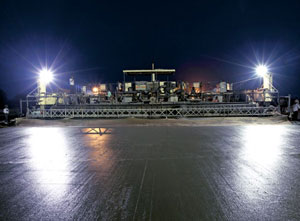
Yamuna Expressway
The Yamuna Expressway not only cuts travel time between Delhi and Agra by more than half but also drives the development of industry and tourism, the two major backbones of the Indian economy in the region. The new expressway will in future provide direct access to the Yamuna Economic Zone and the international airport. Jaypee Infratech was the contractor in charge of building the 165-km long, six-lane Yamuna Expressway between Noida and Agra. The project was estimated to be completed within seven years. In addition to the option of extending the road to a total of eight lanes, the project scope also included the construction of several interchanges, underpasses, toll stations as well as minor and major bridge structures. In view of excellent past experience, Jaypee Infratech relied on the skills of the proven construction machines from Wirtgen also for this megaproject. The fleet of Wirtgen machines played a vital role in completing the Yamuna Expressway after a construction time of only five years, enabling it to be opened to traffic two years earlier than the originally scheduled completion date.
Wirtgen paver quartet
The Yamuna Expressway project devoured nearly 1.7 million cu m of concrete, just the right challenge for the four SP 1600 slipform pavers from Wirtgen. Working at a paving width of 15.7 m and paving thickness of 320 mm, they completed the 165-km long section between Agra and Noida in a single pass for each direction of travel. The huge job could be completed in such a short period of time only because the Wirtgen paver quartet performed efficiently, accurately and with maximum precision. Additional factors of success were the perfectly well-coordinated operator teams and highly efficient logistics system. The specified camber of % was simply adjusted via hydraulic cylinders. In a first step, the spreading plough distributed the previously delivered concrete evenly across the full paving width. The mould of the SP 1600 then slipformed the new pavement slab.
Perfect insertion of dowel bars
As many as 45 electric internal vibrators installed in the paving mould used high-frequency vibration to compact the concrete by expelling the air entrapped in the material. The dowel bar inserter installed in the SP 1600 then inserted a large number of dowels into the freshly paved concrete automatically by means of an additional 32 electric high-frequency external vibrators: 63 dowel bars each, measuring 500 mm in length and 36 mm in diameter, were inserted at 5-m intervals, without the SP 1600 having to interrupt its forward movement. In between, three tie bar inserters inserted tie bars transverse to the pavement: 11 longitudinal tie bars each, measuring 640 mm in length and 16 mm in diameter, were placed at intervals of 530 mm. Insertion of the dowel bars and tie bars was monitored in an automatic process. Details of the dowel bar and tie bar insertion process and other machine parameters were provided to the operator on a separate LC display. The precisely inserted dowel bars and tie bars offer superior strength to withstand the high loads that the road will be exposed to in the future. In a final step the heavy-duty finishing beam and super smoother of high-quality material moved across the concrete surface in an oscillating movement to ensure perfect evenness.
TCM 1800 ensures premium-quality finish
During the concrete paving process, each of the four SP 1600 slipform pavers was followed, at a short distance, by a TCM 1800 texture curing machine. Each of the four self-propelled TCM 1800 machines was equipped with a spraying system and a broom which were guided across the entire width of the pavement automatically in a transverse movement by means of a carriage. The broom was applied on the slab in a transverse movement to give the concrete surface the specific surface texture and grip. For the Yamuna Expressway, the client had specified 3 mm deep grooves at a spacing of 20 mm no problem at all for the TCM 1800. At the same time, the spraying system sprayed a liquid concrete curing compound on the freshly paved concrete surface. The 320 mm high sides of the concrete slab were moistened by means of two separate spray nozzles. The application of a curing compound protected the concrete surface against premature and irregular drying, thus preventing stresses from occurring in the concrete structure that could have led to cracking.
SP 150 - the versatile small paver
Jaypee Infratech decided in favour of German technology to also produce the specified safety barriers. Four S 150 slipform pavers from Wirtgen were used to complete this job. Changing the mould from one machine side to the other in a few quick steps is a major advantage of the SP 150. It can even be done on the job site and significantly reduces setup times. Pivoting legs and the horizontally telescoping rear track unit enable the slipform paver to be fully adjusted to the paving situation on site. Handling of the SP 150 can also be learned in next to no time: after only one day, customers are usually able to operate the slipform paver all on their own. Reinforcing wire meshes customized to the shape of the profile to be built had been laid by Jaypee Infratech?s site staff during preparation of the base.
At the same time, stringlines had been installed next to the course of the profile, which were continuously scanned by sensors fitted to the S 150 paver to guarantee accurate paving of the profile at all times The reliable, versatile three-tracked machine then paved different types of kerbs, concrete safety barriers measuring 850 mm and 1,100 mm in height, as well as rainwater gutters of different sizes along the 165-km long motorway. Machine productivity was enhanced significantly due to the fact that the paving moulds could be fitted on the left or right side of the SP 150 to adapt to the paving situation on site.
Wirtgen Group service
Time and again, high machine availability is of the essence in ventures as large as the Yamuna Expressway project. It goes without saying that the Wirtgen Group?s global customer service followed this maxim in India, too. Being the sales and service company in charge, Wirtgen India had already gained extensive experience in similar projects, such as construction of the Bombay-Pune Expressway. As a result, Wirtgen India?s service team was all set for ensuring that the machines involved in the construction of the Yamuna Expressway were fully geared to maximum operational availability.
Wirtgen India put together a service package that was specially tailored to vehicles equipped with special tools; high-quality measuring equipment and a variety of spare parts were always on stand-by. And as the concrete paving operation continued around the clock, the experts from Wirtgen Bangalore and Wirtgen Delhi were available to support the client 24 hours a day and seven days a week.
PROJECT DETAILS
Construction time: 5 years.
Paving length (concrete): 165.537 km.
Paving width (concrete) in each direction: 15.7 m.
Paving thickness (concrete): 320 mm.
Paving thickness (hydraulically bound base): 150 mm.
Concrete used: 1.7 million cu m.
Concrete aggregates used: 13.5 million tonne.
Steel reinforcement used: 140,000 tonne.