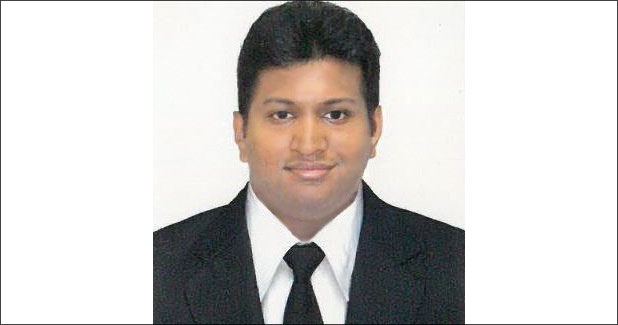
We expect our business in India to double by 2020
What is the importance of filters in an equipment?
Fuel contamination, either in the form of dirt or water, will find its way into your fuel system, however careful you are. With modern engines now injecting fuel at pressures up to 30,000 psi, and injector tolerance being measured in microns, even a small amount of dirt or water corrosion can create problems. Water or particulates can cause microscopic surface damage that is then focused on by the high-pressure fuel flow, which causes wear that will eventually lead to reduced efficiency and complete breakdown. With this in mind, managing fuel delivery and system cleanliness through proper filtration becomes an absolute imperative for economical engine operation. A filter helps maintain the engine and equipment life by removing the smallest of dirt particles which could lead to defuncting of fuel injection systems and other critical components. Filtration systems having water separation capabilities also help in separating water and other contaminants that could lead to corrosion in the equipment.
How does a filter help in the fuel efficiency and productivity of an equipment?
Firstly, there is a false myth amongst general users that dirty or partially clogged fuel filter would allow less fuel into the engine and the engine would run leaner, hence would result in better fuel efficiency. This is completely not true, as ECU usually raises the fuel pressure to compensate using various sensors to direct the injector to open longer and in result dump excess fuel out. The air filter is also important to the efficiency of the engine because of the need for air. The engine of an automobile requires a flow of fresh air coming into the system. What happens is that the air will mix with the gasoline to create the energy spark that puts the wheels in motion. The right amount of air mixed with the gasoline improves performance considerably. Air filters make certain that the intake of fresh air does not contain any debris. This includes dust, pollutants, and other particles that can cause problems within the engine. Clean air mixes well with the gasoline and generates a higher kmpl. As the air filter becomes increasingly more clogged by use, it begins to obstruct air going into the engine. To compensate for the decreased amount of air, the engine must work harder and will consequently expend more gasoline. This results in lower kmpl and higher costs at the fuel pump. The economy realised by a clean air filter and fuel filter are reasons enough to periodically change it.
What are the emerging technology trends in design and development of filters? What are the major factors that are taken care of while designing a filter?
The future of the diesel engine relies on increasingly stringent exhaust emission requirements, while the quality of diesel fuel continues on a worldwide decline. New diesel engines require extraordinary fuel cleanliness and freedom from water contamination to meet these requirements. Ultra-low sulphur diesel (ULSD) and the rapidly expanding use of biodiesel pose new filtration challenges due to their tendency to dissolve existing deposits, absorb water, and support the growth of bacteria. Even cold weather operation is compromised by the new fuels, leading to downtime and problems on an increasing frequency. With India moving to BS-VI norms, will lead to improvements in fuel injection timing and addition of a gasoline particle filter for gasoline direct injection (GDI) engines. The change in norms will also lead to control of crankcase emission norms leading to closing crankcase ventilation systems and routing of gases into air intake systems. A major shift amongst Indian customers has been towards longer life filters that would reduce in service intervals and auto drain solutions.
Major factors considered while designing a filter are engine capacity, flow rates, service interval requirements, ease of maintenance and cost restrictions.
With over 100 active patents, 45 years of media development, and a range of proprietary technologies, Parker Hannifin is 100 per cent focused on developing filtration that enables our customers to meet the challenges of tomorrow. Parker India has immense experience in serving its global customers with Euro-VI filtration products. We have a strong engineering base in India which has enabled us to support our customers with solutions for longer life and cost-effective solutions during the life cycle of the equipment. The heart of these advances is in Parker's proprietary engineered filter media families. Our selection of Aquabloc II? media is known worldwide for its combination of high efficiency, long life and unsurpassed water removal performance, meeting and exceeding the challenges of today's diesel engine requirements in all markets and environments.
What is the range of products and solutions you offer to various equipment?
Parker has an extensive range of filtration solutions for its customers. We have local capabilities for fuel filtration, oil filtration, air intake systems, hydraulic filtration, crankcase ventilation systems, pump filtration solutions etc. We have also invested in India for the future growth in the aviation market and have manufacturing capabilities for aviation fuel filtration with support from Parker Velcon USA. These products follow stringent norms and require certifications from global certification body for aviation industry EI (Energy Institute).
With one eye towards the future, Parker Filtration recently completed the acquisition of Clarcor Inc., a major manufacturer of filtration products, for approximately $4.3 billion in cash, making the combined entity the largest diversified filtration solutions provider in the world. It is hugely relevant for Parker India as Clarcor has an existing presence in India and with their incomparable global experience in aftermarket and extensive range of Baldwin filters we are equipped and ready to grow rapidly our off-highway offerings for aftermarket requirements in India.
Both Parker and Clarcor have a diversified range of products serving diverse industries. We have strong presence in the compressed air, industrial air, gas generation, water filtration, process filtration and bulk fuel filtration.
What are the major differences between filtration solutions offered for equipment operating in various geological, climatic and environmental conditions in India?
Each climatic and environmental condition has its own challenges and requirements, which defines the designing of a filter and results in cost implications. For eg., in a cold environment, all fuel filters require a heating mechanism to ensure that the fuel remains in a liquid state and not solidifies, resulting in complete system failure. Some geographical locations like deserts require special protection in your air intake systems as the flow of dust into the system is much higher than in normal conditions. To tackle such situations, it becomes imperative for customers to work with quality solution providers like Parker who have knowledge and experience in handling such varied critical requirements.
What are the developments to meet the latest emission norms?
As mentioned earlier, with stringent norms, the focus will be on achieving minimal emissions.
The development in filtration would include gasoline particle filters, Urea filters, crankcase ventilation systems among others. These changes would also result in a huge shift towards adopting CNG systems in larger engines and commercial vehicles.
Parker India has been serving our customers globally for their Euro-VI requirements and hence are prepared to adapt to the necessary changes. We have in our standard range of filters globally, a diverse array of options for Euro-VI norms and also for CNG systems.
What is the demand for filters from OEMs and aftermarket consumption?
We have seen a constant growth from our OEM customers over the past couple of years, even though there is a temporary impact due to demonetisation and now with GST implementation, we have a strong outlook for growth in the coming year. Our presence in the aftermarket is small and we are creating our roadmap to grow in the future with the recent acquisition of Clarcor which owns the Baldwin brand.
What is the customer approach towards filtration solution for construction and mining machinery?
With respect to construction and mining machinery, the requirements of the OEM and end customers are not heavily focused on low cost options. Cost might be one of the factors but more focus is given towards ensuring equipment safety, minimum downtimes, longer maintenance intervals, quick changeovers etc. This brings in a quality perspective in the solutions being derived for filtration systems. We see this trend also coming into commercial vehicles space with the rapidly changing and more stringent norms coming into play.
Parker has always been a pioneer and promoter of quality solutions across the globe and in India. With our extensive range of filtration solutions and proprietary patents on media of over 100 active across different categories, we are best suited to serve our customers and drive their future growth requirements.
What is the current market trend for filters? What are the growth prospects?
With the current government's focus on infrastructure development and growth, we see heavy investments flowing into the construction space. The demand for construction equipment and commercial vehicles are on a high and we expect this growth to continue this coming year. Also, with the controlled opening of the mining industry, we see a growth in mining equipment as well going forward.
For Parker, we consider ourselves still comparatively new in India and hence are very bullish about our growth prospects in the country. We expect our business in India to grow double by 2020 and become one of our bigger contributors for Parker in Asia-Pacific region.