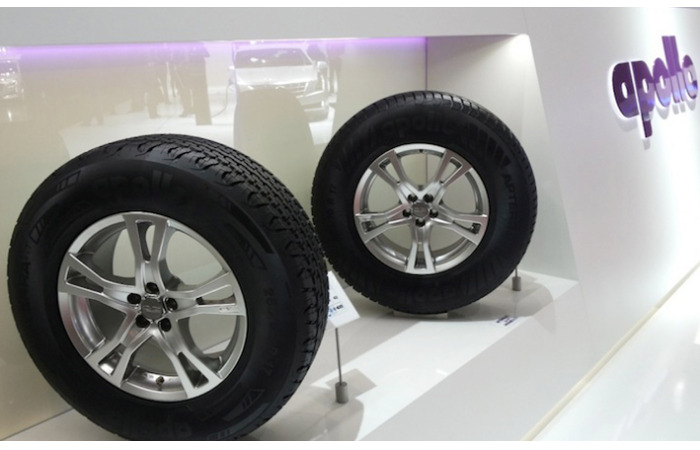
Apollo Tyres commissions greenfield facility in AP
Apollo Tyres commissioned its seventh manufacturing unit globally, and the fifth one in India, with the first tyre rolling out from the Andhra Pradesh greenfield facility. Located in Chinnapanduru village in Chittoor district of Andhra Pradesh (AP), this facility of Apollo Tyres is spread over 256 acres. The company will invest close to Rs 3,800 crore in the Phase I of this greenfield facility. While the capacity will be ramped up gradually in the next 12-18 months, as the demand improves, by 2022, this plant will have a capacity to produce 15,000 passenger car tyres and 3,000 truck-bus radials per day. With a modular layout, the capacity at this facility can be replicated with minimal engineering efforts and with economies on investments.
Commenting on the commissioning of the AP facility, Onkar S Kanwar, Chairman, Apollo Tyres, said, “This ultra-modern facility is a reflection of our growth aspirations and manufacturing capabilities, showcasing some of the best practices available across the globe in tyre manufacturing. This highly automated plant uses IT-driven systems and robotics, and employs young and skilled associates on the shopfloor, mostly hired locally. This plant mirrors the hopes and aspirations of the new self-reliant India. I would like to take this opportunity to thank the AP Government for all the support that they have extended towards setting up of this facility.”
The deployment of state-of-the-art manufacturing technologies at this facility will enable the company to target premium OEMs and after-market customers in India. This will further consolidate the company’s vision of providing world quality products to global markets.
Adhering to its environmental obligation, this facility has been designed to accommodate roof-top solar panels, to be introduced in a phased manner, for optimum usage of natural light for the shop-floor with an eco-friendly power source, and as a zero water discharge facility with an in-built effluent treatment plant. In addition, the company has ensured the usage of energy efficient utility and process equipments, and environment-friendly coolants. To improve productivity and reduce human fatigue, ergonomically balanced and weight optimised material handling equipment has been used across the facility. A ‘Spine’ like central utility corridor services both passenger car and truck radial units in a seamless fashion.