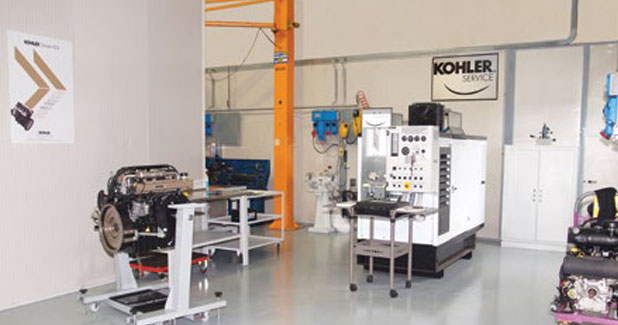
Kohler Engines: Service 2.0
Having designed the family of KDI engines, technologically advanced and the benchmark for industry standards within the sector, Kohler Engines is implementing sweeping innovations in the field of technical assistance. This approach includes new digital tools as well as modern methods for providing training and technical support, for the full utilisation of such systems. The tools and methods take complete advantage of a service network which effectively covers the entire planet.
An innovative approach
A radically innovative approach was taken by Kohler Engines when it took this step. The new approach is based on a solid foundation: an organisational framework in which assistance with diesel engines is coordinated from the Group?s headquarters in Reggio Emilia, Italy and offered by a worldwide service network supported by European branch offices (in France, Spain, Germany and England) and Service Departments in North America (Kohler, Wisconsin), China and Pacific Asia (Shanghai), and Central and South America (Mexico City).
For the KDI line - the first industrial diesel engines to use a 2,000-bar common rail injection system - the?Technical Assistance and Replacement Parts? Division of Kohler Engines has drawn up a series of special requirements for workshops that wish to join the network of?KDI Qualified? service centres, whose technical personnel receive training that is specifically targeted for this line.
Technical assistance
From Italy, and in particular from its Reggio Emilia headquarters, the Technical Assistance department provides documentation, initial training and technical support to all branches around the world, which in turn cover their specific territories and create networks of dealers and authorised workshops. In doing so, they directly supervise OEMs that intend to perform repairs and service on KDI engines directly through their own dealer networks. This highly structured service organisation now includes some 1,500 service locations in Europe, which are flanked by those OEM dealers that directly service the engines in their machines.
At the heart of this new service philosophy is the concept of training, now carried out in both traditional forms and with modern digital tools. The former includes courses offered not only to the service network, branches, distributors and authorised workshop networks, but also to trainers at dealers and at authorised OEM workshops.
Courses are available at both at the Reggio Emilia headquarters as well as distributors? locations. They consist of a technical unit and a practice section that involves installation/removal and dynamic testing. The duration of each course depends on the model of engine involved. Traditional courses in the classroom are accompanied by an innovative?Distance Learning? section - a remote training tool included in the?iService? multimedia platform. It combines traditional viewing of technical manuals with the enhanced usability offered by advanced digital technology. iService is designed to meet the needs of the service network and of end users, as it contains user-friendly interactive content that is easy to access and navigate on PCs, smartphones and tablets. It?s a unique platform that contains the entire gamut of after-sale materials offered by Kohler Engines, such as operation and maintenance manuals, workshop manuals, parts catalogues and warranty programs.