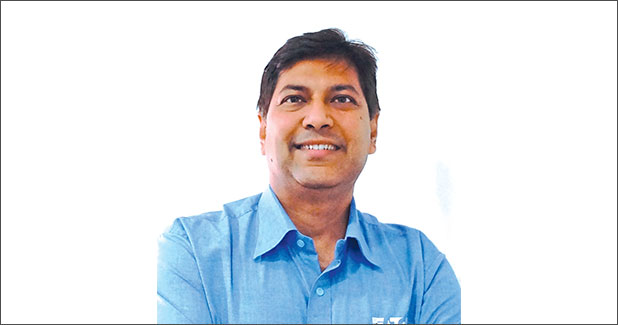
OEMs are looking for more robust hoses
<span style="font-weight: bold;">Eaton has a wide range of product offerings in fluid conveyance that meets the need for innovative products at optimised cost and NVH performance. </span><p></p><p> <span style="font-weight: bold;">Shandar Alam, Managing Director - Hydraulics and Vehicle, India, Eaton, </span>elaborates on the technology trends.</p><p> <span style="font-weight: bold;">What are your product offerings and solutions? Do you offer customised products? </span>Eaton has a very wide range of product offerings in fluid conveyance that meets the need for innovative products at optimised cost and NVH (noise, vibration and harshness) performance. Eaton's two-tiered (standard and premium) product strategy for hose and fittings enables end-users and OEMs to select products based on application. </p><p> In our product portfolio, we have all ranges and sizes of hoses from 250 to 16,000 psi, extensive range of industrial hoses right from air/water transfer to high abrasive and high critical applications like cement, concrete transfer, dry material and bulk transfer, mud suction and discharge etc. We also offer a variety of hose fittings, tube fittings, quick-disconnect couplings, Flexmaster joints and snap-to-connect (STC) connectors. We have recently introduced one and two wire braided hose in one million cycles with higher operating pressure, temperature and half-bend radius to meet specific OEM requirements. We also offer customised products like concrete hoses and carbon injection hoses for steel mill application that cater to regional and global requirements. Uptime of capital intensive equipment is very critical and Eaton has always focused on the product performance and reliability by developing and delivering fluid conveyance solutions that last multi-million impulse cycles. For example, our high-pressure Dynamax hose is tested and qualified for three million impulse cycles. This is a first in the industry.</p><p> <span style="font-weight: bold;">What are the new developments in materials to meet the requirements of: operating pressure range, abrasion resistance, durability, and transfer capabilities?</span><br />For improved product performance, some of the commonly used material in hoses include chlorinated polyethylene (CPE), nitrile rubber (NBR), chlorosulphonated polyethylene (CSM) and EPDM. For fittings, carbon steel (12L14,1215, 1045) and stainless steel (304, 316 grades) ensure superior performance. Eaton's new DURA-KOTE? plating technology offers up to 1,000 hours of corrosion resistance on the metal parts. Eaton also provides adapters as well as protective coils/sleeves for additional hose protection on extreme abrasive conditions in construction and mining applications. </p><p> <span style="font-weight: bold;">What do customers look for while choosing a hose/fitting? How do you meet these parameters? How do the features vary with light to heavy applications?</span><br />Construction applications demand higher flexibility and tighter bend radius in hydraulic hoses for enhanced installation and routing capabilities on equipment. Hoses have to deliver higher product life and abrasion resistance to support extremely demanding duty applications and tough working conditions that mining and construction equipment operate in. </p><p> Selecting suitable hoses and fittings for the required application thus becomes very critical. Hydraulic hoses and fittings are designed to carry hydraulic fluids with high pressure and high temperature, and are important elements for hydraulic systems. The 'STAMPED' principle that focuses on seven factors, (namely Size, Temperature, Application, Material, Pressure, Ends, and Delivery) is generally used while selecting a hose. Fitting selection mainly depends on factors like versatility, reliability, pressure rating and applications.</p><p> Eaton's highly engineered hoses and fittings are designed to efficiently meet these application requirements. </p><p> <span style="font-weight: bold;">Do you see a shift towards safer/sturdy hoses to effectively prevent leakages?</span> <br />Certainly, a lot of awareness related to safety and leakage is being created in the hydraulics industry. Nowadays, OEMs are looking for more robust hoses which will not only eliminate leakage problems, but also improve overall efficiency of the system. </p><p> <span style="font-weight: bold;">What is the average life of a hose? What maintenance practices need to be followed to meet this life period and further extend the hose life?</span><br />According to the specifications stated by the Society of Automotive Engineers (SAE), the shelf life of a bulk rubber hose is 10 years from the date of manufacture and is considered unlimited for thermoplastic hose, if stored in subdued light and controlled temperatures with no fittings attached. But in use, so many variables come into play that it is impossible to exactly predict the service life of a hose assembly. However, understanding important operating parameters that affect a hose, combined with a bit of experience, can help guide users as to when an assembly should be replaced. The average life of a hose depends on its manufacturing process as well as its design i.e. tube and cover material, reinforcement, fitting integrity and accuracy etc. In addition, some important factors that impact the life of a hose are operating pressure and temperature, routing, pressure surges, ambient temperature, bend radius and fittings. It is very important to monitor hose assemblies and carrying out preventive maintenance as it is critical to ensure safe and productive operation of hydraulic systems and also enhance the life of the hose. </p><p> In the case of hydraulics, high pressures and temperatures make hose and fitting maintenance as well as component selection particularly important. </p><p> Eaton's Lifesense? hose is a path-breaking technology in hose condition monitoring system. The technology is capable of forewarning the user of impending hose failure, while, the customer hitherto was dependent on either preventive maintenance that deprives the user of full life usage of the hose, or changing the hose as and when it fails, which poses potential safety issues, downtime costs and loss of expensive lube oil that is detrimental to the environment.</p><p> <span style="font-weight: bold;">What are your future plans in product design and development?</span><br />Hose and fittings have applications in diversified segments such as construction and agriculture equipment, steel mills, oil and gas, and material handling. When these end-markets do well, hose and fittings market are bound to perform and grow. We are anticipating tremendous growth in these markets because of favourable government policies and new initiatives (smart cities, mega corridor, Bharatmala project etc) and feel that the business for hoses shall also rise in accordance. </p><p> The market is moving towards more compact hoses that offer a longer life, more flexibility and a higher operating pressure and temperature. On the fittings side, the current focus is on higher corrosion resistance, zero leakage and improved torque. The key would be to deliver greater value to equipment manufacturers while maximising uptime. This offers an opportunity for a technology- and innovation-driven organisations like ours to keep developing efficient and smarter solutions that are efficient, safe, reliable and sustainable. Eaton is already innovating in this direction and our hose solutions such as LifeSense<sup>®</sup> and Dynamax<sup>TM</sup> are clear examples of this focus. </p>