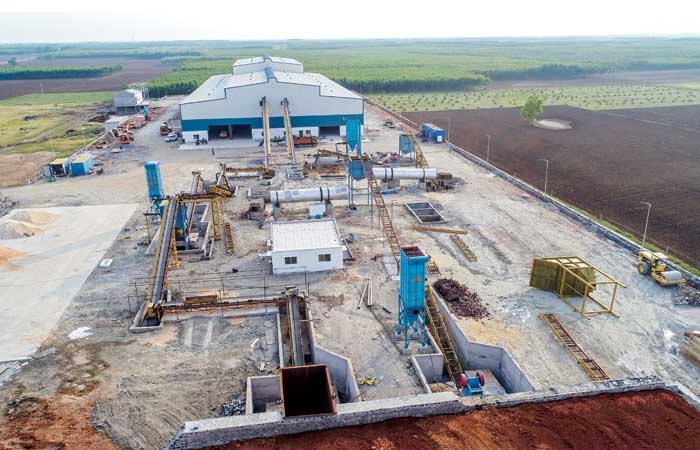
The Crushing Evolution!
The crushing and screening equipment market is poised for robust growth, projected to expand by 13 per cent annually from 2023 to 2027. With the escalating demand for artificial sand, the significance of crushing and screening machinery is steadily rising. After enduring a prolonged period of business stagnation in recent years, manufacturers of crushing and screening plants are now witnessing a gradual but discernible uptick in demand. The crushers and screens market holds vast untapped potential, especially with the recent extension of the government's Rs 111 lakh crore ($1.5 trillion) National Infrastructure Pipeline (NIP) to encompass additional projects by 2025. This expansion of the NIP is expected to generate heightened demand for crushers and screens.
Furthermore, the Punjab Government has recently sanctioned the Punjab Crusher Policy 2023, aimed at providing consumers with access to sand and gravel at fair prices. Under this policy, crusher units are primarily categorised into commercial crusher units (CCU) and public crusher units (PCU). Notably, the policy stipulates that crushing units must incorporate screening, washing, and sorting facilities.
Speaking on the Indian market for their products, Wayne Van Antwerpen, Group Crusher Technology Product Manager, Terex Material Processing, said, India is a unique market. While we may have successfully improved product performance in other regions, the Indian market is very price-sensitive. So, any changes must prioritise cost reduction. However, we also need to account for differences in skill levels among machine operators. Indias labour force, much like in some other regions, may not possess the same level of expertise. Hence, we have been delving into automation controls to make our machines user-friendly, safe, and less prone to malfunctions. Weve developed these solutions locally to cater to the specific needs of the Indian market. Its crucial to have a more connected approach to meet regional demands effectively.
He added, For automation controls and crushing chambers, the Indian market is distinct. Certain types of crushers are more popular in India than others due to their unique materials and demands. Our challenge is to introduce new concepts and technologies like automation controls, which might initially appear costly but can significantly boost productivity. The Indian market needs to embrace technology, just like how people use advanced features on their smartphones. We aim to open doors for Indian customers to realise the benefits of innovation.
Terex Material Processing is actively focusing on digital solutions, telematics, and electronic controls. These digital technologies not only enhance product performance and reliability but also contribute to sustainability and safety. We aim to reduce environmental impact and improve safety while providing cutting-edge technology to our customers.
Added Antwerpen, In todays environment, developing entirely new crushing technologies is both challenging and time-consuming. Therefore, our primary focus is on improving existing technologies to make machines safer, easier to operate, and more productive. Environmental considerations are also crucial. We aim to remove components with toxic elements, reducing health and safety risks and environmental contaminants. Additionally, we are working to eliminate the need for oxy-acetylene cutting and welding, as these processes release harmful substances into the atmosphere. So, our main goals are to enhance safety, productivity, and environmental sustainability.
Neil Robinson, Product and Applications Manager, Powerscreen, said, Powerscreen Maxtrac 1300 is a medium to large-sized track mobile cone crusher that is ideally suited to secondary applications. Its an extremely reliable machine. Ive visited three of these in Australia, and each of them had over 23,000 hours of operation with minimal issues. Were also working on introducing a fully electric variant for our machines, which aligns with the growing trend of electric vehicles in India.
Speaking on energy efficiency, Robinson added, Efficiency is a primary focus for us. Take the Chieftain 2200, for example. The technology in the screen allows for more aggressive screening, which results in higher-quality products and increased productivity. This means you can achieve more with the same amount of fuel, ultimately reducing operational costs. Additionally, our machines can often do the work of multiple machines, reducing the need for additional fuel and labour. For instance, two operators can manage two machines, but with our technology, one operator can handle the work of both, reducing fuel and labour costs. Furthermore, our hybrid and electric solutions provide additional fuel savings.
We view India as a fundamental market for the MB Crusher. Our commitment to providing innovative solutions in the construction and road construction sectors aligns perfectly with the evolving needs of the Indian market. Over the years, MB Crusher has garnered substantial recognition, emerging as a key player in the industry. Our strong brand recognition and the trust our customers place in us underscore our positive outlook on the Indian market. With a diverse range of products catering to the specific needs of the market, we are well-positioned to meet the demands of the growing construction sector in India. We believe that India is a pertinent market for the advantages offered by MB products and their features, given its vast geographical expanse. People often work in remote locations, including challenging environments like mountainous areas, making the attributes of MB products particularly beneficial in such scenarios, said Piero Guizzetti, CEO, MB Crusher India.
He added, Sustainability is at the core of MB Crushers ethos. We take significant steps to address environmental concerns through our product offerings. Our machines are purposefully designed to align with the principles of Reduce, Reuse, and Recycle. This commitment runs through every aspect of our product design and development. One notable advantage is the minimal environmental impact of our product category. In contrast to other options, our units operate without the need for electricity and do not incur any extra fuel consumption beyond the standard operation of the base machine. This makes our solutions the most energy-efficient and eco-friendly choice available. We are continually improving our products and processes to further reduce our environmental footprint while enhancing project safety. Our goal is not just to meet industry standards but to set new benchmarks for sustainability.
Metso has bolstered its manufacturing capabilities for mobile track-mounted crushing and screening equipment in Alwar India. The recently-opened manufacturing facilities will increase the Alwar factory's size to approximately 3,40,000 sq m, a 35 per cent expansion from its initial establishment in 2008. With around 1,300 employees, the Alwar site has become one of Metsos largest manufacturing sites. The official inauguration occurred on September 19 2023 and production will gradually ramp up to full capacity by year-end.
Markku Simula, President of the Aggregates business area of Metso, emphasised the factory's strategic importance stating. With an increased manufacturing capacity, Alwar becomes a key Metso site for expanding domestic operations in India and meeting the needs of Metso's global customers. Substantial investments have also been made in engineering and R&D resources establishing it as one of our primary global engineering hubs.
The Alwar factory will facilitate the production of various Metso Group brands. Alongside mobile Metso Lokotrack equipment, the expanded capacity in India will support the manufacturing of mobile McCloskey and Tesab equipment. Furthermore, the Alwar site will continue to produce essential wear parts and pumps for the aggregates and mining industries.
Metsos intelligent crushing and screening offering is expanding with a new software application called Metso Remote IC. The new Metso Remote IC is used for remote control and monitoring of the crushing and screening process, and it connects wirelessly all the Lokotrack® crushers and screens at the site.
With the Metso Remote IC app, the operator can view all the Lokotrack train machines and their main process parameters using a single dashboard. The feeder and crusher settings can be adjusted safely from the excavator cabin, and the overall visibility of the process allows the operator to adjust the feeding for an optimal production level. In problem situations, the Remote IC automatically stops the feeder, thus preventing overloading. It also instantly alerts and provides a reason for the stoppage, making it quicker and easier to get back to operation. With a lower overflow risk, the process can be run closer to maximum capacity.
Preferences
While the must-have features of a crushing and screening unit depend on the specific needs and goals of the operation, Nachimuthu Krishnamurthy, Vice President - Operations, Transworld Garnet India, highlights the top desirables as best-in-class efficiency, robustness and automation; versatility; and easy maintenance, durable components and effective monitoring. Only then can you maximise the units throughput and output, reduce the processing cost per tonne and improve profitability irrespective of the material handled, aggregates, minerals or recycled materials.
Drilling down to the application, some industry-specific features come to the fore. For example, in the construction and aggregate industry, features like mobility, compact design and dust control systems may be critical, while in mining, heavy-duty components, automation and remote monitoring might take precedence, he adds. Aligning the features with the application is vital for the success of the unit.
At Transworld Garnet India, we prioritise energy-saving, environmental safety (including compliances) and worker health and safety features of crushers and screens, responds Krishnamurthy.
Screen must-haves
We look for a manufacturer who is willing to work closely with us on the entire process plan, including the steps before screening and post screening, and understands material characteristics such as flowability, bulk and particle density, particle size distribution, moisture content, temperature, material shape and the cut points to be achieved, says Bharath Shetty, Director, Silica Mines. Only then can screen sizing, type and design ensure success. Good design should reduce recycling loads and cross-contamination of product sizes, simultaneously focusing on optimal power consumption and minimal wear. We have found such a manufacturer in PSI Technologies Inc. It has successfully delivered high-frequency double-deck screens to our silica mines for grading 1,200 and 600-micron grades at 10 tonne/hr capacity.
We look for productivity in a screen used to make plaster sand, says Kiran Jain, Director, Shri Dakshayani M Sand. If we feed 150 tonne of dry sand to a machine, in the machine of our choice (Proman), we get 30 per cent more plaster sand. In other machines, we have achieved only up to 15-20 per cent more output. In the case of water sand, we get up to 70 per cent more output in a Proman machine but 15 per cent less than that in a comparable machine. This is because of the size and design of the screen and the machine.
In particular, the productivity and environment-friendliness of crushing and screening units have evolved significantly over the years. In that context, Krishnamurthy notes, The features to look out for are higher efficiency ratings, durable components, versatility and mobility. Advanced automation and control systems optimise processes and reduce human intervention, leading to higher productivity. Digitalisation and data analytics allow real-time monitoring and optimisation of processes to improve productivity and minimise wastage and the environmental impact. Advances in material handling equipment and conveyors have improved the efficiency and environmental impact of the process and reduced manual labour and risk of spills or material loss.
Environment-friendly crushing and screening units feature efficient diesel engines with cleaner technologies to reduce the consumption of fuel and minimise air pollution, he continues. Also, engineering and design improvements address noise pollution while innovative dust control and suppression systems reduce airborne particulate matter. A growing focus on sustainability has led to the development of crushing and screening units designed for recycling and reusing materials. Stringent environmental regulations have pushed manufacturers to design units that meet or exceed emission and safety standards.
The recent addition of Telematics powerscreen pulse to Terex Powerscreen track crushers and screening plants has been wonderful because we can monitor our plants from our office, says Pralhad Deshmukh, Managing Director, PD Infraprojects, a leading NHAI contractor from Maharashtra. This remotely operated system allows us to know the current location, crusher hours, engine hours, closed side settings (CSS) settings, wear, etc. It reduces dependency on manpower to that extent. We can also plan the wear parts. Site productivity majorly increases.
Newer cone and jaw designs and VSI designs deliver higher productivity for a lower motor rating, adds Jain. We have machines with a 150 hp per hour motor rating that deliver 30 per cent more output than machines with a 200 hp per hour motor rating.
Screen updates
Screening and grading technology has seen subtle changes that are producing lasting impact, according to Shetty. Design for improved performance, reduced cost, improved durability and better safety is of significance. Previously, the tendency was to build the machine safe and heavy. Optimisation efforts werent based on deeper insights and could lead to costly experiments and poor deliveries. In recent years, the availability of multi-physics tools that allow designers to model parameters such as type screen, frequency of vibrations and the G force to be employed has greatly improved designs. Simulation tools strengthen the designers ability to put both the design and equipment to test, in a virtual but a highly reliable environment. Further, the integration of design and manufacturing is now being tackled with advancements in the CAD-CAM space.
Astec-TelSmiths newer products feature advanced automation and controls enabling real-time monitoring and optimisation of equipment, leading to increased productivity and efficiency. Recent innovations have enabled Astec-Telsmith high-frequency screens to operate at less than 60 per cent of the power consumption of traditional systems.