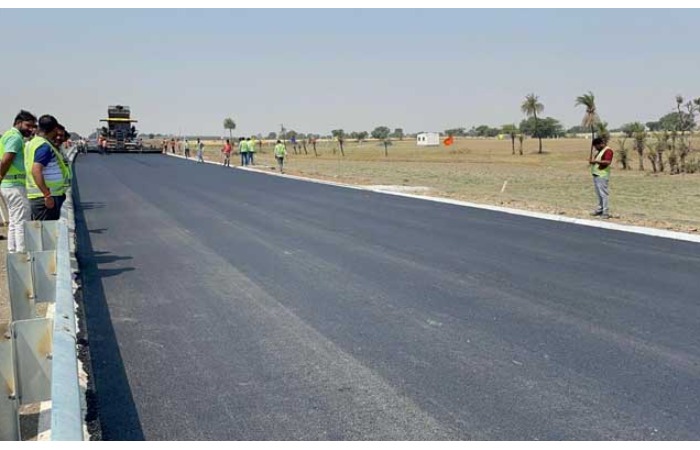
Steamrolling Ahead
In road construction, the challenge of keeping up with an ambitious pace of execution while ensuring high-quality outcomes is paramount. Recent forecasts predict a decline in the daily road construction pace, estimating only 31 km to be built per day in 2024, compared to 34 km per day in 2023. This highlights the growing importance of utilising best practices and cutting-edge technologies to boost productivity, reduce downtime, and ensure top-notch results. Among these technologies, modern compaction equipment is playing a crucial role in shaping the future of construction, improving efficiency, and enhancing the quality of the finished road surface.
Compaction is a fundamental process in road construction, ensuring the stability, durability, and smoothness of the pavement. Historically, compaction equipment such as rollers and compactors have evolved significantly, with technological advancements aimed at improving their performance, ease of use, and impact on the environment.
The introduction of machines like the CASE 952 NX Vibratory Compactor and CASE 450 NX Vibratory Compactor is a testament to how the industry is embracing innovation. The CASE 952 NX, for instance, features a suspended frame concept that ensures superior kerb clearance and improved performance. Powered by a CEV Stage V compliant engine, the 952 NX ensures optimal power delivery while reducing emissions—a crucial factor for meeting the latest environmental standards. Its two-stage vibration system, advanced telematics, and ergonomic design for operator comfort further enhance its appeal for large-scale construction projects.
Similarly, the CASE 450 NX is engineered for compact spaces, offering exceptional maneuverability and fuel efficiency. With its advanced vibration system, efficient compaction force, and a user-friendly operator interface, the 450 NX has redefined the compaction experience for contractors. The integration of myCASE Construction Telematics provides real-time data that helps operators track performance and improve fleet management.
Shalabh Chaturvedi, Managing Director, CASE India & SAARC, said, “CASE’s legacy of creating world-class products has always been the primary commitment. Our ‘Made in India’ initiative is a cornerstone of our strategy. Our products are not just designed to meet the unique demands of the Indian market, but also built to serve global needs, reinforcing our ambition to position India’s manufacturing excellence on the world map.”
Intelligent Compaction
One of the most promising developments in compaction equipment is the advent of intelligent compaction technology. This involves the use of sensors to monitor and control compaction quality in real-time, ensuring the correct density is achieved without over-compaction, which can lead to wasted time and resources.
As explained by Arppan B Ghosh, President – Engineering, Cube Highways Technologies, intelligent compaction works by incorporating a non-nuclear density gauge that provides continuous feedback on the compaction level. This system significantly reduces the need for manual inspection and ensures that over-compaction—often caused by human error—does not occur. Ghosh advocates for the broader use of intelligent compaction, noting that while the technology is currently deployed in isolated projects, its cost-effectiveness (only 3 to 6 per cent more expensive than traditional compaction) makes it a worthy investment for future projects.
Intelligent compaction not only ensures consistent quality but also prevents damage to the underlying layers of the road. For instance, projects involving stone matrix asphalt as the wearing course are particularly sensitive to over-compaction, as it may crush the aggregate. In such cases, intelligent compaction helps contractors avoid this issue by delivering precise data on compaction levels, allowing for adjustments in real time.
Professor Nikhil Saboo, Assistant Professor, IIT Roorkee, further emphasises that intelligent compaction significantly reduces the labour-intensive nature of the task. The sensors integrated into the compactor can track parameters such as moisture content, vibration frequency, and amplitude, which are critical for achieving optimal compaction. This real-time monitoring not only speeds up the process but also ensures uniformity across the entire construction site, resulting in better quality road surfaces.
Best Practices in Compaction
To maximise the potential of advanced compaction technologies, industry leaders emphasise the importance of best practices that streamline operations and improve outcomes.
Pre-planning is another key practice recommended by Atasi Das, Assistant Vice President, GR Infraprojects. Ensuring that material requirements for the next day's work are confirmed in advance eliminates lags between different teams, such as QA/QC, highway teams, and mechanical teams. Weather conditions also play a crucial role in the quality of the final pavement. Das suggests monitoring environmental factors such as temperature, humidity, and wind speed, as these directly influence the concrete’s behaviour. At GR Infra, a mobile construction quality monitoring van is used to track these parameters and prevent issues like rapid evaporation and shrinkage cracks.
Moreover, eliminating stoppages during compaction is a key element in maintaining a consistent paving speed. At GR Infra, a technique called “time precision” is applied to determine the dormancy period before the initial saw-cutting of joints in concrete, preventing unnecessary joint formations. This practice significantly improves the smoothness of rigid pavements, enhancing both performance and longevity.
Integrating Technology
While the advantages of intelligent compaction and other advanced technologies are clear, there is a pressing need for government support to accelerate their adoption. As Ghosh points out, the widespread use of intelligent compaction is still limited to isolated projects. The lack of clear guidelines from authorities has hindered the full-scale implementation of these technologies. To unlock their potential, it is crucial for governments to specify the use of intelligent compaction in road contracts and concession agreements, ensuring that these technologies are deployed on a broader scale.
Similarly, other technologies such as material transfer vehicles (MTVs), which prevent thermal segregation and ensure consistent paving quality, have not yet been mandated by government standards. Ghosh notes that MTVs are particularly useful in preventing undulations and inconsistencies during the transfer of hot-mix asphalt from trucks to pavers. These vehicles allow for smoother, more efficient paving operations, leading to longer-lasting roads.
Energy-Efficient Technologies
In addition to improving quality, many industry leaders are focusing on sustainability in road construction. Cold-mix and warm-mix technologies, which use lower temperatures to create asphalt, are gaining traction for their energy efficiency and reduced carbon footprint. These technologies are particularly beneficial in reducing the environmental impact of paving operations, making them an attractive option for contractors and governments alike.
As Satyanarayan Purohit, Vice President, Dilip Buildcon, highlights, cold-mix technology minimises carbon emissions and is currently being used on a case-by-case basis in India. Similarly, warm-mix technology allows asphalt to be compacted at lower temperatures than traditional methods, consuming less energy and reducing the overall environmental impact of road construction.
Purohit also notes the growing use of micro-surfacing, a cold-paving technology that offers lower carbon emissions and greater efficiency. This technology has been successfully implemented in various Indian states, including Jharkhand, Madhya Pradesh, and Haryana. By using these energy-efficient methods in combination with high-capacity rollers and thin layers, contractors can achieve precise and efficient paving, further improving the quality of the finished road.
Safety in Selecting Compaction Equipment
The top priority in road building is crew member safety. But conventional compaction equipment is about as inflexible as it gets. Operators sweat down the sloping road shoulders and ditches, risking a rollover but praying for the best as they feel every degree of slope. Although rollover protective structures (ROPS), seatbelts, and personal protective equipment (PPE) like hard helmets have been demonstrated to be effective at saving lives in compactor rollover accidents, they are not very effective for averting a disaster altogether.
Some manufacturers are redesigning the compaction process from the ground up in order to overcome the main challenges posed by conventional compaction rollers, including risk, excessive maintenance, and limited utility. When considering a new compaction roller, here is what to look for.
Manufacturers' perception that the compaction drum is a source of motion, compaction, and stability all in one has been the main barrier to compaction safety. On the other hand, the safety concern is quickly resolved by moving the drum to an offset arm attachment. The compaction roller can now be linked to graders, compact track loaders, wheel loaders, or skid steers as an accessory. These hosts offer a separate source of power for the compaction drum as well as stability and operator safety due to the offset arm.
With this configuration, an operator is now able to compact level areas as well as run the host machine on flat ground while the arm extends to the farthest, steepest edge of sloping road shoulders and ditches. Improving safety to this extent puts a major dent in workers comp claims, lowers insurance premiums, and increases safety ratings — a necessity to contractors bidding on competitive jobs.
Shifting the drum to an offset arm attachment drastically improves safety, but it can also unlock a host of other benefits.
The onboard engine, transmission, and other connected equipment are no longer present because the compaction roller is now an independent device. Look for an attachment that offers a universal mounting pad and straightforward hydraulic connections for a smooth setup and disconnect to the host machine to further save downtime.
Think about remote-controlled possibilities as well. The operator can make all adjustments from the palm of their hand and without leaving the host machine's cockpit using certain compaction roller attachments that can be quickly attached to the remote.
Typically, aside from a handful of grease fittings to maintain and clean off debris, compaction roller attachments have no maintenance to speak of — no more oil changes, filters, transmission fluid or any hard parts to wear and break. This can make for 90 per cent less maintenance over self-propelled machines. Cutting out the unnecessary bulk seen with traditional compaction machines also allows manufacturers to design a more compact, versatile machine.
Compaction roller attachments can easily surpass their conventional equivalents in every way during a busy roadwork season. These attachments prevent an engine from lying idle and progressively deteriorating into a surprise repair charge when the next season comes along. But more crucially, offset-designed compaction roller attachments boost crew safety and offer a multipurpose piece of machinery that will outlast any conventional compaction machine in a road crew’s fleet. Customers may buy with confidence knowing that they will receive the best possible return on their investment.
The Road Ahead
Looking toward the future, the focus is shifting to advanced materials that enhance road performance. One such material is stone mastic asphalt (SMA), which is being used on high-traffic expressways like the Delhi-Katra and Delhi-Vadodara expressways. SMA is highly rut-resistant and offers superior flexibility and moisture resistance, making it an ideal choice for roads subjected to heavy traffic. Though it is more expensive due to its use of polymer-modified bitumen, SMA’s durability and longevity make it a worthwhile investment in the long run.
The future of road construction is undeniably tied to technological innovation. From intelligent compaction systems to sustainable paving methods, the integration of advanced technologies is transforming the industry. However, for these innovations to reach their full potential, it is crucial for industry leaders, contractors, and governments to work together to implement best practices, adopt energy-efficient technologies, and ensure the widespread use of intelligent compaction. Only then will the road construction industry be able to meet the growing demand for high-quality, durable, and sustainable infrastructure.
As compaction equipment continue to evolve, the need for precision, efficiency, and sustainability will drive the next wave of innovation in road construction. By leveraging intelligent systems, adopting best practices, and prioritising environmentally friendly technologies, the industry can accelerate its pace without compromising on quality, ensuring that the roads of the future are built to last.
QUICK BYTES:
- The compaction equipment market is around 4,000 machines annually.
- The market growth will depend on the speed of execution of the road projects.
- The market is anticipated to flourish at a healthy CAGR of 6.4 per cent between 2023 and 2033.
Challenges in compaction equipment segment
Despite the promising trends, the compaction equipment market in India faces several challenges that need to be addressed for sustained growth.
- High initial costs: The capital-intensive nature of compaction equipment poses a significant barrier for small and medium-sized construction companies. The high initial costs of purchasing advanced compaction machinery often deter potential buyers, hindering the widespread adoption of modern technologies.
- Limited awareness and training: A lack of awareness and training on the benefits and operation of advanced compaction equipment is a challenge in the Indian market. Many construction professionals may not be fully aware of the latest technological developments or the potential efficiency gains associated with automated compaction. Bridging this knowledge gap is crucial for the successful integration of advanced equipment.
- Infrastructure and connectivity issues: Remote monitoring and control systems heavily rely on robust internet connectivity. In many construction sites across India, especially in rural or remote areas, inadequate infrastructure and connectivity pose challenges for the effective implementation of automated and remote-controlled compaction equipment.
- Environmental regulations: While there is a growing demand for eco-friendly equipment, stringent environmental regulations can pose challenges for manufacturers. Adhering to emission standards and sustainable manufacturing practices adds complexity to the production process, potentially affecting the cost and availability of compaction equipment.