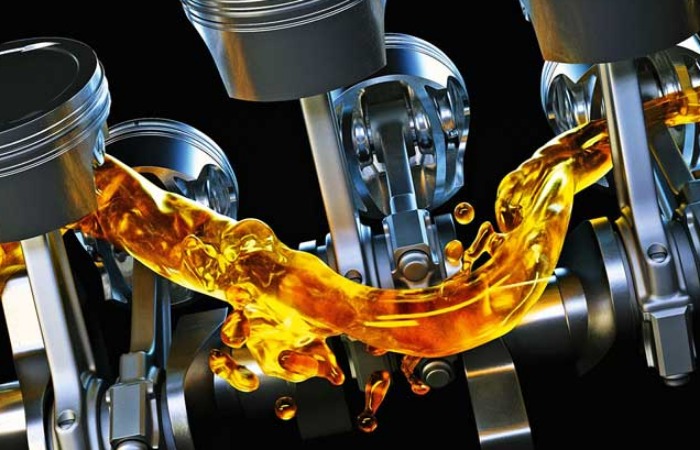
Reducing friction
Lubricants play a vital role in construction. The equipment needs to perform under severe conditions, from heavy loads and extreme temperatures, to excessive wear and dirt and water contamination. Such challenges mean it is essential to provide optimal protection.
Since construction, operations often move frequently from location to location, a maintenance team will not always be nearby. Machine breakdown can lead to long unplanned downtime and unexpected costs, which all equipment owners and operators hope to avoid.
Choosing the right lubricant is essential in helping to improve reliability, boost productivity and reduce the frequency of breakdowns. It is important to consider what factors will affect whether a lubricant will be effective for its intended purpose. With engine oils, some of the key considerations are viscosity grade and performance attributes.
Says Rupinder Paintal, Director of Market Development, ExxonMobil Lubricants, “The construction equipment (CE) companies in India are responding to the benefits of technologically superior world-class application-specific lubricants that yield huge dividends in terms of improved productivity and significant cost savings. The lubricant industry is gearing up to meet the needs for customised specialty products, giving Indian customers best-in-class products developed through global expertise of decades. The trend is of synthetic lubricants, or like we call them, designer lubricants. Synthetic lubricants differ significantly in composition and performance from conventional lubricants. The new generation of Mobil lubricants aptly demonstrates the immense value created by synthetic lubricants.”
Speaking on the range of equipment for the construction industry, Paintal said, “Our offerings for the construction and mining equipment have been designed specifically to meet the needs of customers with heavily loaded equipment that require high EP/anti-wear performance. We have a portfolio of advanced product offerings for various types of infrastructure equipment. The customised lubricants for the mining sector include Mobilgrease XHP 321 Mine and 322 Mine. The Mobilgrease XHP Mine series has excellent extreme pressure and anti-wear properties in addition to exceptional staying power, good water wash-out, water spray-off and extended service capabilities under harsh operating conditions.”
Lubricants are available in different Society of Automotive Engineers (SAE) viscosity grades, which dictate the acceptable temperature range in which they can perform optimally.
Improved aeration control is also particularly important for off-highway engines due to the potential for more air than usual to become entrained within the oil. At the bearings, this can prove dangerous, as these components need an oil film to protect them. Entrained air is detrimental as it interferes with boundary lubrication, or the thin oil film that protects against metal-to-metal contact.
Praveen Nagpal, Chief Technology Officer, Shell Lubricants India, said “The Indian lubricant market is witnessing steady growth due to the rise in the demand for industrial equipment. Over the past few years, there has been an increase in construction, manufacturing and mining activities, which have increased demand for high-performance industrial lubricants for the efficient and productive operation of heavy machinery. Mining equipment work in severe operating conditions.”
Adds Nagpal, “Industries are embracing technologies and equipment maintenance solutions, and Shell, with its deep industry knowledge, expertise and resources across operations, is leading the way. Our expertise lies in developing the highest quality of lubricants using the best-in-class technology to deliver the desired results to customers while meeting industry needs.”
Ravi Chawla, Managing Director and CEO, Gulf Oil India, said, “We have been pioneers in long-drain oils with Ashok Leyland since 2006. Before 2006, people were changing commercial vehicle oils at a drain interval of 18,000 km. We brought this oil for a drain interval of 36,000 km and now this is 80,000 km. We have been working closely with OEMs establishing our customer base. Our global R&D is based in India as the global team can offer our products and we are now going to more OEMs to partner with co-branded genuine oils. We are also offering our oils and services to Schwing Stetter, BharatBenz, Kobelco and we have just announced a tie-up with Doosan. We are trying to tie up with more OEMs and looking at working closely with OEMs to offer products which will suit their engines.”
Adds Chawla, “Gulf Oil recognised the importance of the infrastructure sector in a developing country like India and early on, we set up a dedicated team to cater to the needs of this sector. Today, 6-7 per cent of our sales volume comes from this segment. We offer customised products and services at more than 5,000 sites and to more than 1,000 customers who are building roads, highways, metros and houses. Our customer focus and service-oriented approach has helped us grow the business from this sector year on year. However, the last one year has been challenging for all of us due to slow progress of projects and slowdown in overall market. Despite this, we are still gunning for growth.”
Nagpal concludes. “The Indian industrial lubricant market is estimated to grow to $1.67 billion by 2023, from $1.28 billion in 2017. The growth in construction, mining and material handling equipment sectors across the country has seen a rise and is expected to create more and newer opportunities for the industrial lubricant sector. Heavy equipment and machinery will demand fuel economy benefits from lubricants to increase their potential savings from effective equipment lubrication. These equipment require lubrication with low viscosity, high durability and longer oil drain intervals. This is where lubricant companies like Shell will come to the rescue. We deliver lubricants formulated with advanced technologies that will equal their total lubricants spend and further impact their maintenance budgets.”