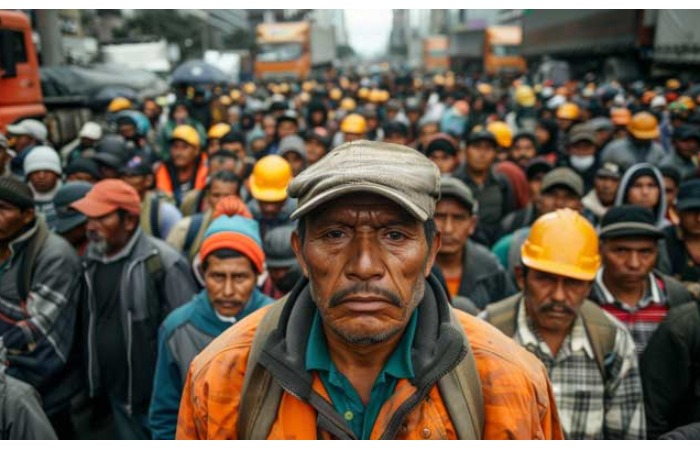
Empowering India’s Manufacturing Workforce
The manufacturing sector is undergoing a huge transformation, driven by advancements in automation, artificial intelligence (AI), and Industry 4.0. While these technologies enhance efficiency and innovation, they also expose a critical challenge—the widening skills gap.
India, on the brink of becoming a global manufacturing powerhouse, faces a pressing shortage of adequately trained professionals to meet the demands of evolving technologies. This gap threatens not only the industry's growth but also the country’s economic progress and global competitiveness.
With the rapid pace of automation and digital transformation, manufacturers must adapt swiftly to stay ahead. As experienced workers retire and job roles evolve, the demand for a highly skilled workforce grows. Bridging this skills gap is essential to building a resilient, future-ready manufacturing ecosystem.
Challenge of skilling in manufacturing
Traditionally, manufacturing has relied on workers skilled in hands-on, technical tasks. But modern factories demand expertise in robotics, data analysis, machine learning, and design technology—skills that many current workers simply don’t possess. The result? Manufacturers often find themselves unable to fill jobs that require a mix of traditional technical skills and new-age technological proficiency.
To close this skills gap, manufacturers need a strategy that revolves around training and upskilling workers, ensuring that they are active participants in shaping their company’s future. By doing so, we can build a workforce that is not only resilient to change but ready to thrive in an increasingly automated world.
What’s driving the skills gap?
- Technological advancements: The growing integration of automation, AI, and IoT means that manufacturers need a workforce proficient in these technologies. But many workers still lack the necessary skills.
- Educational mismatch: The gap between educational curricula and industry needs is widening. Traditional training often leaves workers with theoretical knowledge, but without the practical skills demanded by modern manufacturing. This mismatch is compounded by a 15 per cent skills gap, where workers’ technical expertise doesn’t align with the rapid adoption of new technologies like automation and digital tools.
- Perception issues: Manufacturing jobs are often viewed as physically demanding and low on career growth, which discourages younger generations from pursuing this field. Regional disparities: Training facilities are not evenly distributed across the country, leaving some regions underprepared to meet the demand for skilled workers.
A study by the National Skill Development Corporation (NSDC) highlights a significant mismatch between the demand and supply of skilled workers in India. The report estimates a demand of 103 million skilled workers, while the current supply is only 74 million, revealing a critical shortfall. This gap emphasises the urgent need for targeted skilling and training initiatives across various sectors with specific focus on manufacturing sector to bridge the workforce deficit.
Strategies to bridge the skills gap
Bridging this skills gap requires a joint effort from all stakeholders—governments, educational institutions, and the private sector. By prioritising skill development, embracing modern training methods, and shifting perceptions, we can create a workforce ready for the challenges ahead.
- Revamping education for industry needs: Educational institutions need to align their curricula with the needs of modern manufacturing. Courses in automation, AI, robotics, and data analytics should become the norm. Collaborations between schools and manufacturers can give students real-world experience through internships and apprenticeships, ensuring they graduate with the skills companies need.
- Investing in reskilling and upskilling: Manufacturers should invest in internal training programs to help employees acquire new skills. Collaborations with online platforms can also provide workers with digital literacy, robotics, data analysis, and industrial programming skills. These training initiatives must be accessible and affordable, empowering workers to grow along with their industries.
- Leveraging technology in training: Virtual reality (VR) and augmented reality (AR) can provide employees with realistic, hands-on experiences in a risk-free environment. AI-powered learning platforms could personalise the training process, adapting to each worker’s pace and skill level, making it easier for them to master complex tasks.
- Changing the narrative around manufacturing jobs: The perception of manufacturing jobs as low-tech, labour-intensive work needs to change. Manufacturers should emphasise the high-tech, innovative nature of modern manufacturing, showcasing it as a rewarding career path. Outreach programs, school visits, and partnerships with STEM education initiatives can help spark interest among younger generations.
- Promoting continuous learning: As technology evolves, workers must continuously adapt. Companies should encourage a culture of lifelong learning by offering flexible training options, tuition reimbursement, and clear career advancement pathways.
Empowering women in India’s manufacturing sector
Increasing gender diversity while addressing the skills gap is crucial for the growth of India’s manufacturing sector. Recent data from a leading business services provider indicates that women now comprise 20 per cent of the manufacturing workforce, with an impressive 80 per cent representation in electronics. Additionally, reports from a multinational HR consulting firm highlight a threefold increase in the demand for female apprentices across key sectors such as automotive, electric vehicles (EV), and electronics, signalling a transformation in hiring practices. Cities like Bengaluru, Chennai, Hyderabad, Pune, and Mumbai are emerging as major hubs for hiring women in manufacturing.
This positive shift in gender diversity is opening doors for women in roles traditionally dominated by men. By prioritising skill development and inclusion, India has the opportunity to unlock the full potential of its manufacturing sector—enhancing productivity, fostering innovation, and strengthening its global competitiveness.
As automation, sustainable practices, and smart factories take centre stage, India’s manufacturing sector is poised to create millions of job opportunities while setting its role in global supply chains. With strategic investments in upskilling and workforce development, India can lead the way in advanced manufacturing, fuelling economic growth and positioning itself as a global manufacturing powerhouse for the future.
ABOUT THE AUTHOR:
The article is authored by Subash Ramdoss, Head – ME and Machine Building Division (MBD), Elgi Equipments.