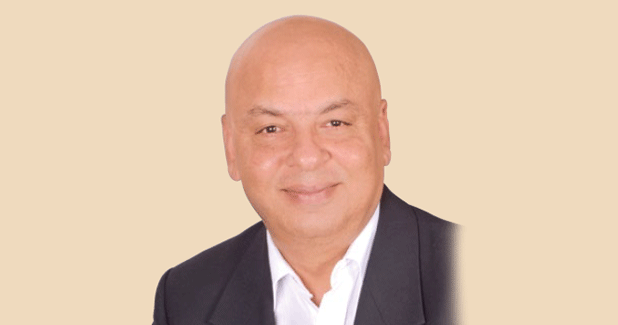
Our core values are interaction, innovation and commitment
What is the demand-supply scenario for DTH/TH solutions offered for mining sector?
In 2015, we have seen an inflow of volume business for rotary blast hole drills from state-owned enterprises involved with coal mining and we expect the trend to continue in April-June 2015 period as well. This current and expected demand will boost utilization of our ?Drilling Solutions? assembly facility at our Nashik plant. We also offer DTH drills for limestone quarrying and these are from ?Surface Drilling? division which has separate assembly set up at our Nashik plant. With the expected surge in infrastructure investment, we also see increased interest in capex from cement. The cement production is expected to grow from 262 million tonne per annum (mtpa) in 2014-2015 to 302 mtpa in 2015-16. This will result in increasing limestone production from 420 mtpa to 480 mtpa.
Rotary/DTH drills are made in our Nashik plant. In addition, higher technology rotary/DTH/TH drills which are assembled in our state of the art facilities in the US and Sweden are also quite prevalent in India. We therefore expect to meet the enhanced demand in mining by supplying from India and US/Sweden. We expect burgeoning mining output in India will generate volume demand for our products over the next few years.
Brief us on the solutions provided by Atlas Copco for underground mining.
Atlas Copco is a global leader in underground metal mining. In India, there are limited opportunities for underground metal mining and these exist in uranium, zinc/lead and copper. We offer complete solutions in underground metal mining by offering products covering the excavation cycle including face drilling, rock bolting, production drilling, loading equipment (load haul dump as well as continuous loaders), transportation equipment (trucks), ventilation equipment and shotcrete equipment. We have significant number of underground mining machinery operational with Uranium Corporation of India and Hindustan Zinc.
Brief us on your core competencies?
Our core values are interaction, innovation and commitment. Everything we do is aimed at achieving our vision of becoming and remaining First in Mind-First in Choice?. The core values express what we stand for, what it takes to serve our customers effectively and to reach this vision. Interaction refers to our ability to listen and to understand the diverse needs of our customers and other target groups coupled with our capacity to create new and better solutions.
We are fully committed to our customers? business and totally engaged in each and every project we undertake together. We believe in lasting relationships. Finally, we believe that there is always a better way of doing things. That explains why Atlas Copco is continuously striving to arrive at better and more efficient solutions. That innovative spirit is a vital part of our way of doing business. We are a direct selling organization and two-thirds of our sales in India is done directly to customers. We seek feedback on our deliverables from customers every year and this is done globally. Listening to customers gives us deep insights and we align ourselves based on demands of customers.
Could you give us an example?
To explain the above, Hindustan Zinc purchased a lot of high capacity underground mining equipment from Atlas Copco Sweden and entered into a 24x7 Service Agreement with Atlas Copco India wherein we would maintain the equipment for a period of five years and guarantee uptime for all the machines. HZL would pay a pre-determined price for getting service and spare parts and this was calculated on operating hour basis. Customer thereby pre-fixed their operating cost and KPIs based on which equipment performance would be evaluated and left the balance operations to us so that they could concentrate on areas closer to their core. We are today doing this at five different underground mines of Hindustan Zinc covering 80 equipment with 200 personnel.
Investments to support the above include setting up of a Distribution Centre at Bijaynagar, Rajasthan where we stock parts/components and consumables. We have also set up a state-of-the-art training centre there equipped with simulators so that operators are trained on drills and loaders resulting into proper operation (and less abuse of equipment) when working underground.