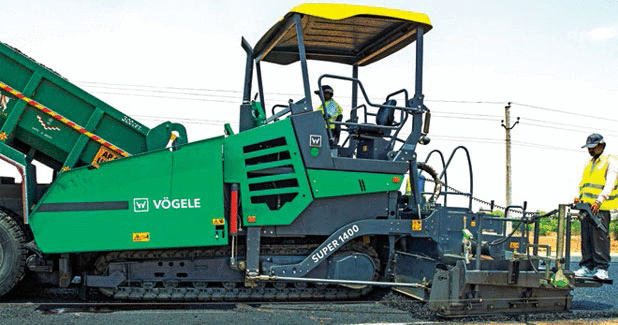
Paving to perfection
<span style="font-weight: bold;">Asphalt paver market is growing in India in numbers and quality with more and more contractors are shifting towards sensor pavers from mechanical pavers. </span><br /><br />Asphalt paver market is likely to flourish in the coming years as more rural roads and highways are in the offing. The Budget 2018-19 has major focus on extension of 3.17 lakh km of rural roads which are largely asphalt roads. There is going to be a lot of requirements for asphalt pavers in meeting the set target of executing road projects in future. While rural roads use mechanical pavers, highway constructions are mainly using sensor pavers which give better quality in road construction.<br /><br /><span style="font-weight: bold;">Wheeled vs tracked</span><br />Tracked and wheeled pavers are equally important for paving applications, depending on various factors. Wheeled pavers are more mobile compared to tracked ones and they can offer quick job-to-job movement. However, long crawler tracks with large footprints provide for maximum tractive effort than with wheels, allowing the tracked paver to progress well at a constant speed even when operating on difficult terrain. Weight is spread evenly across the tracks; distributing the pressure across the paver, and therefore they perform better in soft sub-base conditions. On the other hand, you have to be careful when paving on soft surfaces with the wheeled counterpart so that it does not spin down into the material and get stuck. <br /><br /><span style="font-weight: bold;">Ramesh Palagiri, Managing Director & CEO, Wirtgen India </span>explains scenario in India, 'In India, for wheeled segment pavers, the 5-6 m class is popular. For the tracked segment, pavers with a paving width of 7 m to 13 m are commonly used where 7 m and 9 m paver being the fast moving in the track segment.'<br /><br /><span style="font-weight: bold;">Pavers on offer</span><br />Indian market has presence of technologically advanced pavers with the presence of many national and international manufacturers. Volvo CE, a global player in pavers which has manufacturing facility in India, offers tracked pavers (P6820C ABG and P5320B ABG) and wheeled pavers (P4370B ABG). <span style="font-weight: bold;">Dimitrov Krishnan, Vice President and Head, Volvo CE India</span> comments, 'Volvo CE is widely regarded as one of the leading innovators in the field of construction equipment and we are proud to be driving advances in the technology of existing road construction machines, like pavers with sensorsùthe P4370B ABG and P5320ABG.' <br /><br />Both the P4370B ABG and P5320ABG sensor paver models are made at Volvo's Bangalore plant. <br /><br />They deliver maximum paving widths of 7 m, a paving output of 600 tonne per hour and are powered by an 88 kW engine, which delivers high power with minimal noise and low fuel consumption. The P4370B ABG is a wheeled sensor paver which delivers a basic paving width of 2.5 m, while the P5320B ABG is a tracked sensor paver which delivers a basic paving width of 4.5 m.<br /> <br />The P5320B ABG also boasts innovations such as load-sensing hydraulics, so that hydraulic output is perfectly matched to all components. An automatic hydraulic track tensioner delivers smoother operation while simultaneously reducing wear and downtime. The Volvo Omni V screed provides variable width on the go. The electronically-ignited gas heating system, designed with flame failure protection, quickly and efficient heats the screed plate, while the LPG blower burner <br />system provides uniform heat for a smooth mat finish, with quality pre-compaction.<br /><br />Wirtgen India is offering the Vogele range of sensor pavers in India. 'Vogele has been the industry pioneer as well as the market leader for asphalt pavers. The Vogele range of sensor pavers can pave from 1.5 m paving width to a maximum of 16 m - the widest range,' claims Palagiri.<br /><br />He further elaborates on the features, 'Vogele has introduced several innovations like the pressure bars and electric heating of the screed, Niveltronic plus operating concept and Ergo plus operator features. With our Dash -3 pavers, we also offer the Eco plus which helps in saving fuel, Auto set plus, Pave dock assistant etc.' <br /><br />Vogele also offers several other technologies like the Spray Jet paver which does the tack coat and paving with the same paver, Mobile Power feeders which are now being used for building of airport runways and expressways, and the Inline paving technology. <br /><br />According to Palagiri, the most recent innovation from Vogele is the Road scan which helps the operator of the paver to know the exact temperature of the mix, as it is being paved, and also later through the recorded data.<br /><br /><span style="font-weight: bold;">Mechanical vs sensor pavers</span><br />Mechanical pavers are the most economical and efficient solution while sensor pavers are advanced pavers with intelligent monitoring systems. Mechanical pavers, though economical, cannot provide a smooth finish to the surface. In turn, this affects the traffic flow of the highway and increases maintenance requirements in the finished road. Sensor pavers have intelligent operating technology that helps control the machine in terms of mat thickness as well as the level of the mat and the grade required in the finished road. <br /><br />Krishnan elaborates on the advantage of sensor pavers over mechanical pavers, 'The paving quality of any road is defined by the ability of the paver to satisfy three requirements in line with the highway design: mat thickness, level of the mat, and the grade required. <br /><br />Regular pavers without sensors simply follow the undulations of the road base and are therefore unable to give a smooth finish to a paved surface. But sensor pavers have intelligent operating technology that helps the machine deliver on these three requirements.'<br /><br />Palagiri echoes the same as he says, 'In highway segment, use of sensors pavers play a very important role in getting the right levels and grades when building the roads. <br />The final finish of the road depends, to a great extent, on the accuracy delivered by these pavers, in addition to the mix quality and temperature at which it is laid and also compaction.'<br /><br /><span style="font-weight: bold;">Market scenario</span><br />The current market scenario is demanding more pavers of advanced features. Says Palagiri, 'The market is definitely moving from mechanical to sensor pavers and we estimate the total market for sensor pavers to be more than 300 units per annum.'<br />Krishnan observes, 'In the next five years, the Union Government plans to invest Rs 7 trillion ($108 billion) to build 83,677 km of roads-a huge boost for India's infrastructure. The Indian Government's plans to increase speed of road construction from its current level of about 23 km a day to an eventual 40 km a day have made road pavers, particularly sensor pavers, increasingly important for projects around the country. We see a host of opportunities for the road building sector and remain one of the industry's key players.' <br /><br /><span style="font-weight: bold;">Market opportunities</span><br />Looking at the pace at which the road construction is progressing in the country, road equipment segment sees a considerable demand in future. Says Palagiri, 'We expect the market for asphalt pavers to grow by 20-25 per cent per annum.'<br /><br />The government continues to place priority on building roads and bridges-allocating budget to build 35,000 km of road under phase one of the Bharatmala project, along with allocations for urban rail and airport expansion projects. The drive to improve infrastructure will unquestionably facilitate further growth in the economy and the construction equipment industry, according to Krishnan. He adds, 'As a company, Volvo Construction Equipment has deep roots in India and an established sales and support network. We are well-positioned to play our own part in the India's development and are excited to do so. We remain the only major manufacturer present in all equipment sectors: mining, road building or general construction.'<br /><br />With the government's thrust on quality in highway construction, sensor paver market will perform better in future, while mechanical pavers will continue to perform in rural road projects.<br /><br /><span style="font-weight: bold;">Simplifying transfer of mix</span><br />Continuous transfer of mix on the B271: in the vicinity of a motorway exit on the B271 federal highway, a SUPER 1800-3i with PaveDock Assistant ensured uninterrupted paving. <br /><br />Even in conventional paving, there are some challenges to overcome. Working without interruptions, for instance, and avoiding the jolts caused by the feed lorries as they dock. Both of these criteria can now be met perfectly thanks to a current Vögele innovation: PaveDock Assistant. This is Vögele's name for one of the options offered for their Dash 3 paver generation - operating on the principle of a signal light, it improves communication on the job site and actively supports the lorry driver when docking. The system excelled in every respect when paving the surface course for the modification of an exit on the B271 federal highway.<br /><br /><span style="font-weight: bold;">Milestone for greater process reliability during transfer of the mix</span><br />In practice, the procedure on the Bad Dnrkheim job site was as follows: the SUPER 1800-3i used two signal lights to indicate clearly whether the feed lorry was to reverse, stop, dump mix or drive off again. The signal lights are positioned high up on the hardtop of the machine, where they are easily visible to the lorry driver <br />at all times. One of the key advantages is that the PaveDock Assistant eliminates the need to use horns in job site traffic. This wide-spread practice is not only unreliable û particularly when paving with multiple pavers û but also annoys local residents and confuses <br />vehicle drivers.<br /><br /><span style="font-weight: bold;">Easy handling from the paver operator's ErgoPlus 3 console</span><br />For the paver operator, changing signals to pass on instructions to the lorry driver is a simple and intuitive process from his ErgoPlus 3 console. All functions of the SUPER pavers are integrated into the innovative, easy-to-learn operating concept from V÷gele. Thanks to the PaveDock Assistant, docking feed lorries did not cause a single jolt on the B271 job site. Jolts are dreaded, because they affect the screed and can leave imprints on the freshly paved <br />asphalt course.<br /><br /><span style="font-weight: bold;">- Sudheer Vathiyath</span><br />