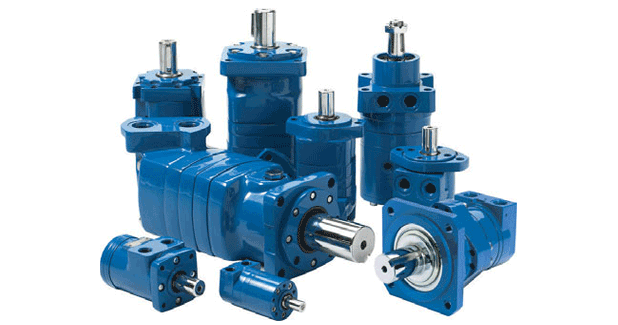
Meeting intelligence and power
Going forward, the focus of hydraulics is expected to be a combination of hydraulics and electronics that will deliver smarter products with a mix of the intelligence of electronics and the power density of hydraulics.<p></p><p> Hydraulics plays a vital role in mobile/construction equipment. Heavy equipment such as construction and mining equipment bank on hydraulic power to perform their tasks, mostly in harsh and severe conditions. A good hydraulic system will allow all the heavy equipment parts to operate efficiently and help accomplish any task required. </p><p>Major heavy equipment parts used in a hydraulic system include hydraulic motors; hydraulic cylinders; cylinder barrels, heads and pistons; gear pumps; hydraulic hoses; and hydraulic filters.</p><p>Hydraulic cylinders are responsible for providing the pushing/pulling forces in a hydraulic system. The simplest systems can use cylinders in presses, but even the simplest hydraulic systems can have cylinders responsible for a large amount of force.</p><p>Cylinder barrels, heads, and pistons go into the cylinder system and work together to create pressure zones. The barrel holds the cylinder pressure, the head encloses the pressure chamber, and the piston is responsible for separating pressure zones. Gear pumps are being used by many hydraulic systems. These allow the system to run smoothly, and they can handle pressures up to 250 bar. </p><p>Hydraulic hoses are some of the most commonly used hydraulic part in hydraulic machinery. These hoses are designed to fit the needs of a variety of systems. Hydraulic filters are important to make sure that any heavy equipment hydraulic cylinders and systems used are kept as clean as possible. These hydraulic components are one of the most effective ways of reducing contamination.</p><p> <span style="font-weight: bold;">Hydraulic motors</span><br />Normally hydraulic motors are used for machines requiring high torque and working in difficult environment. Hydraulic motors are also fitted on other applications where it is required a significant torque. Standard motor is a modular system that can fit for different applications, but at the same time, there are several specific motors for selected applications like compactions, skid steer, excavators, etc.</p><p> <span style="font-weight: bold;">Hose and fittings</span><br />Hydraulic systems are widely used in off-highway (mobile) equipment when heavy force or torque is involved, such as lifting loads weighing several tons, crushing or pressing strong materials like rock and solid metal, and digging, lifting, and moving large amounts of earth. Hose fittings have an impact on the overall efficiency and safety of a hydraulic system. Non-skive hose assemblies; improved cleanliness level and complete kit solution (hose, fittings, adapters and tube fittings) prevents premature hose failure which in turns improves the efficiency. Compact hose and improved fitting design reduces weight of the system which helps to improve the performance of the machine. Hydraulic hoses bring about the flexibility needed for the operations of the various actuators in these equipment. Hoses also help in absorbing the high vibrations these machines are subjected to where rigid pipes or tubes will invariably fail. A hydraulic hose meets all these application requirements while serving the basic purpose of conveying pressurized fluid between various components within a hydraulic system.</p><p>According to the specifications stated by the Society of Automotive Engineers (SAE), the shelf life of a bulk rubber hose is 10 years from the date of manufacture and is considered unlimited for thermoplastic hose, if stored in subdued light and controlled temperatures with no fittings attached. But in use, so many variables come into play that it is impossible to exactly predict the service life of a hose assembly. However, understanding important operating parameters that affect a hose, combined with a bit of experience, can help guide users as to when an assembly should be replaced. The average life of a hose depends on its manufacturing process as well as its design i.e. tube and cover material, reinforcement, fitting integrity and accuracy etc. In addition, some important factors that impact the life of a hose are operating pressure and temperature, routing, pressure surges, ambient temperature, bend radius and fittings. It is very important to monitor hose assemblies and carrying out preventive maintenance as it is critical to ensure safe and productive operation of hydraulic systems and also enhance the life of the hose.</p><p> Hydraulic filters<br />Hydraulic filters are used in the torque converter, transmission, steering and hydraulic systems of most machines. These systems have both high pressure and high temperatures. Hydraulic filters act to remove small particles caused by wear and tear in sliding components and plate lining. The wrong filter with a weak centre core can cause a filter to collapse and spread contamination throughout the system. Filters are designed to handle temperature and pressure variations within the hydraulic systems. </p><p>The industry mostly uses two types of filters, a hybrid and a fully synthetic. The hybrid media is 75 per cent paper and 25 per cent micro fibre. The newest filter is 100 per cent micro fibre. Now filter manufacturers have begun to pay more attention to reducing pressure loss because of the potential cold start issues. Many OEMs have found the premature wear and tear on their equipment, which can be attributed to unfiltered oil flowing through their systems during bypass events, such as pressure loss during cold starts. Hydraulic filters support the efficiency and long life of industrial equipment by removing micron size dusts and particles from the hydraulic fluid in the heart of the machinery. Hydraulic filters will continue to support the professional operators of construction and industrial equipment to protect them from danger in their work under severe conditions.</p><p> <span style="font-weight: bold;">Looking forward</span><br />Hydraulics always has been the best choice for high power-density applications, but new designs, materials, and manufacturing technologies are extending that advantage like never before. These new components are destined to be a smaller piece reducing the footprint and enhancing the power density. The latest trends point to customers looking for the best usage of space, better power density, energy efficiency, accuracy and quicker responses. The marriage of hydraulics and electronics will deliver smarter products that combine the intelligence of electronics with the power density of hydraulics to enable all of these applications and many more that have not ever been thought of yet. In the coming years, energy efficiency, fuel consumption, and the life cycle of the machines will become the major deciding factor.</p>