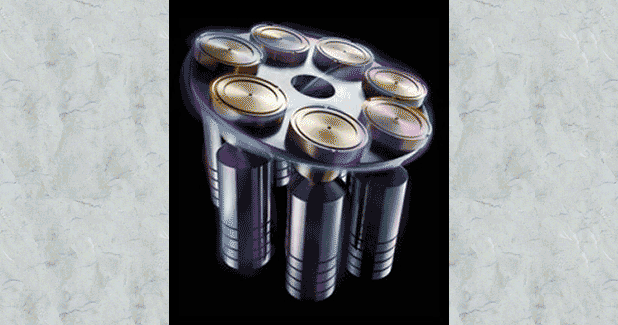
Improving Efficiency
Hydraulic fluids with reduced environmental impact can provide sustainable solutions that support both environmental and economic goals.
Fluids that are used in industrial and mobile equipment applications operate in a wide range of environments and temperatures. It is not difficult to find a lubricant to meet these requirements, but there can be performance concerns if the fluid is not properly formulated. Fluids with a wide operating temperature range are often formulated with special viscosity improver additives to improve both high and low temperature viscometrics; and these additives are subject to shearing forces that can reduce their effectiveness in service.
Advanced hydraulic fluids are available to meet the demands of these systems, as well as to contribute to overall hydraulic system and energy efficiency. These hydraulic fluids transmit pressure and energy, seal close-clearance parts against leakage, minimise wear and frictions, remove heat, flush away dirt and wear particles and protect surfaces against rusting. Other than these functions, the correct hydraulic fluids for the correct machine also have the capability to advance productivity, reduce energy consumption and thus help in monetary savings. This case study on Samruddhi Industries Ltd, one of the leaders in manufacturing unbreakable plastics in India, exemplifies how ExxonMobil supported the company to document energy savings, leading to ?Advancing Productivity?.
In 2000, Samruddhi Industries set up its manufacturing plant at Sangli, in Maharashtra. Currently they have three units in Sangli which house 26 injection moulding machines. Most of these machines were ?in-service? with existing hydraulic oil. Samruddhi Industries were keen on documenting energy efficiency savings and supporting the cause of sustainability.
ExxonMobil recommended using Mobil DTE 10 Excel 68 in their Windsor Armour 150 injection moulding machine. The product has significantly ?lower traction coefficient? than traditional zinc (ZnDDP)-based hydraulic fluids. Over 40 per cent reduction in this property resulted in ?increased efficiency? directly relating to improved equipment productivity.
On observations over a month, Samruddhi Industries recorded reduction in cost of unit production. Mobil DTE 10 Excel 68 displayed an energy efficiency of 4.28 per cent; resulting in an overall savings of Rs 179,400 for all 26 machines annually.
Key benefits of using Mobil DTE 10 Excel 68 included:
- Reduction in energy consumption
- Outstanding shear stability facilitated wider operating temperature range
- Ultra clean performance and oxidative and thermal stability resulting in longer oil drain and filter change interval
Progressive condition monitoring through ExxonMobil? SIGNUM used oil analysis program, to monitor the durability of both equipment and lubricant, was recommended to achieve these benefits.
Mobil DTE 10 Excel series provides ?ultraclean? performance which helps in keeping systems free of deposits for up to three times longer than competitive hydraulic fluids. This is due to Mobil DTE 10 Excel Series hydraulic oil?s ?advanced additive technology?. In Mobil?s proprietary laboratory test, Mobil DTE 10 Excel series has shown improved thermal stability. Better oxidative and thermal stability means the oil holds up better to higher temperatures which lead to longer oil life and reduces sludge type deposits or varnishes. Again, better thermal stability properties provide longer oil life and fewer sticking servo valves.
The results of this demonstration clearly show the impact of increasing hydraulic efficiency. Use of efficient hydraulic fluids in plastic injection molding machines can be expected to reduce energy consumption and increase cycle time, leading to ?Advancing Productivity?.
Article courtesy: ExxonMobil