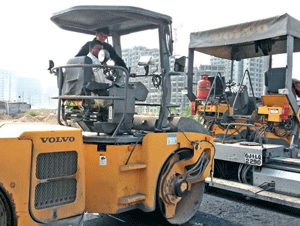
Intelligent Compaction
Intelligent compaction (IC) is a state-of-the-art technology, which is a combination of the absolute measurement technology with regulation system that uses measured information to adapt the equipment continuously to required conditions. IC technology uses a combination of equipment to measure the compaction carried out and to monitor the heat of the asphalt mat. Most of these latest systems minutely document the work carried out, showing the operator/contractor what compaction has been done and providing a digital record that can be stored and checked if required. Using these systems, an operator can optimise the output; moreover, it helps the operator know which area of the asphalt mat has to be compacted before it cools. Most of these latest systems document the work carried out shows the operator/contractor what compaction has been done and provides a digital record that can be stored and checked if required. According to Girish Dixit, General Manager Engineering & Design, Wirtgen India, IC technology will help improve the quality of the roads and improve the efficiency of the operator. He says, ?With IC systems, the quality is not dependent on the operator skills but is system driven and consistently achievable. These systems are user friendly and need to train the correct usage of the system to operators. It is required to create the awareness to equipment owners on the advantages of the system and how the system will help to improve productivity and reduce the operating cost.?
As per the Ministry of Road Transport and Highways (MoRTH) specification, we have to achieve a maximum dry density (MDD) of 95-97 per cent; for embankment it is 95 per cent and earthwork is 97 per cent. As a user, one will be looking at how much passes are required to achieve the density. Along with that, major parameters to be looked into for selecting a compactor are soil type and design requirements. While selecting a particular brand of soil compactor, major parameters looked for are static liner load, nominal amplitude and vibration frequency as these parameters effects the compaction activity the most. Other attributes we look for are the operations and maintenance cost, and fuel efficiency. It is here compactors and rollers with IC technology scores.
Blesson Varghese, Managing Director, Marini India, says, ?As quality results are strictly controlled by authorities (mostly combined with a warranty by the executing company) quality and therewith time and costs are important factors. Contractors therefore chose IC to ensure a long-time quality and to work as efficient as possible with less time and less costs.? He adds, ?We continuously invest in the development of new machines and technologies that help our customers to optimise their business. We offer our customer the perfect machine for every application, whether a standard machine is demanded or high-end technology, such as the Bomag Asphalt Manager 2.?
However, IC technology has not found many takers in the road building fraternity. Reasons are aplenty initial high cost, lack of awarness among the end-user segment, non-availability of well-trained operators and absence of codes and specs that could bring a change in the selection are some the factors. Despite the proven efficacy of the system most of the road contractors have not started using it. Most of them have not deployed IC technology at any of their project site till now as the technology is in its initial stages in India. As per input many of major contractors are studying the product offerings and look forward to implement IC technology in future projects.
Says Sanjay Londhe, Director & CEO, Projects, Ashoka Buildcon, ?Since IC technology is in a very premature stage and has to go a long way, we have not started using the same. They are currently cost prohibitive and have not become mandatory from the authorities. Though definitely if proper compactometers are developed it would have created a positive impact. The current system of manual online checking of compaction level is more reliable and economical. OEMs should come up with operator schools, from where we can pick up skilled operators for using this technology in our industry.?
?We have used compactors from Dynapac and L&T for our flyover projects. We have not used IC in our projects. In India, operators are not trained for such kind of technology and it is an added cost to the company. We have not developed the kind of work culture and skill to handle such a technology in India,? says Amitesh Ranjan, Deputy General Manager, Gammon India.
?So far we haven?t used IC in our projects. It is an excellent system to monitor the progress of the project. It is helpful for big projects and big companies (main contractors) who want to monitor the progress of the work,? says Nilesh Bhavsar, Senior Manager, (Mech), BG Shirke Construction Technology.
Londhe adds, ?Generally compactors are selected on the basis of operating weight of the machine including the dynamic weight at different frequencies and amplitude settings. Operator safety and comfort, while operating the machine, is also in our minds before selection of the machine. The operating and maintenance costs, dictated by the engine capacities, the power developed, low cost of operations, high productivity and reliability influences the decision.?