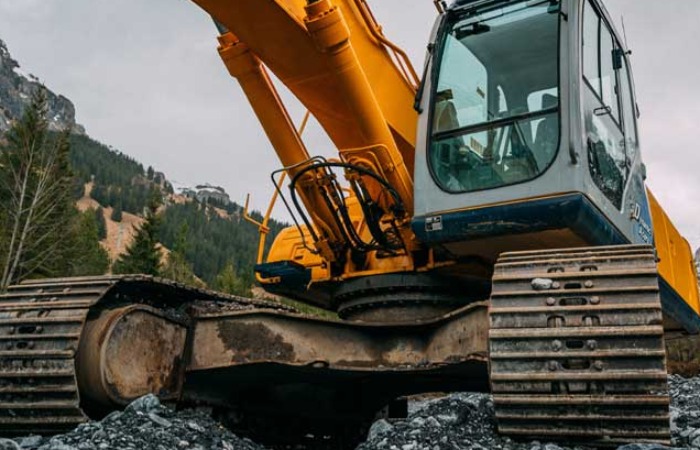
Rolling Strong
The undercarriage is a series of components assembled into a complex mechanism to support and move a construction machine. In heavy machinery, wheeled and tracked undercarriages are responsible for: Moving the heavy equipment around different types of uneven terrain, providing a stable platform to lift and carry objects, distributing the machine’s weight evenly so it doesn’t sink into soft ground, and protecting the heavy equipment from harsh conditions to keep it operating safely and efficiently.
Without undercarriage, there won’t be excavators, wheel loaders, or compact track loaders. And without heavy machinery, the construction industry won’t be able to function because they perform various tasks humans can’t, improving safety and increasing efficiency.
The lifespan of an excavator undercarriage depends on various factors, including the quality of the components, the type of terrain the equipment operates on, and the usage and maintenance practices. On average, undercarriage components such as track chains, rollers, and idlers can last between 2,000 to 7,000 hours of operation. However, this lifespan can vary significantly based on the aforementioned factors. For instance, heavy-duty usage in harsh terrains with rocky or abrasive surfaces can result in faster wear and require more frequent replacements. On the other hand, proper usage, regular maintenance, and using high-quality OEM-recommended components can extend the lifespan of the undercarriage.
Recent track technology and undercarriage technology innovations provide operators with more safety and comfort and extend equipment life and efficiency. These latest developments also help overcome longstanding challenges in the industry, such as operating sensors in harsh environments. Tread designs and rubber compounding define recent trends, leading to longer-lasting, smoother running tracks, said Mike Giordano, Yokohama TWS segment Sales Manager, Rubber Tracks.
While the goal to integrate into an onboard notification system on a dozer can be accomplished, the challenge is in the environment in which the components with sensors are operating, noted Tim Hansen, CASE undercarriage product marketing manager. Extreme conditions–sand, abrasive, and hard rock applications–wreak havoc on sensors for sustainability and dependability, he said. With CASE TrackCare, end users plan maintenance activities, monitor performance and make decisions to help manage undercarriage performance and costs.
The CASE TrackCare monitoring programme is designed as a cloud-based system, a mobile app and Ultra Sonic tool for collecting undercarriage measurements and observations in the field for CASE machines and all makes.
Undercarriage improvements are enhancing durability, efficiency, and overall performance. They often involve the use of high-quality, wear-resistant materials designed to withstand harsh conditions and abrasive materials. Undercarriage configuration varies significantly based on material application and type.
Contractors should balance undercarriage wear across all components to get maximum undercarriage life before required maintenance. Deere’s dozer design process focuses on suitably distributing weight to properly balance the machine and distribute it more evenly to reduce component stress, premature wear, and failure. Deere constantly monitors machines in various regions to determine how different material types impact undercarriage wear.
Deere recently updated its small dozer 450, 550, and 650 P-Tier models to boost productivity and operator comfort while lowering operating costs. New to its technology stack is EZ Grade, in-base on machines with electro-hydraulic controls. It monitors the machine’s altitude, automatically making blade corrections to maintain a smooth grade. EZ Grade is upgradeable to Slope Control technology, which automatically controls the blade to a desired slope. Machines can be upgraded to full 3D SmartGrade when available.
Updated joysticks in Deere’s mid-size dozer lineup are designed for improved ergonomics, incorporating proportional blade angle controls, and reducing arm movement for reduced operator fatigue.
The CASE dozer line has a smooth, one-piece track frame featuring greater structural strength and allowing for easier cleanout, noted Hansen.
With CASE Ultra Life, a wet rotating pin and bushing-style chain is designed to provide a quieter and smoother ride and offers a service life of 5,000 hours or more. Increases in width of the track rollers, carrier rollers and the idler on all CASE dozer undercarriages improve structural integrity, reduce wear, and achieve greater balance, said Hansen.
The Max Life track is believed to extend track life by as much as 15 percent under the right conditions and applications, Hansen said. Since undercarriages make up more than 50 percent of a dozer’s maintenance costs, CASE has designed undercarriages to make maintenance easier, including easy-to-reach critical pivot shaft grease points and equalizer beam joints. In addition to CASE’s standard sealed and lubricated heavy duty tracks, Ultra Life and Max Life extended life options, CASE offers three different track options for each M Series dozer model.
Italtractor ITM Spa (ITM) and DOZCO India announced the creation of a joint venture company called ITM DOZCO. The intention of this joint initiative is to create the leading manufacturer of undercarriage components in India to optimise service to local and global customers. The company will offer a full range of undercarriage components and complete track systems for earthmoving machines. The joint venture will cover the Indian market needs as well as requirements for global customers across all industries. This agreement follows years of successful cooperation between ITM and DOZCO.
The undercarriage of heavy equipment plays a critical role in the performance, stability, and longevity of the machines. Regular inspection, proper usage, and maintenance are essential to detect and resolve issues early on, prevent costly repairs, and ensure optimal performance. The use of high-quality OEM-recommended maintenance products can further enhance the lifespan and performance of the undercarriage. By investing in proper undercarriage maintenance, heavy equipment owners can maximise the productivity and efficiency of their machines, ultimately leading to better returns on investment.
5 things to look for when inspecting an undercarriage
Regular inspection of the undercarriage is crucial to identify any potential issues. This allows for them to be addressed before they turn into major problems. Here are some tips on what to look for when inspecting an undercarriage:
- Track shoe wear: Check for any signs of excessive wear, such as uneven wear patterns, cracks, or missing track shoes. These can affect the machine’s stability and performance.
- Track chain tension: Ensure that the track chains are properly tensioned. Loose or overly tight chains can cause premature wear and damage to the undercarriage components.
- Roller and idler condition: Inspect the rollers and idlers for any signs of damage. This means cracks, dents, or missing parts, as they play a crucial role in supporting the weight of the equipment.
- Sprocket condition: Check the sprockets for any signs of wear, such as worn-out teeth or misalignment. They are responsible for propelling the machine and need to be in good condition.
- Track adjuster function: Ensure that the track adjusters are functioning properly. They are responsible for maintaining the tension in the track chains and ensuring proper alignment.