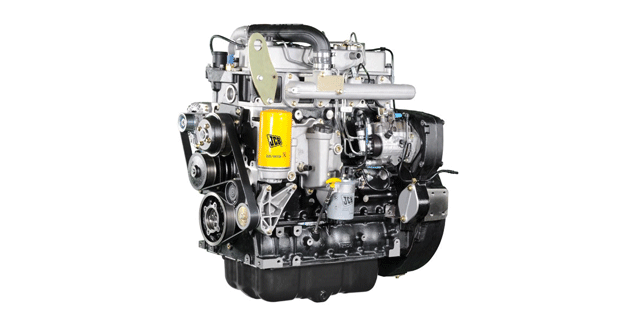
Engines of Future
Introduction of Tier-IV compliant engines is around the corner, for infrastructure equipment. According to Indian Diesel Engine Manufacturers Association (IDEMA), most Indian engine manufacturers have already geared to deliver the same.
Future of Indian emission norms
Vinayak Chavan, General Manager, Deutz Engines (India), says, ?Deutz is already supplying Tier-IV-Final engines globally, while Tier III engines are being supplied to non-emission compliant countries. As far as Indian market is concerned, we supply BS-III compliant (which is equivalent to Tier-III norms) engines presently.? Cooper Corporation anticipates a huge demand for Tier-III and IV generation engines from sectors like industrial applications and construction equipment. Farrokh Cooper, Chairman & Managing Director, Cooper Corporation, says, ?Currently the emission norms are getting formulated and effective date will depend up on availability of maximum 10 ppm. Sulphur content in fuel. At Cooper we have always endorsed the government?s view of bringing in stringent emission norms and similarly in case of Tier-III and IV engines we will be adhering to the norms as required.?
JCB manufactures engines for India that are BS-III compliant for construction equipment, while for the industrial applications, it has gensets compliant to CPCB2 norms. ?At JCB, we believe giving our customers the latest technology and will comply to the latest emission norms as and when they are announced,? says Amit Gossain, Executive Vice President - Sales, Marketing and Business Development, JCB India.
According to Sanjeev Nimkar, Vice President and Business Head, Power, Industrial and Service, Kirloskar Oil Engines (KOEL), currently the Tier-III compliant equipments are there in the wheeled and mobile off-highway segment. The tracked ones are still in the Tier-I or II level of emission norms. He adds, ?There are clear-cut guidelines and indications coming up for Tier-IV. Discussions are going on in the industry whether the government should go first with Tier-IV Interim, a lower version of Final Tier-IV, and then with Tier-IV Final.?
JCB India offers engines in mobile and stationary segments: In mobile at capacity range 56 kW to 129 kW (all in IV cylinder ratings), while in stationary, the range is 56 kW to 121 kW (all in IV-cylinder ratings). Further, it also has 6-cylinder engines which also cater to the requirement for mobile applications in the power range up to 212 kW and for stationary engines up to 200 kVA.
KOEL has diesel engines on offer ranging from 3 to 300 hp for off-highway applications; for gensets the range is greater than 5,000 hp.
Vijay Varma, Chairman, IDEMA, says, ?The government has concluded on what the next emission norms should be. Now it has to issue an order through gazette notification and then it will come into effect. We expect the new norms come into effect in the next two years time. But it depends on the government on how soon it will complete its activity and issue the official notification.?
When the norms are getting stringent, it is becoming challenging for the companies to comply with in the current scenario. According to Chavan, emission standards are becoming more and more stringent as time passes. ?However, it is equally important that the consumables such as fuel, lubricating oils etc, of appropriate standards and quality are also to be made available easily across the country,? he observes. JCB always updates its product range as Gossain says, ?Our endeavour is to constantly improve the engines on various aspects of performance and fuel efficiency with every new revision of engine.?
Nimkar optimistically says, ?When we move to Tier-IV norms, we will also be complying with the European standards at the same go. So our off-highway equipment will be adhering to European standards as well. This will also make us eligible to enter global markets, and vice versa.
Focus on fuel efficiency
According to Chavan, presently most of engine manufacturers use Common Rail Direct injection (CRDi) technology with electronic governing to achieve optimum fuel efficiency. ?Completely electronically controlled fuel injection systems (electronic fuel injection pumps + electronic injectors) are also developed to achieve maximum fuel efficiency,? he adds.
For Cooper, enhancing fuel efficiency has always been the top priority. For the same, according to Cooper, the new generation engines will be equipped with technology features such as optimising the combustion properties, using low friction materials for power cylinder components, enhancing the fuel pressures and using exhaust gas recirculation (EGR).
?Going forward, fuel efficiency will be a vital element in our country,? says Nimkar. He elaborates on KOEL?s efforts in achieving better fuel efficiency in its products, ?Incidentally, we have taken a new tag line for us called Efficiency Integrated. The single most important factor in consideration is fuel efficiency. When the product design starts, we keep fuel efficiency at the center of our designing and revolve our all other aspects around that.?
Advanced design trends
Major factors that impact fuel efficiency of an engine are fuel delivery system, fuel injection pressure, hydraulics and electronics in injection systems, changes in exhaust temperature, ignition chamber design, and compression ratio.
Fuel delivery system: Earlier fuel delivery was mechanically controlled. Nowadays according to S Jayabalan, Senior General Manager, Application Engineering, Stanadyne Amalgamation, ?the fuel injection system talks about injecting a measured amount of fuel, in a period of time, at a given instance of engine position. How accurately you can go ahead and repeat and how flexible you are in doing that determines your ability to meet higher emissions and also improve your fuel efficiency.? Stanadyne has introduced EcoForce, a new high-technology fuel injection system to reduce emission for up to 50 hp engines.
Nimkar says, ?At Tier-III level, we are able to manage fuel efficiencies with electromechanical fuel delivery system. Going into Tier-IV level, the requirement will be for 100 per cent electronic system; electronic control, EGR - internal or external. Then the entire fuel delivery system will shift to CRDi, in off-highway sector. However, good fuel quality will be of essence.
Fuel injection pressure: This tends to go higher and higher in the new emission standards. According to Chavan, earlier injection pressure of fuel injection system was below 1,000 bar. Now it is 1400-1,600 bar for Tier III engines and it will be around 2,000 bar to achieve low NOx level in Tier-IV final compliant engines.
Electronics with hydraulics: Electronics plays a vital role in modern fuel injection systems. ?It helps in speed-governing, precise fuel deliveries and accurate injection timing to achieve optimised results,? says Chavan. Cooper reinforces,?Combustion elements have to be optimised to achieve energy efficiency and electronics will play a major role in doing so.?
Sanjay Chadda, Managing Director, India & Near East, Stanadyne Amalgamation, has a different view on electronic parts in engine. He says, ?Our new pump is based on advanced hydraulics. This pump is mechanical and the reason we feel there is a demand because you can get better fuel efficiency by the electronic pump or the common rail pump. But they come at 2-2.5 times more price. We are bringing the same level of performance of electronic pumps by the mechanical pump with less than 40 per cent of the price. Also, the maintenance of electronic pump is expensive compared to the mechanical pump.?
Exhaust temperature: According to Chavan, it is a real challenge in engine design to control the exhaust temperature. It directly affects the emission levels. So it is equally important to maintain the desired level of exhaust temperature during the engine operation. Nimkar says, ?In the new domain of Tier-IV emissions, a lot of external emission handling systems is needed to put with the engine. Currently we are able to manage the entire emission norms as per Tier-III emission standards inside the engine chamber. But, in Tier-IV, we need to handle a lot of things outside the engine chamber. This is a big change.?
Cooper says, ?There may not be a change in exhaust temperatures, but we have plans of utilising exhaust gas energy through Combined Heat & Power (CHP) concept.?
Ignition chamber design: This helps to form homogenous mixture of air and fuel before the combustion. According to Cooper, combustion chamber design needs changes to meet latest emission norms. ?Compression ratio and piston bowl design, swirl ratios and injection timing also will be optimised,? he observes.
Engine governing system
Variable speed needs governing at various engine speeds to maintain the required load at a given speed where as fixed speed is at one constant engine speed. Normally fixed speed engines are used for stationary applications whereas variable speed engines are used for industrial applications. Nimkar says, ?I don?t think there is much of a difference on the equipment side. But there are requirements coming from some of our OEMs that they need this variable speed engine governing systems so that the operators will be comfortable with changing fuel depending upon the load conditions. We will be offering some solution in this domain and it will be the first time for us. It is more from the perspective of giving comfort to the fleet handlers, machine operators and the same engine will be able to work in various load conditions.?
Power-to-weight ratio
This is a very important aspect of engines. Every equipment manufacturer expect the power-to-weight ratio should be as high as possible. Says Nimkar, ?In this modern era, people expect lower weight machine to do a bigger work. But there are certain cooling packages also attached with this. The most robust is air-cooling types. There are many air-cooled engines which are very robust, but the efficiency of these engines is very low. The more you go with sophisticated engines, the power to weight ratio improves, but their maintenance requirement also will go up. They have to be delicately maintained, though their fuel efficiency is better.? According to Gossain, this is not relevant to the segment of the application as the construction segment which focuses more on highly loaded/torque applications and the engine requirement is more on robustness, ruggedness wherein the power to weight ratio is not the main criteria.
Dr John Pinson, President & CTO, Stanadyne LLC, correlates power-to-weight ratio with cost. ?Power-to-weight ratio is a matter, but with cost. Light weight and high power density lead to cost. We find our customers in this area relatively prefer lower power density. The heavier larger engines tend to be much more durable as well. So certainly from a cost point of view, you could consider producing very high power density engines but in these markets we see lower power density larger engines more durable and have high expectations for long life,? he says.
Cost of technology
The engine industry indicates that technology up gradation will lead to higher cost. Most indicate the price hike in the range of 10 to 50 per cent, depending on the systems incorporated in the engines. However, many endeavour to avoid the same to make their products price competitive.
Optimistic outlook
India is set to be one of the biggest manufacturing hubs in the world. Provider of globally accepted engineering and environment compliant products will fast become its identity. Internal consumption of equipment will grow commensurate to the government?s initiatives towards infrastructure development in the country. Varma says, ?There is a great degree of optimism and we expect that in the coming years, which will be realised in terms of actual projects getting executed and equipment purchased by the contractors, for the same. On this thought, we are pretty optimistic on the future of the industry.?
External success factors
- Govt. to legislate new regulations
- Ready availability of low sulphur fuel, a must
- AdBlue urea supply necessary
- Skill to support new technology in after market