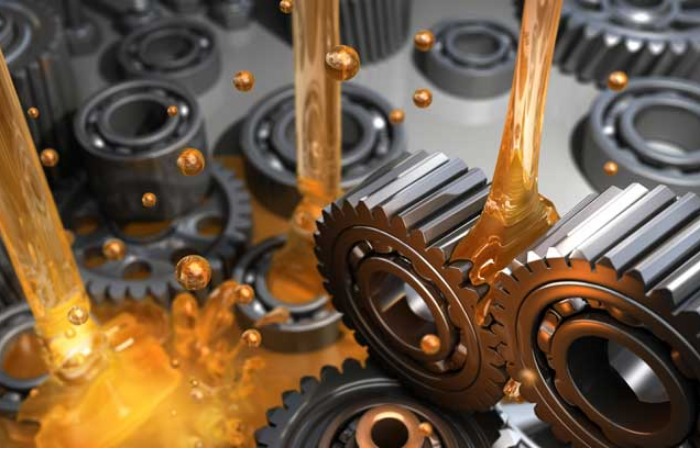
Contamination-free lubricants!
Contamination in lubricating oil is the main reason why 80 per cent of the machinery encounters premature failure. The mechanical failures which take place in the machinery are predominantly due to contamination which is well known to lead to loss of production and revenue.
One of the major pillars of Total Lubrication Management (TLM) is contamination-free lubrication of the machines. Managing and control of contamination in various stages of plant lubrication helps in extending the life of lubricants and equipment. Major emphasis should be given to keeping the lubricants clean, cool, and dry which helps the machinery to run reliably and efficiently.
The contaminants are of two types:
- Internal - for example combustion products, wear and tear of components, sludge, varnish, etc. There are controlled through periodic online and offline filtration techniques
- External - For example dust, dirt and water through storage, handling, and dispensing of lubricant
The following areas are important to control external contaminants:
- Receipt of new lubricants
- Storage environmental conditions
- Housekeeping standards
- Storage and handling of lubricants
- Dispensing of lubricants using dedicated colour-coded containers
- Maintenance of breathers on the machinery
Receipt of new lubricants
New lubricants are generally received in the stores in bulk and packed form. While receiving the lubricants in bulk care should be taken so that it is filtered before transferring the same to the storage tank. While packed lubricants are generally expected to be contaminated free but some storage and handling processes may cause ingress of dust and water in them. These should be filtered before transferring the contents to the lubricant dispensing tanks or containers.
Environmental conditions on storage
These conditions influence the storage practices of new lubricants. For dusty or wet conditions indoor storage is recommended with barrel bungs tightened and stored horizontally in three to nine positions. In very hot areas for outdoor storage in a shaded or covered area is recommended and for indoor storage well- ventilated areas rooms are recommended. Lubricating oils in machines are like blood in the human body, hence it is highly recommended to store lubricants (oil/grease) indoors.
Housekeeping standards
Good housekeeping practices would ensure dust particles are not adhering on any lube or grease barrel, full or empty, at the storage or dispensing location and lubrication tools used for dispensing. Spillage and leakage handling are important areas of good housekeeping standards.
Apart from the environmental reasons for storage, good Storage and Handling practices for lubricants are important to control contaminants. While receiving the lubricants care should be taken that the packaging should not be broken exposing the lubricants to dusty conditions. The longer the lubricant is stored the higher the chances of contamination and degradation hence they should be stored in such a way as to facilitate the rotating of inventory on a first-in first-out basis. To prevent mixing up proper labelling and colour coding is useful.
Dispensing of lubricants and equipment
As per the study, available 60 per cent of contamination of lubricants happens due to wrong dispensing and handling. The dispensing equipment should be thoroughly cleaned and flushed between uses otherwise dirt, dust, old oil residue, and other contaminants may contaminate the new oil before it even reached the machinery. The use of Dust Free Container is highly recommended for the clean and safe transfer of lubricant to the machinery. This GLOBETECH V generation dust-free containers have been designed for convenient, easy, safe oil top-up with the elimination of contamination.
Desiccant breathers on the machinery
Choosing the right desiccant breather is important for contamination control in the reservoir. The factors influencing the type of breather are environment, application, airflow rate, reservoir capacity and the type of operation. The major factor influencing the life is humidity of the air. Most desiccant breathers last anywhere between three to six months. These should be checked at regular intervals.
Grease: Handling & dispensing
The grease barrels are to be stored in the vertical position with a plastic cover on the top. While dispensing grease specific spatulas and grease guns should be used. Cotton waste should not be used for cleaning excess grease from the dispensers, etc.