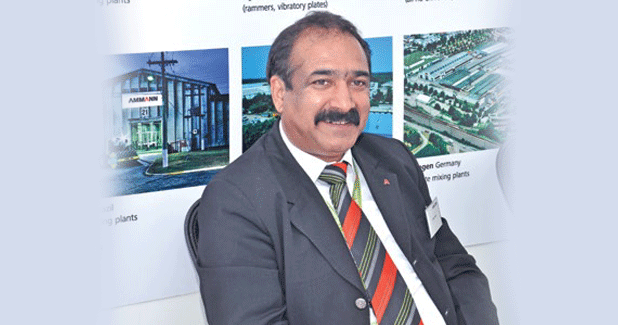
Our plant can provide better energy saving
Two global players, Ammann from Switzerland which is into asphalt mixing plants for the last 150 years, and Apollo being in India for the past four decades, which is into asphalt mixing plants and other allied road equipment business, joined hands where Ammann has 70 per cent stake and Apollo the remaining 30 per cent stake in the JV. Sunil Sapru, Chief Executive - Marketing, Ammann Apollo shares his views with EQUIPMENT INDIA. Excerpts from the interview...
What was the real technology of Ammann Group attracted it to Apollo or vice versa?
It is basically the strength of Apollo in India and the way Apollo is known to its customers, while at the same time, the popularity of Ammann in Europe as one of the leading asphalt plant technology and solution providers. They have been investing in research and development, developed individual components with their own patent. They have plants which are thoroughly tested over generations and technologically superior as of today. We wanted to bring in this technology innovations into India so Indian customers will get the best technology with customisation. We had conceived the vision of Make in India two years before the Prime Minister announced it recently and did the joint venture of Ammann Apollo.
Are you introducing the oscillating flame technology in India?
We have all options available from oscillating flame to multi fuel burner, gas burner etc. Our plant can provide better energy saving as the thermo drum gives better heat transfer efficiency within the virgin aggregates. The heating gets transmitted to the aggregates and the heat will not go out of the plant for which we have a specialised flight design to reduce wastage of energy. We have designed products in such a way that it can take a very high standard of heat resistance to those flights which can go up to 400oC.
In Ammann, the technology where they talk about the negative pressure creation within the drum is phenomenal. The knockout box designing and getting the fines to the baghouse is being controlled by a VMT drive through the exhaust, and it is perfectly controlled. We can de-dust the fines up to 20 micron while the international norm is 50 micron.
The core components of our plants are manufactured in-house. Around 60 per cent components are manufactured in India and 40 per cent are imported.
How different are warm-mix and cold-mix with hot-mix batch plants?
In hot-mix plant, the mixture is being heated up to a temperature of about 160-165oC, in the warm-mix, the temperature is 130-120oC, while cold mix can be below 100oC.
In India, the maximum permissible axle load is 9.8 tonne as per NHAI standards. Will the cold mix meet this requirement?
It is a tried and tested technology. Ammann Apollo is offering a solution to the customer which is a future ready plant. All the plants will have the kind of adaptability that whatever technologies require in future can be adapted into the same plant and need not go for a new plant.
What software you use at Ammann Apollo product range?
We use the software AS1 which is exclusively developed by Ammann. We can access the plant from anywhere in the world and can be remotely operated.
What is the scope for low energy/low temperature asphalt mix?
This is very much possible. Our proven foam technology enables production of warm mix with comparable quality of mix and road performance. This can result into several benefits - cost, lesser carbon foot print, reduced fuming of bitumen and cleaner paving site.