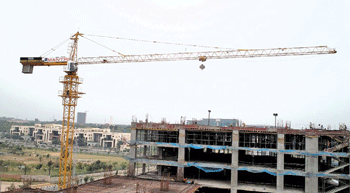
Maintenance, the Key to Performance
More than ever before, the past decade has seen the emergence of demanding customers - customers, who expect more from their assets. Domestic customers expect their home appliances to perform consistently, while industries demand superior performance from their assets. Be it power generation facilities, manufacturing industries, steel mills or infrastructure sector, everyone expects his facility to meet production targets. With the reduction in overall budgets, a purchase decision is often driven by lowest cost of equipment meeting a minimum technical specification. On the other hand, with the investment cost of equipment increasing, it is extremely difficult for customers to replace their plant and machinery before the economic life has been reached. Once installed, invariably there is a gap in customer expectation and the supplier?s service delivery. Once an equipment breaks down, the focus is to bring it back to operation as soon as possible as any downtime of critical equipment in the production process leads to huge financial losses, directly and indirectly. This has driven up a huge demand by plant managers for aftersales service providers to offer a bouquet of maintenance services to extend the life of the existing assets.
Maintenance is often explained as all those activities required to keep an equipment or a plant in its original condition so that it can retain its rated production capacity. Various maintenance approaches are prevalent in the industry today.
Breakdown maintenance
Here the repair work is conducted after the failure or breakdown of an equipment or its component. This is, in a strict sense no system at all as it is indicative of no attention given on the machine. It is actually a reactive response where the repair needs to be completed immediately as the machine has probably stopped working resulting in production down time. Hence, breakdown maintenance is very costly.
Routine maintenance
In this method, certain checks and inspections are followed at regular intervals, for example, daily checks, weekly checks or monthly checks. This is more generic in nature, for example, lubrication checks, checking of motors and electrical connections, checking the tightness of bolted connections etc.
Planned maintenance
In planned maintenance, the OEM recommends the maintenance programme on the ?what, when, how? and what tools are necessary for the maintenance. Based on the application and utilisation of the machinery, maintenance frequency is adjusted and records are kept to develop a log of the maintenance needs of the equipment.
Preventive maintenance
In a more holistic approach which anticipates failures, the equipment is routinely maintained irrespective of its actual condition. Since the repairs are anticipated to happen, and action is taken to prevent them from occurring, some of the maintenance activities may not really be required. In addition to routine maintenance and cleaning activities, a comprehensive preventive maintenance technique defines the various inspections to be carried out, what maintenance and tests are to be conducted (eg, non-destructive test and which small parts are to be replaced). It also includes the maintenance to correct any shortcomings or deficiencies captured during the inspections or which show up after testing. It is carried out for both mechanical as well as electrical components. Electricals are generally checked and corrected for loose connections, overheating, dust and dirt, depositions due to fumes or ill effects of humidity or corrosive environment. Preventive maintenance is carried out irrespective of the OEM. After preventive maintenance, the equipment becomes safer to use, almost new and hence far reliable, and it can match its originally rated capacity and capability.
Carried out by qualified personnel, a preventive is a rather expensive technique, however less expensive than breakdown reactive maintenance.
Predictive maintenance
This is essentially a knowledge-based maintenance programme based on the condition of the equipment or any component assessed from earlier maintenance or heath check activities. In a sense, it is an extension of preventive maintenance.
Having regular information about the current health of the equipment, customers obtain valuable information which then helps them decide when maintenance should actually take place be performed. Such maintenance should be performed before equipment?s rated performance drops. The age of the equipment, its application, utilisation and duty cycle and the environment in which it operates are evaluated. The idea is to predict a possible failure well in advance so that operational failures, safety hazards, production losses and expensive breakdown maintenance are avoided. This leads to a significant drop in equipment accidents.
An effective preventive maintenance strategy not only lays out the quantum of activity to be performed on specific equipment or their component/sub-assemblies but also identifies the frequency at which such maintenance is to be carried out. Predictive maintenance is reported as the least expensive maintenance technique and offers several benefits to customers such a as an overall reduction in the cost of maintenance; delivers accurate information about the current health of the equipment; operational pain areas of the equipment are identified and can be addressed proactively; improves equipment performance, reliability and productivity; data is available about when major overhauls, modernisations or upgrade can be taken up; planning and scheduling becomes easier; leads to savings in costs and reduced downtimes, and increased safety at the workplace.
EOT and gantry cranes play an important role in equipment across industries, namely manufacturing plants, heavy fabrication shops, construction industry, conventional and nuclear power plants, oil and gas industry, steel and metallurgical process plants. While they are the workhorses in the material and product handling bays in the manufacturing and fabrication industry in the steel and metallurgical industries, EOT cranes are a part of the process itself. Downtime in a crane can very often bring a plant to a standstill and cause substantial financial loss in terms of loss of production or loss of in-process raw materials. In recent times, regular health checks and preventive maintenance therefore form the backbone of an overall operation and maintenance strategy in a majority of production facilities.
Typical checks for EOT cranes
Safety check: Checking of limit switches, brakes, wire rope, wire rope clamps, electrical connections and supply voltage. Also included is any other safety aspects related to crane. Inspection and rectification as per detailed preventive maintenance checklist.
Oiling and greasing: Oil level checking and filling of gearbox, greasing of wire rope. Inspection and rectification as per detailed preventive maintenance checklist.
Electrical checking: Checking of contactors, overload relays, electrical connections, motor connections and cable checking/tightening; checking of DSL for power supply to cranes; and inspection and rectification as per detailed preventive maintenance checklist.
Alignment checking: Checking of motors and gearbox alignment for all motions. Inspection and rectification as per detailed preventive maintenance checklist. Motor checking: Hoisting, CT and LT motors checking for proper current, resistance, voltages, insulation test. Inspection and rectification as per detailed preventive maintenance checklist.
Brake settings: Setting of brakes, checking of thruster oil, checking of liners/brake discs or brake shoes; inspection and rectification as per detailed preventive maintenance checklist.
Replacements, if required
Replacement of all motors, brakes, wheels, LT complete assemblies (gearbox-coupling-brake drum-floating shaft, MH sub-assemblies, and replacement of cables and panel accessories.
Checks for any constraints faced during operations such as lifting of safe working load operating at the rated speed in long travel, cross travel and hoisting; excessive noise and/or vibrations at any location on the crane; a review of the crane log book for repeated failures and their frequency.
NDT checks: Magnetic Particle Inspection (MPI) on the hook, wire rope testing
Oil sampling
Benefits
The CMMS should be in a position to provide hard data on Response Time (RT), Turn Around Time (TAT), Mean Time Between Failures (MTBF), Mean Time To Repair (MTTR) and Right First Time (RTF) - all of which are of paramount to customers to efficiently utilise their Cranes and improve productivity.
Advantages of preditive maintenance
An overall reduction in the cost of maintenance Delivers accurate information about the current health of the equipment Operational pain areas of the equipment are identified and can be addressed proactively Improves equipment performance, reliability and productivity Data is available about when major overhauls, modernisations or upgrade can be taken up. Planning and scheduling becomes easier Leads to savings in costs and reduced downtimes Increased safety at the workplace.
Health checks in eot cranes
To check the present condition of the installed crane, and decide on the immediate corrective and preventive measures required to be taken:
Safety checks: checking of limit switches, brakes, wire rope, wire rope clamps, electrical connections, and supply voltage.
Lubrication: checking the greasing condition of LT machinery and couplings; oil level checking of gearbox, greasing of wire rope.
Electrical checks: checking of contactors, over load relays, electrical connections, motor connections and cable checking / tightening.
Alignment checks: checking of motors and gearbox alignment for all motions. Motor checks: hoisting, CT and LT motors checking for proper current, resistance, voltages, insulation test.
Brake settings: setting of brakes, checking of brake motor oil, checking of thruster oil, checking of liners / brake discs or brake shoes. General checks: visual checks for any structural /mechanical deformation; inspection of LT and CT wheels for wear and tear.
The author is CEO, Cranedge India.