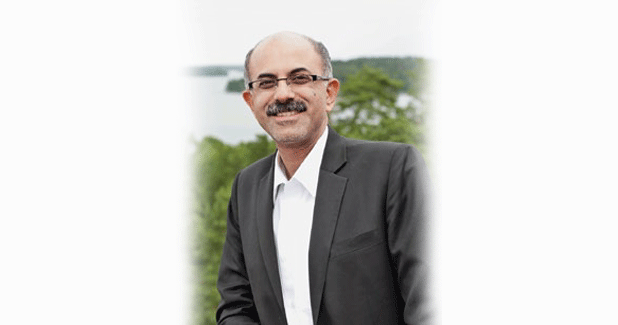
Our hydraulic breakers are loaded with features such as Krupp percussion technology
Atlas Copco India, Construction Technique Customer Center.
Atlas Copco is committed to continuous innovations and improvement in the current product design. With opportunities to launch new products in India from the global Atlas Copco portfolio, we expect many firsts and we hope to launch the world?s most powerful hydraulic breaker shortly, says Nitin Lall, General Manager, Atlas Copco India, Construction Technique Customer Center.
Excerpts from the interview...
How do you assess the growth prospects for rock breakers?
The total market has remained more or less constant with a minimal 2-3 per cent growth. 2015-16 will remain stagnant with respect to the previous year. We expect growth in the first quarter of 2016 because of new projects which are getting announced now. There will be a certain time lag before we start the impact of these projects in the market.
We expect 4,500 units as an estimation of the breaker market in 2015. If the business environment supports the market, then we expect the market size to grow between 7,000 to 8,000 units in the next five years.
What is the range of rock breakers offered and what is the carrier range it can be mounted?
We have our rock breakers suitable and successfully commissioned on every type of carriers / excavator from 140.00 kg to 700.0 tonne class. Our hydraulic breakers range from the most powerful breaker in the world, the HB1000, to the smallest breaker. Our existing range now caters to every segment in the market. We cover the entire spectrum of the market, that is, for customers needing productivity as their main focus and also for the hiring segment which is our range from the value segment.
In India, breakers suitable for 20T excavator class dominate the market with 2,000 units. The Atlas Copco MB1500 medium hydraulic breaker and the EC135 breaker are the products pitched to this specific segment where the MB1500 is the most popular breaker in our portfolio.
Do you also supply the entire conversion kit?
We also supply the conversion kit for the equipment. However, customers have the choice of buying the conversion kit from the excavator OEM or Atlas Copco. We source these items from Atlas Copco approved, quality conscious vendors only. It is recommended to our customers to purchase only Atlas Copco genuine parts/conversion kits to benefit from the most efficient performance of the equipment. As such, Atlas Copco does not have any tie-up with any specific carrier supplier.
What are the most common applications for which your rock breakers are used in India?
Secondary breaking in aggregate quarries, foundation/breaking in building projects, primary breaking in mines are the most common applications for hydraulic rock breakers in India. Besides this, applications such as building demolition and tunnelling are some other applications in India. New global applications such as piling and underwater breaking may find some scope in India in the future.
What are the special features your range of breakers?
Atlas Copco hydraulic breakers are loaded with features such as Krupp percussion technology, and highest power to weight ratio which makes our breakers optimum for maximum productivity as well as long life of the carrier.
Atlas Copco hydraulic breakers have several additional unique features which ensure minimum machine downtime. Specifically, the Conti Lube which is a self-priming lubrication pump with adjustable grease volume is designed for uninterrupted operation and optimised lubrication. Autostop mode is another feature where the hydraulic breaker starts without load applied to the working tool thus simplifying handling. In the AutoStop mode the hydraulic breakers runs only when load is applied to working tool thus preventing blank firing. With minimal wear and tear of parts the machine does not remain idle.
Further, selection of different modes while operating the breaker according to the operating conditions, leads to reduced fuel consumption of the excavator. Impact power is defined by impact energy by the breaker times the blows per minute. Atlas Copco has the highest impact energy for each breaker in every category coupled with energy recovery mode. So when it comes down to productivity, we deliver maximum power irrespective of any application as compared to other breakers in the market.
Could you elaborate the Krupp percussion technology?
Our breakers are incorporated with Krupp percussion technology, which makes the breakers with highest power to weight ratio. For example, our 20T class breaker MB1500 weighs only 1,500 kg (includes weight of adaptor plate and chisel) and delivers maximum impact power with 30 per cent more productive compared to others carrying dead weight of nearly 2,000 kg.
Krupp percussion technology makes the breaker use only 30 per cent of the hydraulic power and rest of the energy is provided by the nitrogen gas which is aided by features such as auto control and start- select which helps to reduce the fuel consumption to the minimum.
Are you making any efforts to reduce the noise pollution created by rock breakers?
Our breakers are vibro-silenced and hence our breakers make minimum noise when in operation compared with any competition in the same category. However, we always strive to further reduce these sound levels through continuous innovation.
What are the challenges encountered by you in this range of equipment?
Excavator manufacturers in India supply economical rock breakers which erodes the market share of high quality manufactured breakers. Further the current stagnant market scenario due to lack of construction projects and a slow mining market, all together are challenges faced in the breaker market. We foresee a new bright future for all contractors in India. Whether small, medium or large scale contractors all will be active in India.