational needs and environmental conditions of their machinery. This tailored approach helps maximise performance and efficiency, reducing the risk of breakdowns and costly repairs. One of the key benefits of using OEM-approved lubricants is the extended lifespan they can provide to machinery. These lubricants are engineered to offer superior protection against wear, corrosion, and high temperatures, which helps in maintaining the integrity of critical engine and transmission components.
Caterpillar Oils are designed to provide you with increased performance and extended engine life. They are specially formulated to reduce wear on bearings, piston rings, bushings, and other valvetrain components, which can help your engine run longer. Cat Oils improve engine life, performance, and efficiency. The detergents in the formulation are effective at reducing buildup in your engine.
Case IH stays ahead of the curve with newly improved Hy-Tran® Premium Hydraulic Transmission Oil designed to keep tractor transmissions, axles and hydraulic systems free of deposits while inhibiting wear, corrosion, sludge and foaming. Similarly, CNH top-grade Premium Transaxle Oil enables smooth, noise-free operation in equipment, especially those fitted with oil-immersed (wet) brakes like wheel loaders and tractor loader backhoes.
Tata Hitachi offers a wide range of lubricants includes hydraulic oils, engine oils, gear oils, grease and coolants. The company’s engine oils include high quality base oil and advanced additives combined in a balanced manner for high output and low emission diesel engine. Its heavy duty grease is multi-functional extreme pressure grease suitable for temperatures up to 130°C. It is specially recommended for use in construction equipment and heavy duty vehicles.
Says Vasanth Thangavelu, General Manager – Marketing Deployment (Commercial), ExxonMobil Lubricants, “In our product line-up, we have a range of high-performance lubricants designed specifically for the construction and mining sector. These products are tailored to withstand severe conditions such as high temperatures, heavy loads, and harsh environments. One notable product is our Mobil DTE 10 Excel™ Series, hydraulic oil with high viscosity that extends oil change intervals and improves energy efficiency. Another is the Mobil Delvac 1TM ESP 5W-40, a synthetic lubricant offering fuel efficiency and extended engine life. We also have the XHP series, like the Mobilgrease XHP™ 220 Series, focusing on structural stability in harsh operating environments.”
Over the years, Gulf Oil has established partnerships with over 40 OEMs in the automotive, industrial, and construction equipment sectors. These partnerships go beyond product collaboration, extending to various segments such as factory, aftermarket, and operator levels. Gulf Oil’s approach involves working closely with OEMs on product technology, testing, and providing comprehensive services, including education for dealers and operators. The company also emphasises the importance of being at the forefront of technology, working with additive companies and base oils in its state-of-the-art R&D facility in Chennai.
“Gulf Oil has a history of pioneering lubricants with a focus on longevity and quality. Recently, the company introduced products like Gulf Harmony Biosynthetic, a synthetic oil with advanced grades, and a biodegradable hydraulic oil called Harmony. Additionally, Gulf Oil launched Gulf Harmony Premium 46, zinc-free hydraulic oil designed for extreme weather conditions in India. The company also introduced high-performance wire rope grease, emphasising its commitment to optimal lubrication and product durability,” said Ravi Chawla, MD & CEO, Gulf Oil Lubricants.
Shell’s high-performance lubricants are engineered to maximise protection and ensure the optimal performance of construction equipment, even in the most challenging conditions. Utilising advanced technology, these lubricants drive efficiency and help customers maximise the capabilities of their machines.
Says Praveen Nagpal, Chief Technology Officer, Shell Lubricants India, “Shell Tellus S4 VE hydraulic oil, derived from gas-to-liquid technology, reduces energy losses from hydraulic pumps. Additionally, Shell Gadus S3 V460D 2 high-temperature grease enhances efficiency and extends service intervals, resulting in significant cost savings. To ensure smooth operation and maintenance of construction machinery, Shell offers expert technical support and digital lubricant solutions, enabling a proactive approach to maintenance. This comprehensive support reduces the impact of unplanned downtime and maintenance costs, contributing to more reliable and cost-effective site operations.”
Shell Lubricants has been a leader in developing next-generation heavy-duty engine oils globally for years. “We have ensured that our systems are agile and ready to meet regulatory reforms, allowing us to stay ahead of changes and meet new standards effectively. Our products, such as Rimula R5 and the Fleet NX series, are formulated with advanced additive technology to protect exhaust after-treatment systems, reduce harmful emissions, and improve combustion efficiency,” added Nagpal.
“The high-performance lubricants from GS Caltex offer ultimate reliability at all temperatures, lower oil consumption, significantly lower fuel consumption and specifically extended service intervals. Whenever engines and gearboxes run freer and more reliably, operating costs are lower if only because they consume less. We in GS Caltex are always focusing on reducing overall lubrication costs of business and have made services an integral part of our offering to mining companies to achieve sustainable goals,” says Jayanta Ray, General Manager – Industrial and OEM, GS Caltex India.
GS Caltex KIXX LUBO Group II/III base oil has excellent low temperature properties and exceptionally bright water-white clear transparent characteristics. The Group II/III base oil produced by GS Caltex is environment-friendly with low volatility, thus reducing oil consumption and improving fuel economy. Kixx Lubo Base Oils also offer high thermal and oxidation stability to support drain interval extension.
Castrol offers a comprehensive range of high-quality industrial lubricating oils and greases tailored to meet the specific needs of various applications and industries. Castrol’s extensive portfolio includes mineral, synthetic, semi-synthetic, and a wide selection of high-performance greases. With expertise, commitment to quality and continuous innovation, Castrol lubricants can be trusted to provide optimal performance, reliability, and equipment longevity, making them the ideal choice for superior lubrication excellence.
Oilmax Systems, based in Pune, has been providing very unique and innovative products for oil and coolant conservation for more than 25 years. Says Ashutosh P Gokhale, Director, Oilmax Systems, “We are manufacturers and exporters of industrial equipment, including hydraulic oil cleaning systems, vacuum-operated sump cleaners, floating/tramp oil separator, etc. The marine, mining, and automotive industries are just a few that use these items. With our products, there are no filter elements or consumer costs because they operate on centrifugal separations. The smallest of the contaminants is separated from the oil using centrifugal force, extending the life of the oil, filter, and machinery.”
Selecting the right lubricant
Selecting the appropriate lubricant—whether oil or grease—is crucial for maintaining equipment performance and prolonging its life. Each type of lubricant has its own set of advantages and drawbacks, making them better suited for different applications and conditions. Effective lubrication not only minimises friction and prevents wear but also ensures smooth and efficient machinery operation.
Viscosity is a key characteristic of lubricants that impacts their ability to protect heavy machinery. It essentially governs the lubricant’s flow and thickness, akin to its lifeblood. When choosing a lubricant, consider both the type of machinery and the specific operating conditions it encounters. Different machines require different viscosities to function optimally. For instance, high-speed equipment typically performs better with low-viscosity lubricants that reduce friction and improve efficiency, while heavy-duty machinery may need higher viscosity lubricants to support greater loads. Environmental factors, especially in industries like oil and gas, also play a crucial role in determining the right viscosity.
Additionally, compatibility is an essential factor in lubrication. The chosen lubricant must be compatible with your machinery’s existing systems. Incompatible lubricants can cause efficiency issues, increased wear, and costly breakdowns. By opting for our pressure-activated lubricants, you minimise the risk of compatibility problems.
Road ahead
Lubricants play a vital role in the effective operation and longevity of construction equipment. By reducing friction, dissipating heat, preventing corrosion, and providing cleaning and sealing functions, lubricants help ensure that machinery performs optimally and remain reliable in challenging conditions. Understanding the types of lubricants available, adhering to best practices, and addressing common challenges can significantly enhance equipment performance and reduce maintenance costs.
Investing time and resources in proper lubrication practices not only extends the life of your equipment but also contributes to safer and more efficient construction operations. As construction projects continue to grow in complexity and scale, maintaining a proactive approach to lubrication will remain a key factor in achieving success and maximising the value of your investment in machinery.
QUICK BYTES:
Dangers of over lubrication
An insufficient amount of a lubricant can cause serious damage to construction machinery and even bring operations to a stop. One common misconception is that to prevent this, more lubricant should be added.
This, however, is also a serious issue that can cause premature failure in components like bearings for instance due to elevated temperatures and oxidation issues caused by over lubing. In case of an over-greased bearing, its rollers can start sliding instead of turning causing the grease to churn. Consequently, churning removes the base oil from the lubricant or grease leaving behind only the lubricator thickener that typically does not possess many or any lubricating features. The churning of the grease also creates heat and, as there is no base oil present, the lubricant or grease starts to harden.
Once more, machinery operators are faced with the possibility of component damage, additional lubricant changes which translates to higher grease consumption and costs.
Common challenges and solutions
Despite the best efforts, challenges in lubricating construction equipment can arise. Here are some common issues and how to address them: