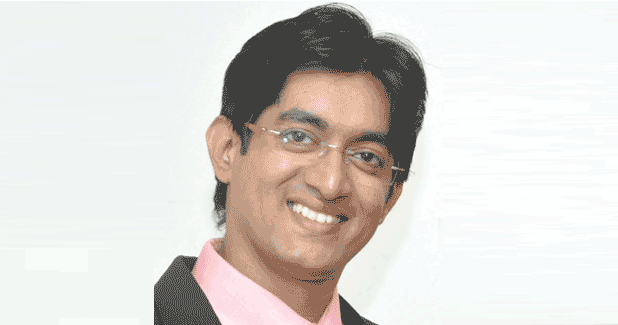
The level of automation in CE has skyrocketed
B&R's modular X90 control and I/O system brings all the functionality of advanced automation solution to construction equipment. <span style="font-weight: bold;">Saurabh Kulkarni, Mobile Automation Expert, India, B&R Industrial Automation,</span> shares more on the importance of automation in construction equipment. <p></p><p> <span style="font-weight: bold;">What are the advanced automation solutions from B&R for motor graders and other construction equipment?</span><br />With development for roadways in urban and rural sectors increasingly tremendously, the need for technology-intensive construction equipment (CE) is on the rise.</p><p> Levelling of ground is essential for road constructions with motor graders playing a vital role in increasing efficiency and reducing tedious labour. B&R's modular X90 control and I/O system brings all the functionality of advanced automation solution to construction equipment, providing precise and accurate slope and height control from the control area. Deployment of B&R control and software platform guarantees ease of machine operation, higher efficiency and productivity. All products belong to X90 family can handle operating temperatures from -40 to +85¦C (housing surface) and are resistant to vibration, shock up to 50 g, salt, UV light and oil. These systems are coupled with condition monitoring functions allowing predictive maintenance functionality to motor graders. Together with condition monitoring, OEMs can increase machine availability, further reducing the considerable cost of outages and unplanned service calls in motor graders. In addition, data recording and seamless connectivity to the cloud are more features being provided by our powerful X90 platform. </p><p> <span style="font-weight: bold;">What are the safety solutions offered by B&R in motor graders?</span><br />It is essential to ensure safety of the operator, people around as well as the construction equipment. Safe automation plays a crucial role in satisfying the necessary safety requirements demanded by OEMs. Over the years, the level of automation being deployed in construction equipment has skyrocketed. One of the many examples of automated processes is drive-by-wire systems, which transmit information from the gas pedal electrically rather than mechanically. These systems offer many advantages, but are not without risk, even a minute malfunction while driving could cause a serious accident. Safety technology is therefore critical for the drive system. The Machinery Directive (it addresses manufacturers, importers, and dealers of machinery and safety components and applies to new equipment.) requires manufacturers to carry out a hazard analysis and risk assessment using a risk graph in order to determine the necessary level for the safety function. The mobile machinery must generally achieve safety integrity level SIL 2 and performance level PL c. However, achieving these safety levels is no problem using programmable safety technology. For a wide variety of safety functions, T_V certified software blocks are available. The task of safety programming itself is thus reduced to simple configuration and linking of the safe software blocks. The machine manufacturer then only has to prove to T_V that this work has been carried out in accordance with the guidelines for safe development. This drastically reduces complexity, workload and certification time. The hardware to go with B&R's programmable safety technology is the X90 safety control and I/O system. B&R has added an easy-to-implement safety solution to its portfolio for mobile equipment. </p><p>At bauma 2019 in Munich, Germany, from April 8-14, we are presenting our first X90 controller with integrated safety technology. A new option board can expand any X90 controller to include a full-fledged safety controller. OEMs are helped with mapp technology even for creating the corresponding safety application enabling them to configure more and program less. This brings all the advantages of networked safety technology without any traditional programming and makes it substantially easier to achieve compliance with the European Machinery Directive. As a technology partner, B&R goes to great lengths to ensure that its platforms are future proof. If the safety requirements increase to SIL 3 or PL e, for example, there would be no need to redesign the hardware. Our controller is already designed to support PL e. </p><p> <span style="font-weight: bold;">What are the maintenance-related solutions from B&R for motor graders?</span><br />OEMs moved from reactive maintenance to preventive and today they are considering predictive maintenance. Condition-based predictive maintenance maximises machine availability and save the considerable cost of outages and unplanned service calls. It also helps them monitor the health of the equipment 24/7 and enables them to utilise the maximum life cycle of a device in the equipment. Our modular X90 control and I/O system is equipped with condition monitoring functions, which helps to detect problems in their early stages and reduce unplanned downtime. The X90 module allows operators to continuously monitor the status of mobile equipment such as motor graders. The analytics help determine exactly which components require maintenance and when. Typical applications include continuous monitoring of rotating machine components such as hydraulic assemblies, belts, gears and motors. </p><p> <span style="font-weight: bold;">How do you look at the trend in adoption of automation and digital features in motor graders?</span><br />Technological advancement is not the choice but need of every sector. The construction industry has witnessed several technology trends that improve product quality, while reducing waste, decreasing labour costs, and expanding production flexibility. In order to improve performance of motor graders, OEMs have implemented machine control technology, which improves equipment efficiency. Digitising assets further enables OEMs to monitor equipment 24/7 and gain deeper insights into the equipment operation. This also might result in enhanced business models and protect OEMs against unwarranted warranty claims. OEMs can take B&R's advantage of over 35 years of expertise in control technology. OEMs can also benefit from the extensive diagnostics and simulation options that are implemented directly in the system. </p>