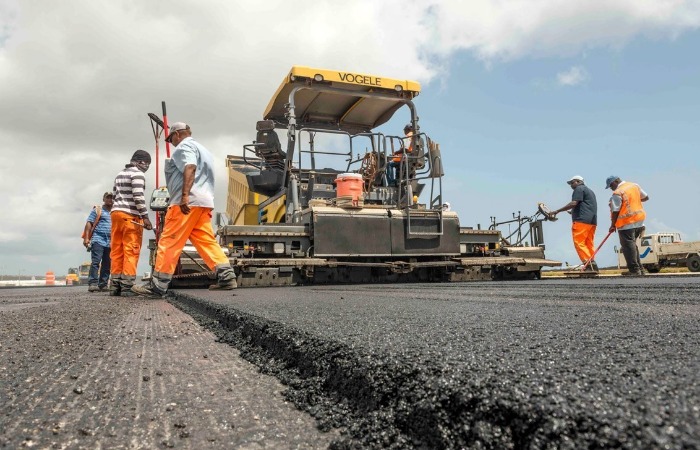
The New Concrete Frontier
In the past decade, concrete equipment manufacturers have worked hard to bring awareness among builders and contractors that how advanced technologies features, and control systems help in producing high-quality, homogeneous concrete and deliver it to greater heights and distances quickly.
Awareness among the contractors is changing the trends of the cheapest plant instead they are asking value for money, which is making/forcing equipment manufacturers to put in extra effort in their R&D cells and offer better quality equipment. Moreover, the manufacturers have to come up with innovative after-sales/market solutions and have to work like a partner in the project.
Moving towards higher-capacity concrete equipment typically involves advancements in technology and engineering to enhance the efficiency, productivity, and capabilities of concrete production and placement. Advanced batching and mixing systems allow for precise control of the concrete mix, ensuring consistent quality and reducing waste. Automated systems with increased capacity can handle larger volumes of raw materials, resulting in higher production rates. Equipment manufacturers are constantly improving the efficiency of concrete machinery, such as mixers, pumps, and batching plants. This includes energy-saving features, optimised component designs, and advanced control systems to minimise downtime and maximise output.
Mobile concrete plants equipped with high-capacity mixing units enable on-site production of large quantities of concrete. These units can be transported to construction sites, providing flexibility and reducing transportation costs. Similarly, concrete pumps and placing booms have evolved to handle higher volumes and reach greater distances. Modern pumping systems can deliver concrete vertically and horizontally, enabling efficient placement in tall buildings or large-scale infrastructure projects.
Automation: Leading the way
Automation technologies, such as robotic arms and conveyor systems, streamline concrete production and placement processes systems can handle larger volumes of materials with precision, speed, and reduced labour requirements. The integration of digital technologies and data analytics in concrete equipment allows for real-time monitoring, remote operation, and predictive maintenance.
Said Anand Sundaresan, Managing Director, Ammann India, The concrete equipment industry has become very dynamic in the last few years. Besides technological advancement, demand for sustainable solutions, digitalisation, customisation and versatility due to changes in the requirement of the concrete itself like high strength concrete calling for special mix design, demand for coloured concrete, use of additives, etc. demand for necessary changes and adaptation in the concrete production, transportation or placement equipment.
Ammann India, the brand owner of ELBA Germany, is known for its innovation and customer-centric development. We invest heavily in R&D to develop technologically-advanced products as our products are exported from India to the most developed European countries, complying with all the Euro norms. Our equipment is energy efficient, low polluting, and aligns with Indias sustainability goals. Ammanns computer control system provides remote monitoring and predictive maintenance thus enhancing the performance of the product and the customer experience. We also provide a comprehensive training programme and efficient after-sales support to ensure the equipment operates optimally throughout its life span, said Sundaresan.
He added, In the R&D department at Ammann ELBA, we continuously work on developing new technologies and solutions to enhance productivity, safety, sustainability, performance improvement and reduction of operating costs. This comes out of a customer-centric approach. We are engaged in continuous dialogue with the customers to understand their requirements and opportunities. Our company is focused on digital transformation through the Ammann ELBA AS1 control system for better project coordination, implementing automation in processes and utilising data analytics for predictive maintenance.
Said a spokesperson from Husqvarna India Products, There definitely needs to be a forum wherein all the manufacturers within the industry can come forward and take the initiative to educate their customers on new technologies and automation that they provide. If the customers are made to understand the benefit of using quality products and solutions then there will definitely be an upgrade towards how the customers get their job done. So, seminars, technical meet-ups, and industry associations would be a way forward in this endeavour. Huqsvarna offers the broadest range of products under the concrete placement range. It offers concrete vibrators, screeds and trowels.
Ramesh Babbar, President and Director, Columbia Machine Engineering, said Last two years, have inadvertently forced every small and big company to adopt digitalisation in a big way. Columbia has introduced IOT to reach out to our existing customers to understand their requirements for moulds, spares, service, etc., and also to get an update on the machine output, and products manufactured on Columbia machines. In addition to this, we have introduced various digital platforms to reach out to prospects and potential buyers.
Columbia offers concrete block machinery model SPM20+ for tall and low-height products. This machine of the same pallet size of SPM20, 508 X 508 X 6 mm can manufacture products as low as 25 mm in height and tall height products like bricks, blocks, and kerbstones of height 250 mm. We have developed this model to enable our customers to meet the product requirements of their end users, adds Babbar.
Recently, a manufacturer of concrete equipment, Ajax Engineering announced a Rs 100 crore investment to build its fifth manufacturing plant in Bengaluru with plans for a portion of the facility to be operational by the end of the year. Shubhabrata Saha, the organization's newly appointed MD and CEO, has stated that the companys sales target for 2026 is Rs 30,000 million. We anticipate having a revenue turnover of roughly $10 billion at the end of FY23. Our primary local and export companies will be responsible for the scaling of revenues.
The company hopes to grow in these markets because it believes its goods are ideally suited to cover regions including Middle East, Africa and South and Southeast Asia.
The size of the Indian market for concrete equipment is between 50000 and 60000 million. We think that the infrastructure story will be extremely important if the nation intends to grow its economy significantly over the next 20 years. We are optimistic that we will meet our sales objective in this scenario because the size of this market could increase to Rs 80,000 million in a few years, according to Saha.
Said Kalpesh Soni, Vice President, KYB-Conmat, India's market for construction equipment, concrete construction equipment is experiencing growth due to increased government investment in infrastructure development. KYB Conmat holds a top three position in most segments, including batching plants, paving machines, transit mixers, and self-loading mixers and is growing in concrete pump segment."
KYB-Conmat concrete mixers are IoT enabled, BS-4 and ARAI compliant, and offer better fuel efficiency, high productivity, better mix quality, faster loading and discharge due to an advance blade design and electronic batching system with printer, produce more concrete per batch by optimised drum capacity, which reduces the overall cost per cubic meter of concrete. Further, these self-loading mixers offer superior manoeuvrability by single joystick control, 4-wheel steering/4-wheel drive system, also offer superior operator comfort due to reversable operator seat and balanced load distribution on front and rear axles.
Speaking on the opportunities for concrete equipment in India, he added, As can be seen, 2023 is shaping up to be a fantastic year for construction. With technological advancements and high demand for services, the only way to go is up. With an emphasis on rebuilding infrastructure, sustainable buildings, and smart cities, construction companies that embrace the industrys changing landscape will have more opportunities. Investments in infrastructure are the main growth drivers of the industry."
Outsourcing concrete to maximise productivity
In constructing the Mumbai Metro Rail, we usually used boom placers as these are suitable for placing concrete up to the required height and radius (unlike high-rise buildings where the boom falls short) shares Pramod B Joshi, Additional General Manager (P&M Head “ All India), Ahluwalia Contracts India. We used a 36-m boom although in some instances contractors used a 43-m boom. For metro construction concrete boom placers work better than stationary concrete pumps especially when the quantity of concrete involved is limited. Boom placers are easier to use and shift to the next job.
The operators skill is the most critical factor affecting the productivity of a boom he continues. In city areas spaces are usually limited and traffic poses a concern. A skilled operator can help ensure the safety of the site and passers-by.
Productivity may also be hampered by traffic adds Joshi. The team in charge of logistics the transport of concrete and placement of the boom and getting the authoritys approvals for all this play a key role.
Deploying our own batching plant is productive when the monthly need for concrete exceeds 2000 to 2500 cum for a 30 cum/hr plant and 5000 cum for a 60 cum/hr plant he continues. Our preferred plant for a metro project is a 30 cum/hr or 60 cum/hr machine depending on the quantity of concrete needed with a twin-shaft mixer and SCADA software. We set up a site quality lab when the plant is installed by own at our site.
If the monthly need for concrete is less than 1,200 to 1,500 cum or if the site is too congested, we outsource the procurement of concrete adds Joshi. Setting up a plant requires approval from the Weights & Measures Department and pollution certification. If this process is likely to be time-consuming then again, we outsource the concrete. Quality checks on the concrete mix design are essential to ensure the quality of concrete. Monitoring productivity with quality checks is the most important factor in operating a batching plant.
For the construction of 348 residential buildings and administrative offices for the Nagpur Improvement Trust at Lakadganj Nagpur we deployed a batching plant of 60 cum/hr capacity as the daily need was upwards of 100 cum says Sachin Aware, Maintenance Head, Harsh Construction. To maximise the output of the plant we ensured a dedicated short (less than 20m) ramp to load the aggregate and put up a partition to ensure no mixing with sand. The logic was that loading aggregate is the most time-consuming of all the processes involved in making concrete. If loading is done correctly the process can be optimised. We used a stationary concrete pump to pour the concrete.
In constructing the raft foundation of a district court in Nasik we needed to pour 1,400 cum of concrete without a break, he continues. Arranging separate teams to continue the pour over successive shifts helped complete the job with a mixer and boom in about 27 hours.
In general, a batching plant will deliver 80-85 per cent of its stated capacity onsite adds Aware. We choose a plant size depending on the project needs; our plants vary from 20 cum per hour to 60 cum/hr but if you want to use a boom pump of 70-80 cum/hr even the latter size can prove small. Nine of our batching plants are from Aquarius Engineers and six concrete pumps all chosen because the brand delivers good services.
Pain points
Well-trained operators are essential to maximise productivity. Across the industry, there is recognition of the dearth of trained operators. Anil K Banchhor, Managing Director and CEO, RDC Concrete, believes vendors should play a bigger role in solving this issue as infrastructure work will continue to be in focus in the next decade.
He adds, We have so many manufacturers of construction equipment but very few are focused on training operators, he says. Most manufacturers focus on selling equipment. But for equipment to perform optimally and maximise its uptime and reduce fuel consumption, we need well-trained operators. Manufacturers should focus on training and certifying operators so that the users pain point in getting the right operator is reduced. They would find that many buyers would like to take both the machine as well as the operator and come back with repeat orders as the machine has performed well because of the trained operator. Operators should be trained in operations as well as minor maintenance and repairs. Refresher training can also be organised for operators through web meetings if the numbers are few. This approach would allow users to enjoy much higher productivity and availability of machines. At present users are fully dependent on the manufacturer for any breakdown even if its a minor one or the operator is not able to handle small issues.
After the industry migrated from the use of river sand to crushed rock sand as a fine aggregate, batching plants see more dust pollution, observes Suresh Rao Marpally, Technical Director, Starcrete LLP. If crushed rock sand is made wet or washed to control the dust, the material doesnt flow easily through the fine aggregate hoppers, and actually needs to be poked near the discharge gates to facilitate the flow. Plant manufacturers should improve plant designs to ensure that no such manual intervention is needed.
The design of batching plants should also be modified to facilitate the sampling of raw materials like cementitious materials and admixtures, a task that is essential to quality control, he continues. Also, many plant manufacturers dont provide indicators inside the operator cabin to assess the workability of concrete inside the batching plant mixer, or provide the indicator at a high price, compelling customers to add their own ampere metre, but such add-ons are of low accuracy. Monkey ladders provided in the vertical storage silos of concrete batching plants have always been risky. Instead, manufacturers should provide safer dogleg stairs or spiral ladders to reach the roof of the silo to manage/service any installed safety valves and dust collectors. Modern concrete produced for aggressive coastal environments is made of small quantities of multiple cementitious components in addition to Portland cement and fly-ash/GGBS. Plant manufacturers should introduce small quantity storage silos and weigh batches for such raw materials.
For safer batching plant operations, Marpally suggests that manufacturers should certify plant safety star ratings based on the safety features the customer opts for. Thereafter, local licensing authorities such as factory inspectors should enforce a minimum star rating to permit operations, he says. This practice would also help concrete buyers to select suppliers who adopt industry safety standard requirements.