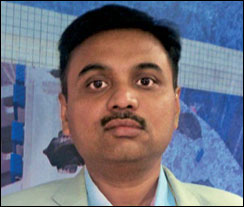
The demand for TBMs has been consistently increasing.
Could you tell us about your product line?
We design and manufacture TBMs of all sizes, ranging from 2 m to 15 m diameter and for all type of grounds, that is, for hard rocks, for soft ground, for all type of geologies, too. Along with TBMs, we also make specialised cutters in the TBMs: special alloy steel cutters and conveyor systems.
What is the application of conveyor systems?
Conveyor systems are used to remove mud or rocks that come out of the tunnel while boring it. There are ways to take the mud out, either by the help of rolling stocks, by mud carts, or with a conveyor. The conveyor is a continuous process, you bore and the mud is continuously pumped out with the conveyor, so it is very efficient and saves time. We make all type of conveyors; the conveyor which is used in the tunnel is the tunnel conveyor. We have small-sized conveyors which are on the TBM and for the EPB machines, we have screw conveyors. Particularly in jobs in Mumbai the machines are operating 109 m below the ground, first of all to take the mud from the face to the shaft and then from the shaft to the top. So, mud from as much as 110 m height is taken out by the vertical conveyor and from the vertical conveyor, it is transferred to the stacker and then stacked outside.
What is the demand for this product in India?
When Robbins started in India around seven years ago, mechanised tunnelling was new to the country. There were hardly 1-2 TBMs used earlier. Since we started, Delhi Metro also began and people came to know about this technology and about TBMs. Since then, the demand has grown tremendously and we have seen that there is a continuous increase in demand, about 20-30 per cent increase per year. In the first projects of the Delhi Metro, they used only two TBMs, whereas in Phase 3, there are around 25 machines boring together. After the Delhi Metro, there are other cities which are going to start similar projects. The next in the pipeline is Mumbai, which has a very hard rock area, and we expect 70 km of tunnelling, about 35 times. Around 20 TBMs will be required for Mumbai.
What is the capacity of these machines?
We are doing an average of 300 m a month minimum; whatever be the geology, it is capable to bore more than 300 m. We had months when we have bored 500 m also. But in October, the Robbins machine in Mumbai did an Indian record of 870 m in a month. The machines are very strong and robust; they are capable of going at very high rates, provided the supporting structures or arrangements are behind it. If you have bigger size tunnels coming up in the Himalayas or other places, the conventional method is now increasingly being replaced by mechanised tunnelling.
What size of machines is used for the projects in Mumbai?
There are all sizes. For Mumbai, for water tunnels, the main water transfer tunnel from the lake would be around 6 m diameter finished, for the metro sites, it is 6.6 m diameter and the finished internal diameter would be around 5.8 m. It is done by TBMs because you cannot blast in the city, even controlled blasting is not allowed. You cannot blast within these structures, and you have no option so it is the best way out. It is pretty fast as well.
What are the opportunities for TBMs in the current market?
The demand has been increasing consistently for the last two years but it is still not what we expected. The overall delay in approvals from the government has been a bad hit. There are a number of projects which have been delayed due to non-approval but we foresee that everything should come on track by the middle of next year, after the elections are over. What we have seen is that even the Metro?s jobs have been delayed. There are a couple of projects like Mumbai that we hope will come up very soon, by the first quarter of next year. But other Metro projects in Ahmedabad, Pune, Ludhiana, Lucknow, etc, are expected by the end of 2014 or in 2015.
Are these machines imported?
As Robbins is a US-based company, we pioneered this technology 60 years ago and we have a complete design department and a production unit for it, back in the US. The majority of the components are being designed and made in the US and Europe; it is then further assembled and tested and then the machine comes in a knockdown condition to India. We are using our China facility just for the assembly.
We have two plants in China but the components and the entire machine is from the US, partial components are from Europe as well. We then assemble them in China, sometimes in the US, too. We are looking at the possibility of making some of those machine parts here in India as well and for a couple of machines which are being used here in India, we have tried and made some components, and they are working fine.
Will indigenisation make a difference as far as cost is concerned?
One problem which I face here is that even if we start making the majority of the parts in India, there are tax issues. If we import any of the TBMs, it is one hundred per cent duty-free. Initially it was mega hydro projects for which TBMs were exempted. Later it was relaxed for the water irrigation tunnels, and then for road tunnels. For the last one-and-a-half years, they exempted the TBMs for any use, whether it is for sewage, metros, hydro, roads. If I make the machine here in India and supply it to my customer, I have to pay excise duty as well as VAT which is extra cost not comparable to the import expense.
Practically, it is not justified to to make it here in India where material and labour are separate, making the tax structure skewed. If I import the product from the US, it costs me no tax but if I make the same in India, I incur at least 20 per cent in duties and taxes. However, in the future, we are trying to indigenise some of the components which is not critical for the machines and subsequently we have a plan to start some of the units also.
How do TBMs add to the project cost?
If you compare the capital costs of the equipment along with comparison to a TBM, yes, it is expensive. But you need to see the overall economic situation of the project liability, when it is still dependant on the length of the tunnel and the size of the tunnel. If you have any tunnel which is substantially longer than 3 km and has diameter of 3.5 m and above, it is always an advantage or economical to use a TBM, because with a TBM, you have a production rate which is 3-4 times higher; you don?t need to add the additional cost of the ventilation. So it is faster, cleaner; you launch the machine from one side and it comes out on the other side.
How is the competition on the ground?
As far as TBM manufacturing is concerned, there is nobody who has started production here in India. There is one company from Germany which has its plant and factory in India but that is only used for assembly and refurbishing. The company gets all the parts from abroad. Robbins is the pioneers in designing these machines worldwide. Sixty years ago, we developed the first rock machines, first double-sheet machines, first 19-inch disc cutters, and the first floating grippers. Robbins holds 90 per cent of world records for rock machines.
How many Robbins premiums are in operation in India?
At the moment, we have seven to eight machines in operation, out of which four machines are 10 m in diameter.
What about after sales service?
We have about 200 Indian technicians who are engineers and technical experts. We also have around 30-35 foreign experts.
Do you provide training to the operators?
Yes, in fact more than a supplier, we act as partner to the customers. What we do is, after commissioning the machine; we give them the experts from our team, first to operate and then for the training. We train the full crew of our customers.
Initially when we start a project, the strength of our people is more but we keep training those people, first at our manufacturing places, then when we are assembling the machines and third when we start operating those machines. Then they take over from us and we start gradually decreasing our people and handing over the job to them. There are a number of projects where we started with more than 10-12 expatriates with 20 Indians and now this expat strength is down to two or three people.
If you have any tunnel which is substantially longer than 3 km and has a diameter of 3.5 m and above, it is always an advantage or economical to use a TBM.