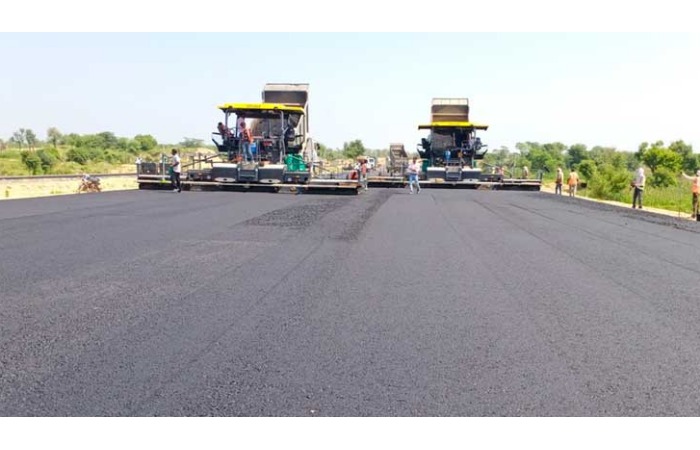
Impressively Wide, Incredibly Accurate
The Delhi-Mumbai Expressway is one of the most prestigious expressway projects in India in current time. The highway will start near Gurugram at Sohna and will end at JNPT, near Mumbai. With a total length of 1,353 km, the expressway is divided into 49 packages (31 packages in Delhi-Vadodara section, 13 packages in Vadodara-Mumbai section and five packages in Mumbai-JNPT section). The eight-lane expressway is being built under the engineering, procurement and construction (EPC) route and would reduce the distance between the two cities by over 150 km and cut travel time to 13 hours from 24 hours now. Likely to be ready by 2023-24, the project was necessitated because of heavy congestion on the Delhi-Mumbai National Corridor along the NH-48 of the Golden Quadrilateral. Passing through Haryana, Rajasthan, Madhya Pradesh, Gujarat and Maharashtra, the Delhi-Mumbai Expressway would also provide easier connectivity to the cities of Jaipur, Kota, Chittorgarh, Indore, Ujjain, Bhopal, Ahmedabad and Vadodara.
Background
It is required to pave the width of road in multiple lanes because paving the full width of the pavement in a project like Delhi-Mumbai Expressway is usually impossible. In this project, flexible pavement section has base layers such as WMM width of 19.55 m and bituminous layers vary in width from 19.25 to 18.75 m.
Most often, differences in the temperature and mat plasticity cause an improper bonding of the fresh hot mix asphalt with the older asphalt lane and this subsequently causes the longitudinal joint to possess a significantly lower density than the rest of the pavement. Over time, a longitudinal crack usually occurs between the asphalt mats, permitting the intrusion of water, increasing roughness, and potentially limiting life of the pavement.
While deliberating and adopting the paving methodology in such kind of a project, one of the most important factors comes to mind is longitudinal joint type and its position. The objective is to have a strongly interlocked joint which provides the same sealing effect as that of the other part in carriageway to avoid water intrusion into the layer and thus avoid oxidation and raveling of pavement. While there are several conventional methods of joint preparation, making and repair, somehow hot and hot joint proves to be the best among all because of its paving methodology and way to address the base from where generally the problem and defect starts.
Let’s know about some other highlights of Hot and Hot Paving, which is also known by the name ‘Echelon Paving’.
Paving ‘Hot to Hot’
Paving with two or more pavers in echelon is ideal for an integral bond between asphalt strips. In this paving method, the distance between the pavers is to be kept as short as possible to have minimum temperature difference between the paved lanes.
The first roller following each paver should be of the same size. The rollers start rolling towards the joint from the outer pavement edge inward. Compaction ends approx 15 cm beside the longitudinal seam on either side. The joint is then the last strip to be compacted by the rollers. This way, a tight bond between the strips is obtained.
Benefits of Echelon Paving:
Technology from VÖGELE
VÖGELE is supporting the nation’s vision of building world-class roads in the country by serving its customers with the Super 1400 asphalt pavers (Make in India) and state-of-the-art German technology asphalt pavers like the Super 1800-3 (10 m) and Super 2100-3 (13 m).
VÖGELE’s seamless product range
VÖGELE’s seamless product range is considered unique in the industry. Whether a service road or a highway, an airfield or a race track, a new construction or a rehabilitation job, thick or thin, hot or cold – customers will find the right machine in its product range for every paving task. The products range from pavers with state-of-the-art screeds to material feeders which are particularly suitable for large-scale job sites and digital solutions for Road Construction 4.0.
The extensive product range of VÖGELE is divided into two lines: the Classic Line and the Premium Line. The Classic Line is for pavers equipped with the particularly easy-to-use ErgoBasic operating concept. The Premium Line comprises all pavers that feature cutting-edge technology and advanced mechanical engineering. Premium Line products are all equipped with the ErgoPlus 3 operating concept. The varied range of asphalt pavers has paving width ranging from 3.5 m to 18 m in single pass.
With its seamless product range, VÖGELE can cover its customers’ every requirement anywhere in the world. The company helps its customers secure success with innovative machinery and solutions. Being the No. 1 in innovative technologies is consequently one of the guiding principles of its business activities. Advancements in engineering are all well and good – but for VÖGELE, the focus is on turning these advancements into solutions that benefit customers.
In the current scenario, the Delhi-Mumbai Expressway itself is one of the biggest examples of the latest technology and high-quality paving by VÖGELE asphalt pavers throughout the length. In the past, Wirtgen Group had continuously proved high quality results from its machines in Indian road construction whether it is Yamuna Expressway, Agra-Lucknow Expressway, Buddh International circuit, Purvanchal Expressway, Jaipur Ring Road, or various airports etc.