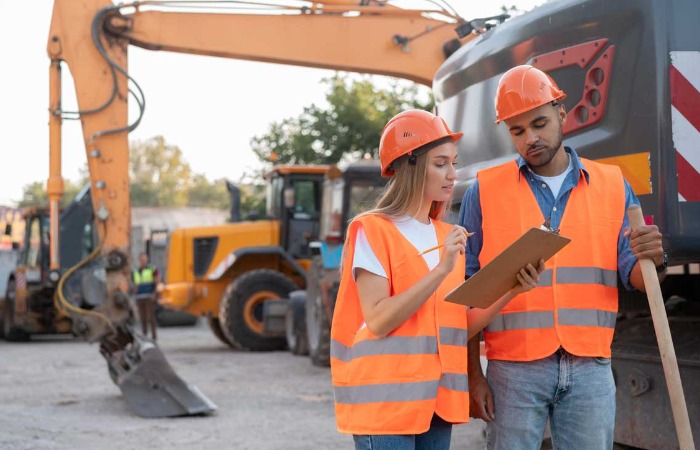
Building Safer Worksites
The operational efficiency and safety of construction and industrial projects across India are significantly dependent on the reliable performance of machinery. A crucial element in ensuring this reliability and preventing accidents is a consistent and well-executed approach to preventive maintenance. The demanding nature of the work undertaken in our sector means equipment is often subjected to heavy use and challenging conditions. Over time, wear and tear are inevitable, but neglecting regular maintenance can lead to equipment failure, which not only causes costly downtime but also poses significant safety risks to personnel on site.
Preventive maintenance is not simply about fixing a problem after it arises; it is a proactive strategy focused on identifying and addressing potential issues before they escalate. This involves regular inspections, scheduled servicing, and the timely replacement of worn or damaged components. By adhering to a well-defined maintenance schedule, we can significantly reduce the likelihood of unexpected breakdowns and the associated hazards in all operational environments. This includes following manufacturer recommendations for maintenance intervals and procedures, as well as keeping detailed records of all maintenance activities.
Consider the various types of machinery used in our industry – from excavators and loaders to cranes and specialised equipment, found in projects across different states. Each of these machines has critical components that require regular attention. For instance, hydraulic systems need to be checked for leaks, engines require regular oil changes and filter replacements, and structural elements must be inspected for any signs of stress or damage. Ignoring these essential maintenance tasks can lead to serious failures, such as brake failure, structural collapse, or engine malfunction, all of which can have severe safety consequences. Regular inspections should also include safety features such as emergency shut-off switches and warning systems.
Implementing a comprehensive preventive maintenance programme offers numerous benefits. Firstly, it significantly improves machine safety by ensuring that equipment is operating within its designed parameters and that potential hazards are identified and rectified before they can cause harm. Secondly, regular maintenance extends the lifespan of the equipment, providing a better return on investment for businesses. Thirdly, it minimises unplanned downtime, leading to improved project schedules and overall productivity. A well-maintained fleet of equipment also presents a more professional image to clients and stakeholders.
The adoption of modern technologies can further optimise preventive maintenance practices. Telematics systems can provide real-time data on machine performance, allowing for predictive maintenance based on actual usage and operating conditions. This data can inform maintenance schedules and alert operators to potential issues before they become critical. Utilising genuine, high-quality parts during maintenance is also crucial to ensure the continued reliability and safety of the equipment.
In essence, viewing preventive maintenance as an integral part of our operational strategy, rather than an optional expense, is paramount. By prioritising the regular care and upkeep of our machinery, we are not only safeguarding our investments but, more importantly, we are actively contributing to a safer working environment for everyone involved in construction and industrial activities. This proactive approach to machine health is a fundamental pillar of responsible project management and a commitment to the well-being of our workforce nationwide. By fostering a culture of regular maintenance and safety checks, we can create a workplace where equipment failures and accidents are significantly reduced.
Article courtesy: CNH Industrial