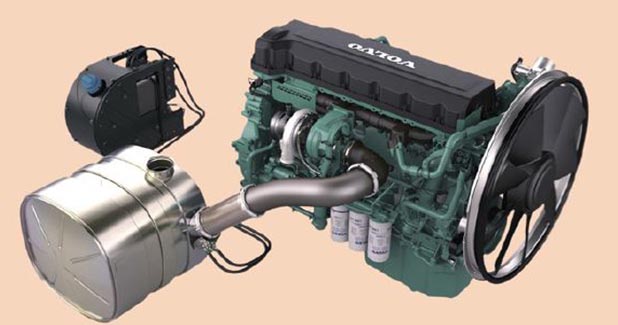
Compliance Challenges
Embracing the next level emission regulations is expected to be tough for the engine and equipment OEMs considering technology upgradations and need for adequate skill development among the users. <p></p><p> With emission regulations entering the next stage in 2020, off-road equipment are gearing up to meet the regulations with new designs and fuel composition. As the BS (CEV) IV is just a year away from implementation, what are the new changes taking place in engines and components? How OEMs are realigning themselves to be ready with their equipment to accept the new norms? How challenging is the situation to adopt the new regulations? How technology is evolving and what are the new opportunities for such technology providers? </p><p> <span style="font-weight: bold;">The transition </span><br />Emission compliance is of utmost importance for equipment players and fuel producers as the norms are getting tougher. Since April 2011, the emission standard applicable to off-highway equipment is Bharat (CEV) Stage III. Emission standards primarily apply to the exhaust emissions from the engine. Diesel, fuel injection systems on diesel engine and diesel engine itself come under the purview of emission.</p><p> In line with the global practice of promoting the use of cleaner diesel engines, Ministry of Road Transport and Highways on March 5, 2018 issued a notification for implementing BS-IV and BS V emission norms for the engines of wheeled construction equipment from October 2020 and April 2024, respectively. The emission standards are similar to Euro Stage IV and Stage V non-road vehicle. The BS CEV- IV standards are applicable to diesel engines between 37 and 560 kW. A lot of changes are going to take place in diesel engines and components. The engine and equipment OEMs are already on the job to meet the stringent requirements of the new regulations. </p><p>According to <span style="font-weight: bold;">Pradeep Sharma, President, Action Construction Equipment, </span>the engines used for complying to BS IV emission norms are generally equipped with common-rail fuel injection system capable of generating high injection pressure and an engine control unit (ECU) for electronically controlled solenoid fuel injectors and exhaust after treatment system.</p><p><span style="font-weight: bold;">Vivek Hajela, General Manager and Head-CEB, Larsen & Toubro, </span>elaborates, "In the new emission regime, the engines will have to adopt advanced technologies like Common Rail Direct Injection (CRDI) for fuel systems, Exhaust Gas Recirculation (EGR) for NOx reduction, and Diesel Oxidation Catalyst (DOC) and Selective Catalytic Reduction (SCR) for Exhaust After-treatment Systems (EATS). For the functioning of the SCR, AdBlue which acts as a reductant, is an additional consumable required. To integrate all the above, engine and EATS consist of several sensors and to manage the performance efficiently, the engine henceforth has to be electronically controlled through an ECU. Errors and malfunctioning of engine and EATS are to be monitored through CAN-based cluster."</p><p>According to <span style="font-weight: bold;">Hemant Mathur, AVP-Sales and Marketing, Tata Hitachi Construction Machinery Co, </span>based on the operating power band, the products need to undergo various levels of after treatment to comply with the emission norms. "During this changeover, Tata Hitachi is also planning to introduce some newer features in the machines that will make them more user-friendly and even safer to work on," he says.</p><p>From an engine manufacturer's perspective, <span style="font-weight: bold;">Miron Thoms, Vice President and Head, Volvo Penta India </span>says,"With the stringent BS (CEV) IV emission regulations, all the engine suppliers have to move to electronic engines with an after-treatment system. Volvo Penta has already in 2006 introduced electronically controlled engines in India, independent of stricter emission regulations."</p><p>He further adds, "OEMs will have no choice but electronic engines and at the same time will look for engines with proven track record in terms of reliability and efficiency. Volvo Penta has been one of the pioneers of electronic engine control and all our engines are already today as a standard electronically controlled. Many features and benefits for end-users and operators are only possible with an electronic engine control. Most important are the increased reliability and stable operations over the lifetime of the engine. Volvo Penta will use its tried and tested Selective Catalytic Reduction (SCR) technology for Indian OEMs when the stringent BS (CEV) IV emission regulations come into effect in October 2020." </p><p>According to Thoms, customers of Volvo Penta are already today prepared for the change as the base engine dimensions remain the same, hence the driveline and engine room does not have to be alternated. "Only the exhaust system has to be redesigned, with an easy switch of the current silencer with the new SCR catalyst and its inbuilt silencer," he adds.</p><p><span style="font-weight: bold;">Sanjeev Nimkar, COO, Kirloskar Oil Engines (KOEL)</span> says, "KOEL believes in developing its products according to the equipment's requirements as finally engine is the "heart" of equipment and plays an extremely critical role in the equipment's performance. So, instead of developing plain vanilla product, we customise our products for various equipment and applications in the market." On a technology level, the major changes that take place while transitioning towards the stringent BS (CEV) IV emission norms is introduction of electronic engines from existing mechanical engine. This will then get coupled with addition of appropriate "after-treatment system", which will change with respect to various power nodes of engine and the end-customer requirement. "End-users" needs and requirements were the central core theme for us to develop our BS-IV products. With this consideration, we have developed our unique product architectures which will surely emerge as winning products in the market. Apart from these changes, the power nodes also will see a major change in multiple applications, depending on the equipment and market requirements," he adds.</p><p> <span style="font-weight: bold;">Role of technology</span><br />India is moving to stringent emission regulations and customers will be using after-treatment system for the very first time. So, the simplest solutions with lesser maintenance will succeed. Thoms says, "Volvo Penta's SCR only technology is providing features and benefits in the complete value chain. We see our after-treatment solution as the key differentiator. All in one, the OEM as well as the end-user, customer, and operator will have minimal changes to the stricter emission regulations. Installation commonality across emission regulations and different power nodes, ease of installation as well as the maintenance-free after-treatment technology from Volvo Penta are main features of our design philosophy. Our SCR catalyst is also the silencer and will simply replace the present silencer."</p><p>Apart from the earlier mentioned technological changes that will play a major role, KOEL has invested significantly in the channel readiness, mainly for digitisation. "This will surely provide an edge to KOEL in serving the end-users when the advanced KOEL electronic engines get launched into the market," says Nimkar. "Off-highway equipment works in extremely rough and rugged environment. So, ability of engine manufactures to support the end-users in these tough environments is critical to their success and KOEL will add strength to the end-customers in this endeavour. Kirloskar engines are always cherished for their ease of operation, robustness, durability and reliability. Our product technology coupled with after-market support will play a crucial role in the BS-IV environment," he adds.</p><p> <span style="font-weight: bold;">Meeting challenges</span><br />In spite of the positive implications of the new emission regulations on environment, there are many challenges for the engine and equipment OEMs to face in terms of cost, technology adoption, and availability of fuel matching the requirement.</p><p>The new added technologies and components in the engine system to meet the upcoming emission regulations are going to increase the input cost which is going to compel the OEMs for an upward revision of product cost. This may be a burden on the customers as initial cost. But in the long term, it is going to benefit the customers in many ways. How OEMs are looking at this scenario? </p><p><span style="font-weight: bold;">Jasmeet Singh, AVP-Corporate Communications and Corporate Relations, JCB India</span> says, "JCB India is committed to carrying out socially and environmentally responsible operations across the country. Sustainability is at the core of our business. We are in full support of the upcoming fuel emission norms and are well-prepared to welcome this change, which will lead to better technology and sustainability in the long run."</p><p>He further adds, "We believe the new standards will enable the percolation of world-class technology and advancement in the products/component thus, getting us at par with other advanced markets such as USA and Europe. It will also contribute in the enhancement of the overall value chain of the product in terms of development, research and upgraded technology in the supply chain."</p><p>To ensure seamless transition from BS (CEV) III to BS (CEV) 1V emission standards for wheeled construction equipment, JCB is investing in technology, service support network, skilling and training of its people, according to Singh.</p><p>"India is going to leapfrog from the current BS III emissions to the BS IV emissions which are equivalent to global Tier 4F/Euro Stage IV norms. This is quite different from developed markets which moved to an interim norm such as Tier 4i or Euro Stage III B before progressing to Tier 4F norms. The key challenge lies in developing technology in such a manner that it creates benefits to the end-users and not make their life difficult," says Nimkar.</p><p>According to Thoms, the major challenge is the technology itself to meet these regulations. He adds, "Volvo Penta has already proven success in BS (CEV) IV equivalent Stage IV/Tier 4f technology and is underlined by the increased number of customers in various applications. Hence, the first challenge of product and technology is already addressed by us. Next challenge lies with Indian OEMs who are in the early stages of the learning curve with electronic engines and handling after-treatment system. They need to develop the competence on this aspect. Finally the big challenge lies with end customer handling/maintaining these machines in field. </p><p>Volvo Penta has proactively taken a few steps initiating BS (CEV) IV training for our dealer service partners and our key OEMs in early 2019. Next step, we have already planned training OEMs field personnel as well as OEMs trainings. Further, we support our customers and potential customers with our in-house trained application engineers that support them through the engineering project to develop their new BS CEV IV machine/application."</p><p>Sharma sees these challenges as opportunities as he adds, "We are completely geared up to meet these requirements. This will certainly have an impact in terms of better emission controls further enabling us in offering more environment-friendly equipment to the customers. However, the equipment cost will increase by 5-10 per cent depending upon models." </p><p>He explains further on other factors that are challenging for OEMs. For engines up to 75 hp, the exhaust after treatment system consists of a diesel oxidation catalyst that suffices the BS IV emission norms which doesn't require any major changes in equipment besides changes in electrical harness etc. However, for engines above 75 hp, the after treatment system consists of a selective catalyst reduction, and Blue Tank in addition to DOC. The incorporation of these aggregates on the equipment is a huge challenge because of the sizes of these aggregates and special requirement in terms of their positioning in relation to the engine. The major components affected shall be rear chassis, counterweights, bonnet and dashboard electrical. Compared to equipment fitted with BS III compliant engines, major changes in the electrical harness/aggregates are also envisaged in the equipment meeting BS IV norms.</p><p>Hajela elaborates, "BS (CEV) IV engines will have to be adapted in the machines and thoroughly validated under various operating conditions. OEMs will have to test the machines over a long period of time to prove reliability of the components. For proper functioning of the BS (CEV) IV compliant engine, diesel with maximum 10 ppm sulphur is a necessity. Although this diesel will be available after April 1, 2020 because of implementation of BS-VI emission norms in automobiles, its availability for testing and proving of CEVs prior to April 2020 will be a challenge." </p><p>On the other challenges, Hajela explains, "As we are aware, CEVs are mainly operating in remote areas like mines and quarries and OEMs have to ensure that low sulphur diesel is made available in those remote areas. The CEV manufacturers are facing a major challenge in accommodating the new EATS in their current layout. Proactive selection of right technology and layout planning will ensure smooth transition for future upgradation to BS (CEV) V from April 1, 2024. Since the above system is entirely new and complex, CEV manufacturers will face initial challenges in creating the awareness of proper maintenance practices to the customer. The technicians have to be adequately trained to handle the service and maintenance as the new technology is completely based on sensor controls, the malfunctioning of even one of them would lead to machine breakdown. </p><p>The Adblue, which is an additional consumable for the engines with =75 hp, the operating cost would marginally increase and the failure to use Adblue will lead to breakdown of the equipment. Due to changes in the engine technology, initial cost and maintenance cost of the equipment will significantly increase."</p><p>Mathur elaborates on how his company is gearing up on meeting the new regulations, "In view of the implementation of the BS (CEV) IV norms on wheeled equipment from October 1, 2019, Tata Hitachi has geared up for a timely switch over of its products. All its wheeled products including backhoe loaders and front-end loaders are being upgraded with BS-IV compliant engines. Each of these products is going through the company's rigorous new product introduction (NPI) process that involves thorough analysis of design concepts by different functions, building of proto machines and testing them elaborately in the company's in-house test facilities. The entire process is supported by Hitachi, who already has wide experience of manufacturing Euro-IV (like BS-IV) construction machines for the global market." </p><p>According to him, while the new norms will help a great deal in bringing down pollution levels, it will invariably result in increased equipment costs due to the improved technology and higher fuel prices. ''The increased level of technology will also call for improved maintenance practices, and upskilling of the customer workforce," he adds.</p><p> <span style="font-weight: bold;">Are we ready?</span><br />As the new emission regulations are going to be in force from October 2020, how OEMs and engine manufactures are preparing themselves? ACE is already on the job for introducing the products compliant to the upcoming regulations as Sharma says, "The prototype development of some of the crane models is already in process though the engine suppliers are yet to freeze the design and scope of exhaust after treatment system. The internal testing and field trials are targeted to be finished by May-June 2020 so as to meet the deadline of offering BS IV compliant equipment from October 2020."</p><p>Singh adds, "JCB India is committed to carrying out socially and environmentally responsible operations across the country. Sustainability is at the core of our business. We are in full support of the upcoming fuel emission norms and are well-prepared to welcome this change, which will lead to better technology and sustainability in the long run. We believe the new standards will enable the percolation of world-class technology and advancement in the products and component thus, getting us at par with other advanced markets such as USA and Europe. It will also contribute in the enhancement of the overall value chain of the product in terms of development, research and upgraded technology in the supply chain."</p><p>To ensure seamless transition from BS (CEV) III to BS (CEV) IV emission standards for wheeled construction equipment, JCB is investing in technology, service support network, skilling and training of its people.</p><p>Hajela is of the view, ôManufacturing of BS (CEV) IV compliant machines will be commenced from October, 2020. Hence, we expect various OEMs will approach testing agencies like ARAI simultaneously to get BS IV certification, which will become a challenge. However, as per the provision in the Gazette notification, we will have a six months period to liquidate the stock of existing BS (CEV) III compliant machines."</p><p>Mathur says, "The wheeled machines of Tata Hitachi complying with the new emission norms will hit the market in October 2020. In addition to the wheeled machines, the company is also proactively working on developing new tracked excavators equipped with BS IV compliant engines."</p><p>According to Thoms, Volvo Penta is already in the space of advanced emission compliant products. He adds, "We have been supplying BS (CEV) IV equivalent Stage IV/Tier 4 Final engines globally since 2013. In India, from the middle of 2019 we are working together with several current customer and new OEMs on the BS (CEV) IV introduction."</p><p>Nimkar says, "At KOEL, we are happy to see that the government is taking big environment-friendly steps. KOEL is fully geared up for its BS-IV product development. We have a complete range of KOEL engines, which covers a vast range of several construction equipment applications such as backhoe loaders, compactors, wheel loaders, motor graders, self-loading concrete mixers, cranes along with multiple other applications, which are going for the stringent BS-IV emissions in October 2020 (wheeled applications). Apart from that, we are also gearing up with KOEL BS-IV products on the "tracked applications" such as excavators which are going for the emissions in phase II. KOEL as an independent engine manufacturer is in partnership with the leading global and Indian construction equipment manufacturers for a long period and will continue to foster the partnership in future as the industry moves to new emission norms."</p><p> <span style="font-weight: bold;">Looking ahead</span><br />According to Hajela, despite these challenges, there are several advantages like accurate monitoring of the loads on the engine, thereby resulting in the possibility of optimisation of engine power and fuel consumption. "The availability of the ECU also helps in faster diagnosis and trouble shooting. Remote monitoring of the vehicle becomes more efficient as many of the key parameters are digitally available." Beyond October 2020, the industry is going to be greener and cleaner, once the BS (CEV) IV norms are implemented. We have seen that the industry has to go through a lot of challenges on various fronts. But the implementation of new technologies and processes will make the whole system more sustainable and advanced and on a positive note, this will lead to cleaner and greener future, which is of utmost importance in the era of global warming and climate change. </p><p> <span style="font-weight: bold;">Sudheer Vathiyath</span></p>