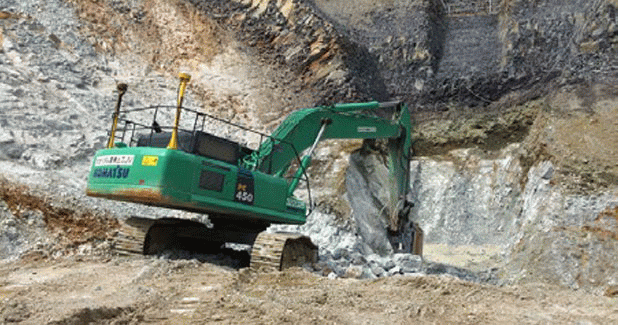
Increasing Productivity
Oitagawa Dam is a rock dam located in Kyushu, the third largest island in Japan. The island is mountainous and home to Japan?s most active volcano, Mount Aso. The new construction of Oitagawa Dam is an important infrastructure project for the island; the new dam will hold a total of 24,000,000 cu m of water. The city of Oita suffered a significant flood in 1953 making the development of the Oitagawa Dam a foundational piece to the city?s modern flood control and disaster prevention plans. Kajima, one of the country?s largest civil construction companies, was selected as the primary contractor for the massive excavation and civil engineering effort. Tomijima was appointed as the main earthworks subcontractor for project. Started in 2013, the first phase of the dam build includes breaking rock, removing rock and prepping the site area. In total, the team has moved 1.39 million cu m of earth, before the next phase which will involve building up the rock dam wall. Once constructed, the dam wall itself will be 100 m high by 500 m wide and will include 3.7 million cu m of rock and material. Because of the slope and vertical elevations required for meeting the dam design, Kajima and Tomijima were looking to use Intelligent Construction Technology (ICT). Kajima and Tomijima project manager consulted with the company?s technology partner NTJV to talk about project management and machine control options.
With support from NTJV, Tomijima equipped five excavators and five dozers with the Trimble GCS900 Grade Control System. They have also utilised four Site Positioning Systems Essentials Kits and deployed Trimble SPS620 total stations to conduct high accuracy structural works and checks. The Trimble Essentials Kits include the Trimble Site Mobile controller, Trimble SCS900 Site Controller Software and Trimble SPS985L GNSS Smart Antenna. The Tomijima team selected the mobile controllers and connected communication system so they would have the ability to send information from the field to the office - including design updates, GNSS corrections, telematics, and production information.
?With the SPS Essentials Kit the team can perform site survey and positioning tasks at the dam site without relying on full-time surveyors,? said Kajima Project Manager. ?Instead, field crews can collect positioning data like checking grades and elevations and calculate volumes of rock we removed compared to the material we have brought in.?
Operators used the hydraulic excavators with 3D GCS900 machine control systems to excavate for the dam according to the design. Traditionally, building a rock dam of this size would require the initial survey plus ongoing subsequent grade checking as dirt was being moved. That would involve checking and re-setting stakes close to where the excavator and rock crusher are working. Instead, with the Site Positioning Systems Essentials Kits and machine control, crews were kept out of harm?s way and there was 90 per cent less staking required compared to traditional methods.
With Trimble grade control, after an initial grade check, machine-mounted sensors calculate necessary bucket position to achieve the desired design. They also measure how much material must be moved. For about nine months, the GCS900 system was also used to guide the team?s rock breaker attachment for the excavator. Traditionally, this step is needed to prepare the dam?s foundation, breaking down the earth until the ground is solid enough to add fill for the dam material.
Following the design profile on the in-cab control box, the rock breaker removed rock and overburden across the dam site by breaking rock to 2-3 cm pieces. With the GCS900 systems, the team achieved a 150 per cent increase in productivity in managing and completing earthworks, moving 1.39 million cu m of earth.
?We tried different systems for the project and the Trimble GCS900 sensors were the only ones that survived the high vibrations caused by the rock breaker attachment,? said Tomijima Project Manager. ?The reliability and consistency of the system is amazing.?
The team used the breaker and twin-header attachments with Trimble guidance to cut excess material. This was critical to saving time and money, not only because of the extra work in over excavating but because additional material that would have to be used for backfill.
Tomijima also adopted VisionLink site productivity technology from Trimble for a holistic view of the project site and to track site productivity and materials movement. The system monitors and records 3D earthmoving operations across the project. Managers can also create real-time 3D surface models, elevation and cut and fill maps. With machine control and VisionLink, instead of taking an average of 2.5 hours to prepare and manage data, it now takes engineers on average of 30 minute each day an 80 per cent time savings in managing the earth moving process.
As of September 2015, the team has finished breaking down and moving rock totaling 1.39 million cu m of material. Next, Kajima and Tomijima are bringing in fill material to build the rock dam walls. This provides even more opportunity to utilise VisionLink to track loads of material and associated productivity and efficiency in the next phase of the project.
?With our success VisionLink and GCS900 are no longer specialty technology, it?s standard technology required for this type of job.? said Kajima Project Manager. ?By working with the best technology and staying focused on productivity, we can accomplish high quality work and have a safety as a top priority.?
Customer Profile: Kajima Corporation is one of the most famous general contractors in Japan. Tomijima Construction Co Ltd is an engineering and infrastructure contractor founded in 1954 in Japan.
Business Challenge: Kajima selected Tomijima as the primary subcontractor to build the Oitagawa rock dam on the southern island of Kyushu. Looking to improve excavation productivity and to keep the crew out of harm?s way, the company turned to Trimble for help through Nikon-Trimble Joint Venture (NTJV).
Solution: The VisionLink? solution, Trimble GCS900 Grade Control System with specialist attachment support, Site Positioning Systems Essentials Kit and Total Stations
Benefits:
- 50 per cent increase in earthwork management productivity
- 90 per cent less staking required than traditional methods
- Reduced data prep and management from 2.5 hours per day to 30 minutes per day 80 per cent time savings for managing earth moving operations
- Removed debris and cleared rock to prep the site