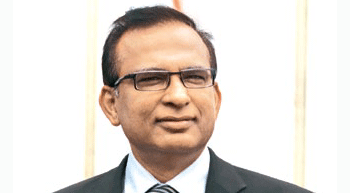
We are working closely with institutions
Excerpts from the interview
What are the solutions offered by Wirtgen in milling and recycling?
For milling and recycling, we have a wider range of equipment. Wirtgen has been pioneer in this field, not only in technology but also in market share. Last year, we have introduced new sets of cold recyclers which are already operating in India.
We have introduced new mixing plant KMA 220 and GR Infra Projects purchased the first new generation machine which will be operational in this January. So we have a complete range of machines and we are trying to promote the select models which are suitable for India. We also offer machines to customers on short term rental basis so that they can use the machine and get a feel of it.
What are the technology trends in the equipment and machinery in this area?
Technology trend is towards getting more production, less fuel consumption, and a lot of innovations on the products. We have come out with many innovations on our products of WR 240 and KMA 220 like camera system for the operator to see the RAP while milling. Even in recycling, there are many new technologies coming in with the new range of machines.
Is cost a deterrent?
These machines are high-tech machines so more capex is required. This is why we were initially offering these machines on rental basis. It is a matter of time before the market picks up. I don?t think capex is a big issue once the awareness face is clear. We have seen the same happening in China in a big way where we supply almost 50 recyclers a year.
Some contractors cite the lack of availability of quality RAP as reason for not using RAP in road projects? What is your take on this?
Once we identify a project, where RAP is available, we need to test the samples of this RAP. For this purpose, we have supplied labs to the institutions like CRRI and the IITs in Kharagpur and Chennai. The RAP sample needs to be tested in the labs accordingly and ensure whether it can be used in WMM or the top layer.
WR 240
With the world?s largest line of recyclers and soil stabilisers, Wirtgen has the right solution for every application. The WR 240 is considered to be an all-rounder for the heavy-duty stabilisation of large areas of non-cohesive soil, and for the conservative cold recycling of damaged asphalt layers. A variety of new features make it a pioneer in terms of performance and cost-efficiency, and it has impressively demonstrated both of these in practical use in recent months, as the exclusively positive feedback from customers confirms. Despite its higher productivity, the WR 240 consumes significantly less fuel thanks to state-of-the-art engine management, and therefore considerably reduces costs for contractors. What is more, their machine operators praise the large, modern cabin, the all-around view it affords, the machine?s iF product design award in gold for the Wirtgen WR 240. In addition to their innovative features, all three models lastly win out with their ultra-modern design. The WR 240 even won the iF product design award in 2013 in gold, one of the world?s foremost design prices.